7 minute read
TECHNICAL GURU
Heating
By: Amy Stone, Aquatic Equipment and Design, Inc.*
Heating and cooling can both be big capital expenses as well as big hits to the operating budget; however, they are essential parts of an Life Support System (LSS) when it comes to growth rates, survivability, and year-round profitability.
This article will focus on heating. Temperature control becomes a real concern when the animals that are being cultured have different requirements than the naturally occurring water, whether year-round or just seasonally. There are several ways to maintain water temperature in systems.
Flow Through Systems Flow through systems require that the heating system be able to increase the temperature of the water in a single pass. Meaning, the heating system will only process the water once and it will never return through the heater. Electric and gas heating can be cost prohibitive in these designs. Large shifts in temperature and high
flow rates add to the expense exponentially in these applications.
For flow through systems, the recommendation would be to reduce the heating requirements as much as possible and consider a geothermal approach, which will be discussed later. Geothermal systems can also have a large upfront capital expense, as you need a subterranean well or heat sink and these can be costly.
With all flow through applications, you must consider heat recovery as a highly efficient and cost-effective option. Heat recovery involves using the effluent flow of water you have already heated to “pre-heat” the incoming water to your system using a plate heat exchanger. This can typically save up to 50% or more on heating loads and makes using gas/ electric heaters a more viable option.
Recirculating Systems Recirculating systems allow the water to pass through the heating device multiple times, which allows the
Boilers at alligator farm.
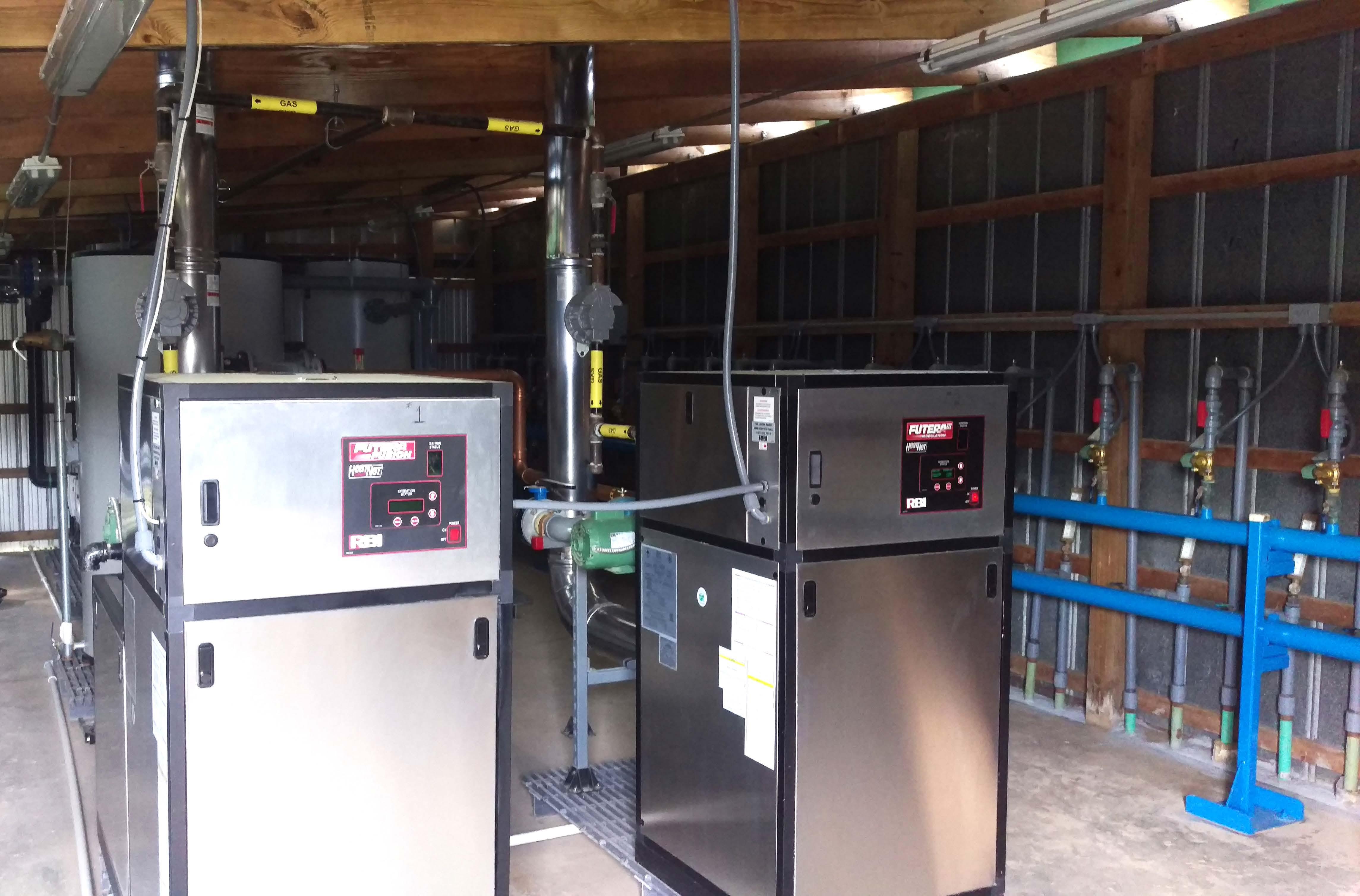
