MARKET
MATERIAL HANDLING AND PRODUCTIONINTELLIGENCELINE
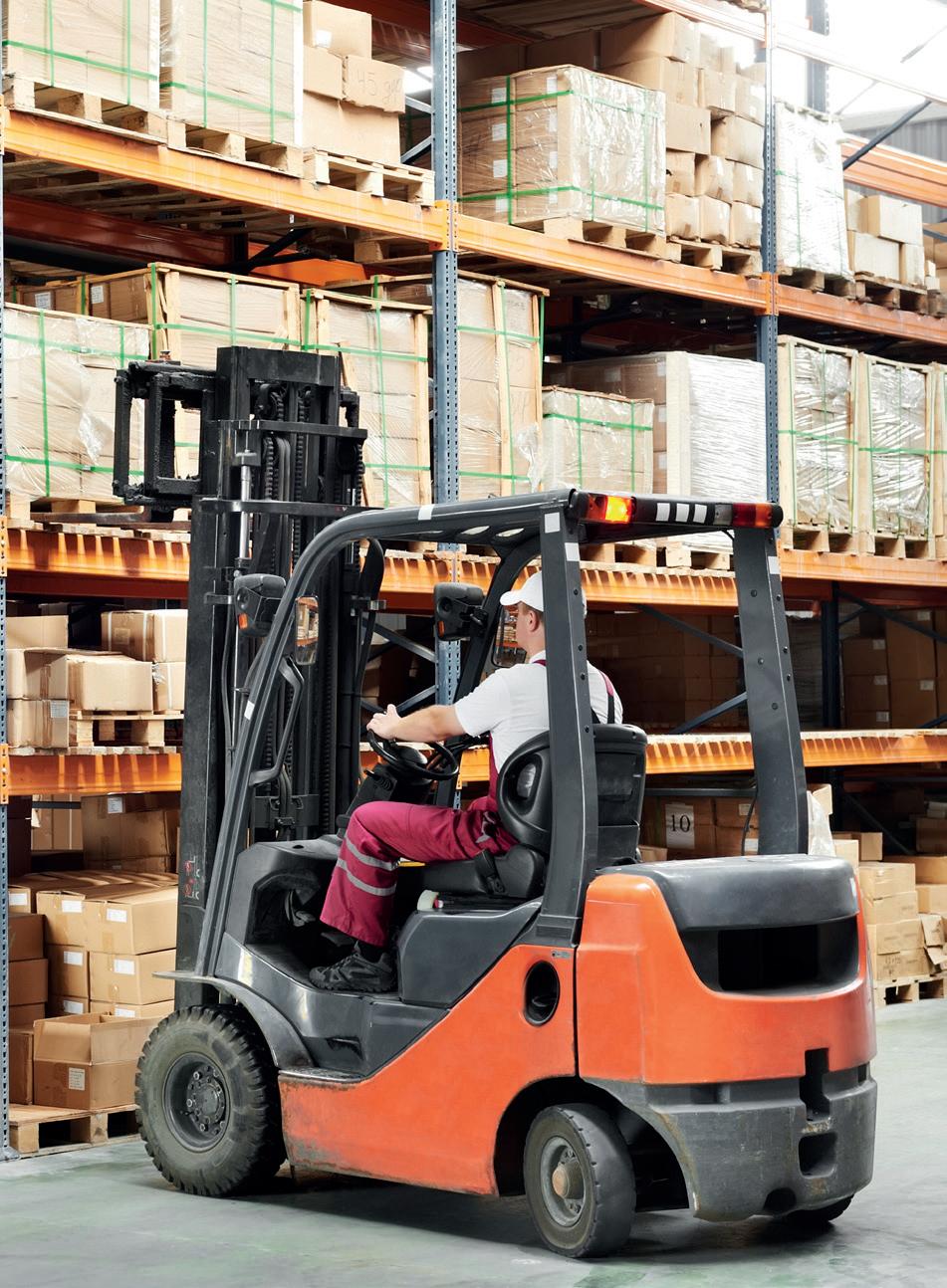