heater to bring up the temperature of the water more slowly than if a large change in temperature is required in a single pass. Recirculating systems require larger and more robust filtration systems compared to flow through systems, but the heating system is significantly smaller for a similar sized flow through application.
Heating Calculations In general, it takes 2.44 Watts (8.33 BTU’s) to raise 1 gallon of water 1 degree Fahrenheit. However, depending on factors in the system, it can be anywhere from 2.44 Watts to 24 Watts, or more to achieve that same temperature change. Say what???? Why is there such a big range? How do you design your system properly to keep the animals healthy and growing? It’s more complicated than it may appear at first.
First and foremost, what temperature range is required? Most animals can accommodate a range of temperatures. It’s important to know what the range is but also keep in mind the optimal temperature range which is where the best growth rates occur. Time is money so it is best to keep the animals in their optimal growth range.
For a flow through system, the heating calculation is fairly simple since you are heating up water in a single pass to a desired temperature. A quick calculation you can use is: GPM X ΔT X 60 = BTU/HR *ΔT is equal to your desired water temperature minus your incoming water temperature.
As you can see, the higher the flow rate and larger the ΔT is, the higher the BTU load is. Keep in mind in many places the incoming water temperature is not constant. For heating, you need to size your heating system for the lowest temperatures your system will see (typically mid-winter).
For recirculating systems, the temperature calculations become a bit more complex.
The first parameter to consider is your volume control load. This means in a given 24-hour period, how many degrees do you want to be able to increase the entire volume of water in the system. This number can vary
Temperature control becomes a real concern when the animals that are being cultured have different requirements than the naturally occurring water, whether year-round or just seasonally.
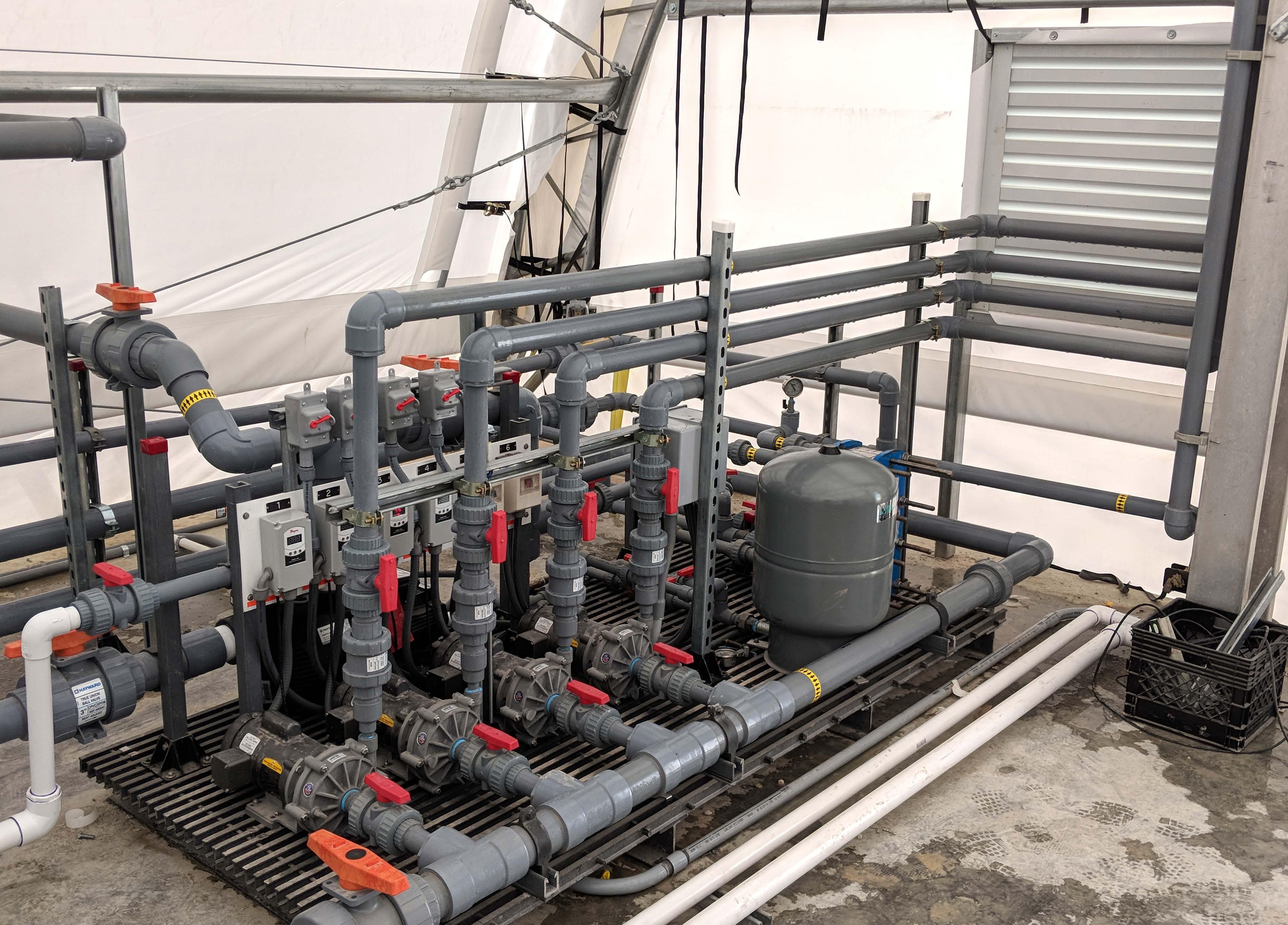
greatly depending on the size and application of the system. To calculate your volume control load:
Volume (GAL) x X/24hr x 8.33BTU/GAL = BTU/HR X = number of degrees F you want to be able to change your system in a given 24-hour period.
The next parameter is the ambient (air) temperature that the surface area of the water will be exposed to. Most heat energy in a system is lost through water to surface exchange making this a very significant portion of the overall heat load. This is where most of the calculations fall apart. In many cases, the end user will estimate the lowest temperature without any empirical data. If the estimation of ambient temperature is not as low as the system will actually be exposed, then the heater will be undersized and cause the water to be outside of the recommended range. If the estimation of ambient temperature is too low, the heater will be oversized causing an increase in capital expenditures and possibly causing the heater to cycle more often. This calculation has many factors such as sunlight, wind speed over tanks, air humidity, etc. A couple ways to mitigate surface area heat loss is to control ambient air temps or tent the tanks to create a microclimate to limit evaporation.
Finally, considerations need to be made for tank wall thickness, water exchange information, mechanical heat gains, biomass heat gain of fish in the system, aeration and sometimes more factors, depending on the application.
Types of heaters Immersion Heaters These are relatively small heaters that are immersed directly into the system water, usually in a collection sump or sometimes directly in the culture tank. These units can be electric immersion heaters or water-water heat exchangers. They are available in stainless steel, titanium and other metals. We usually only use titanium to avoid the possibility of corrosion. Hydronic Buffer Tank & Pumping Skid.
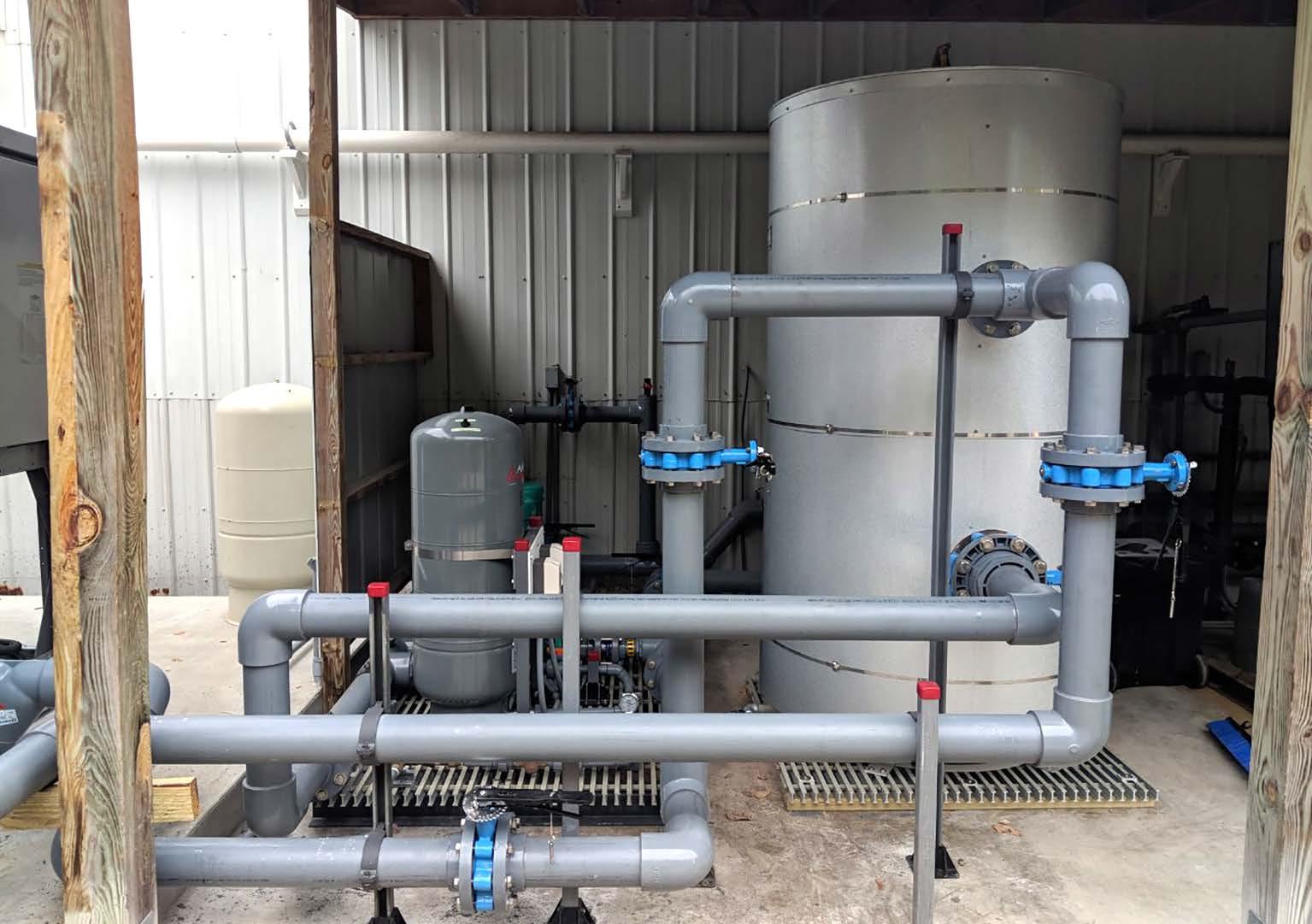
Installed Grid Coil Heat Exchanger.
In hard water, these heaters are prone to calcium build up which can create a hot spot. If this is not cleaned in a timely period, the heater will fail. This also voids any warranty that the manufacturer included.
These heaters are available as fully submersible and with a riser tube and junction box on the top. Except for the really small heaters, they all have an external controller. In the units that use less than 15 amps, the controller is available pre-wired and is
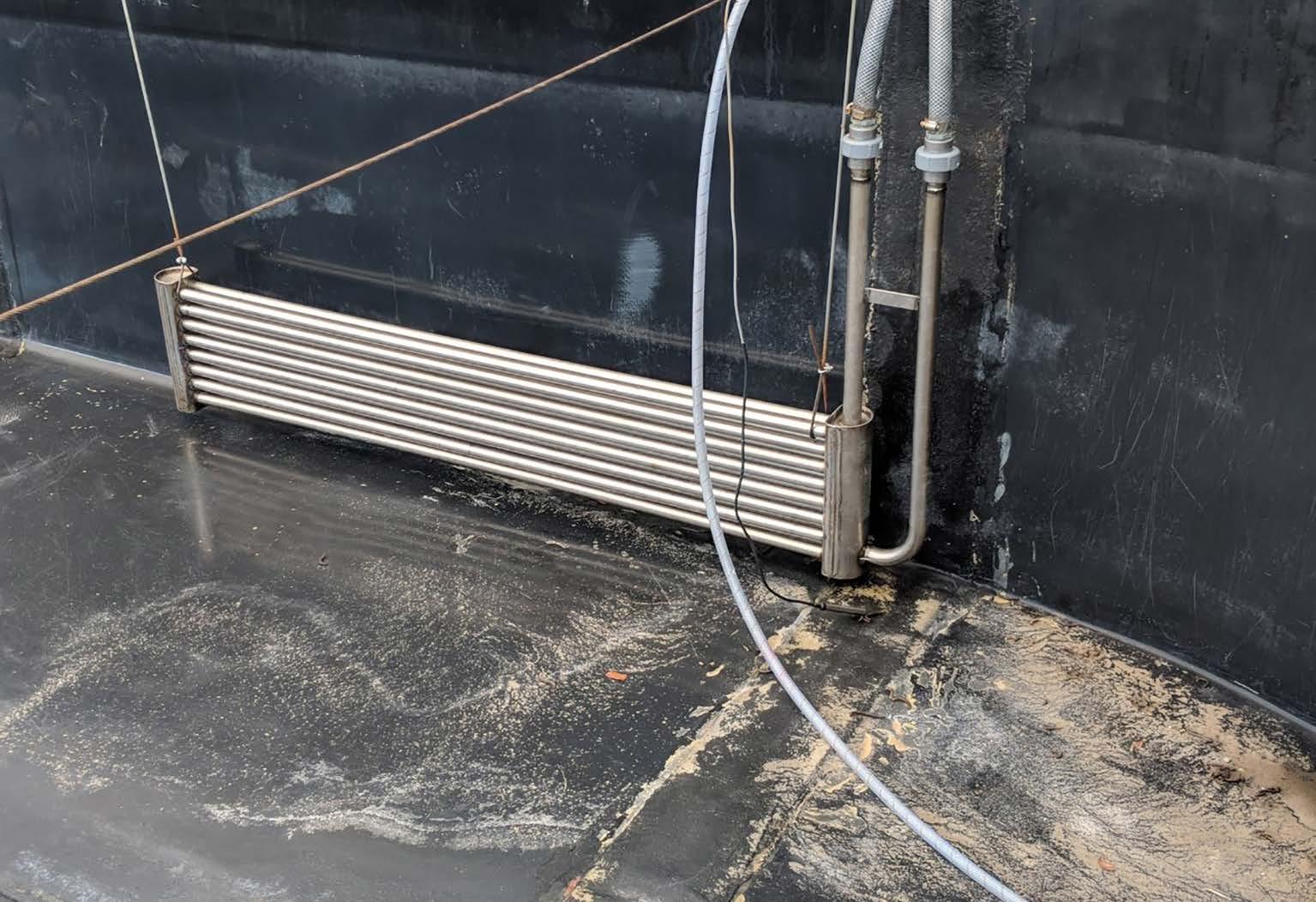
considered plug and play. Anything over 15 amps is supplied with a controller that will need to be wired in the field.
Gas and Electrical Inline Heaters Inline heaters come in a variety of sizes from the very small units which are slightly larger than the piping up to the larger units which can require significant space. Starting with the smaller heaters, these are comparable to the immersion heaters discussed
Titanium Immersion Coils.
above. The maximum available size in this style is 120KW.
Larger inline heaters are available in propane, natural gas and electric. These vary from simple spa heaters up to larger systems with onboard heat exchangers. There are a variety of options with this style of heater,
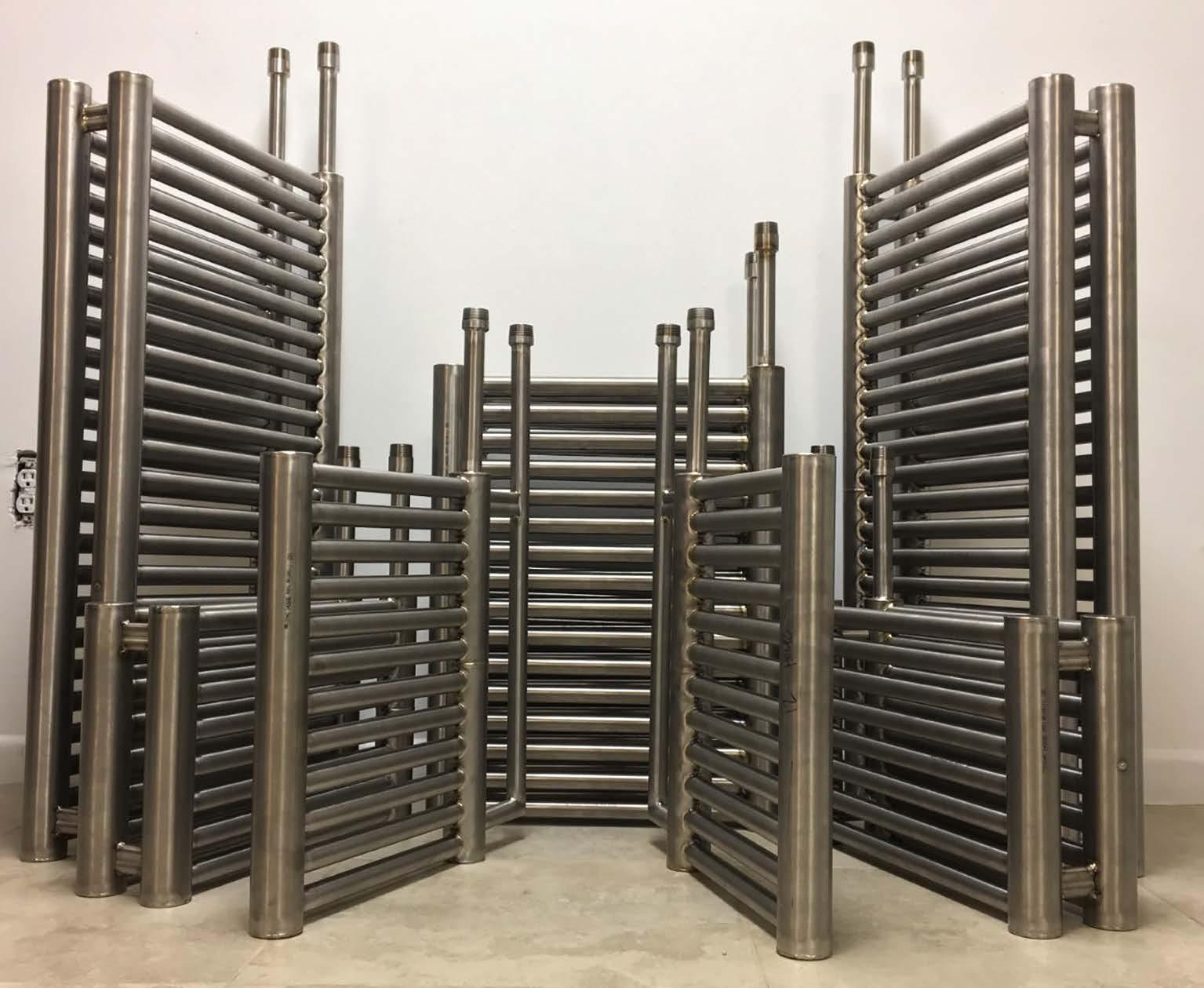
A couple ways to mitigate surface area heat loss is to control ambient air temps or tent the tanks to create a microclimate to limit evaporation.
but they max out at about 20 horsepower.
Boiler Loop For the more commercial systems, it is more effective to set up a hot water loop using a boiler and separate heat exchangers. The concept is similar to
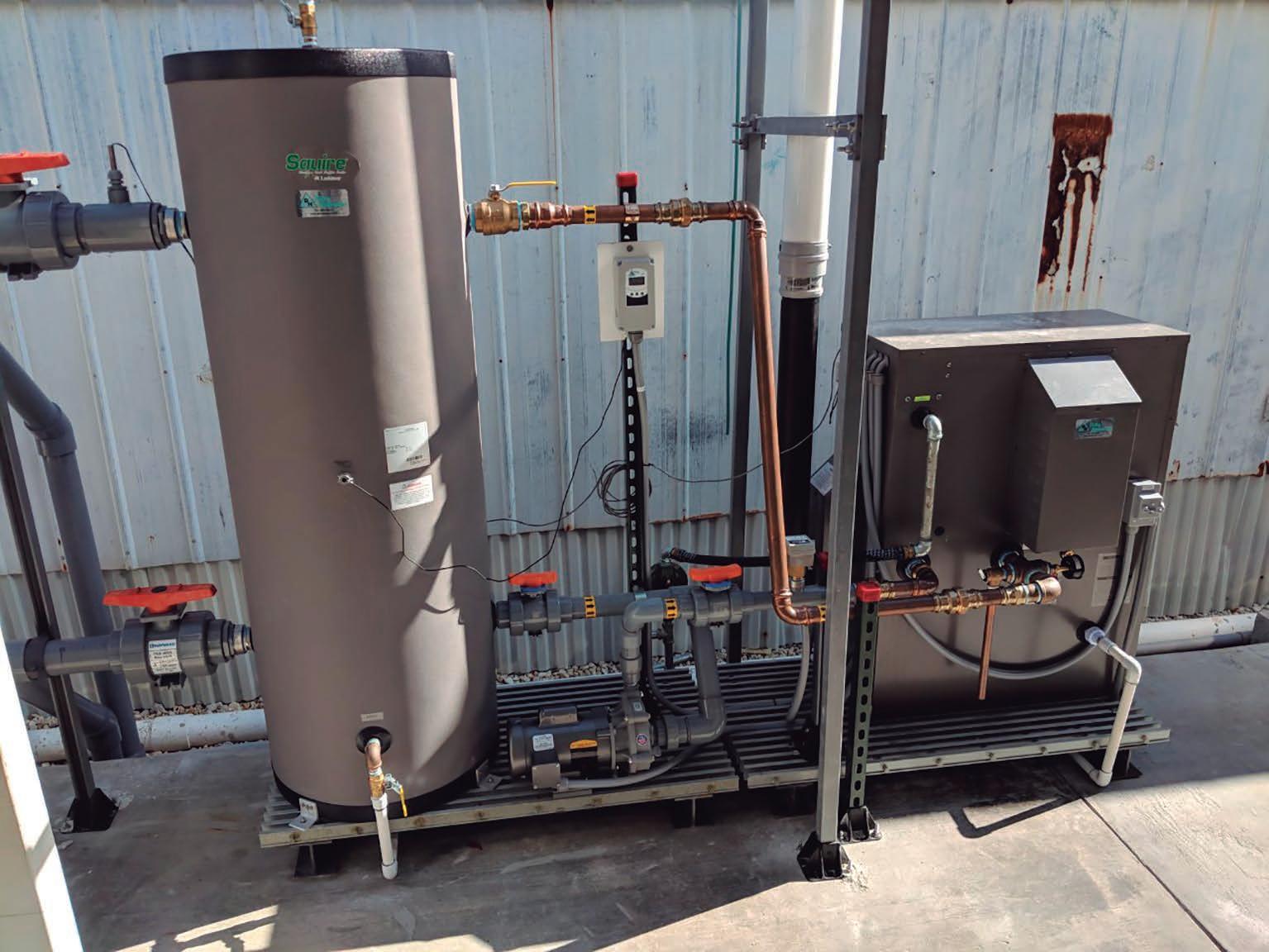
an in-line system, but it is split into separate components. They consist of a boiler, heat exchangers (immersion, shell-in-tube, or plate type), control valves/pumps and individual temperature controllers. The entire system is sized to accommodate the heating load for the entire facility or building and keeps the water in the boiler loop at 125F -180F depending on the heat transfer required and the piping system.
At the end of the day, the type and size of heater is really dependent on the application. I want to thank Delta Hydronics for their technical review of this article.
Amy Riedel Stone is President and Owner at Aquatic Equipment and Design, Inc. She was formerly a Manager at Pentair Aquatic Eco-Systems, and she studied Agriculture at Purdue University. She can be reached at amy@aquaticed.com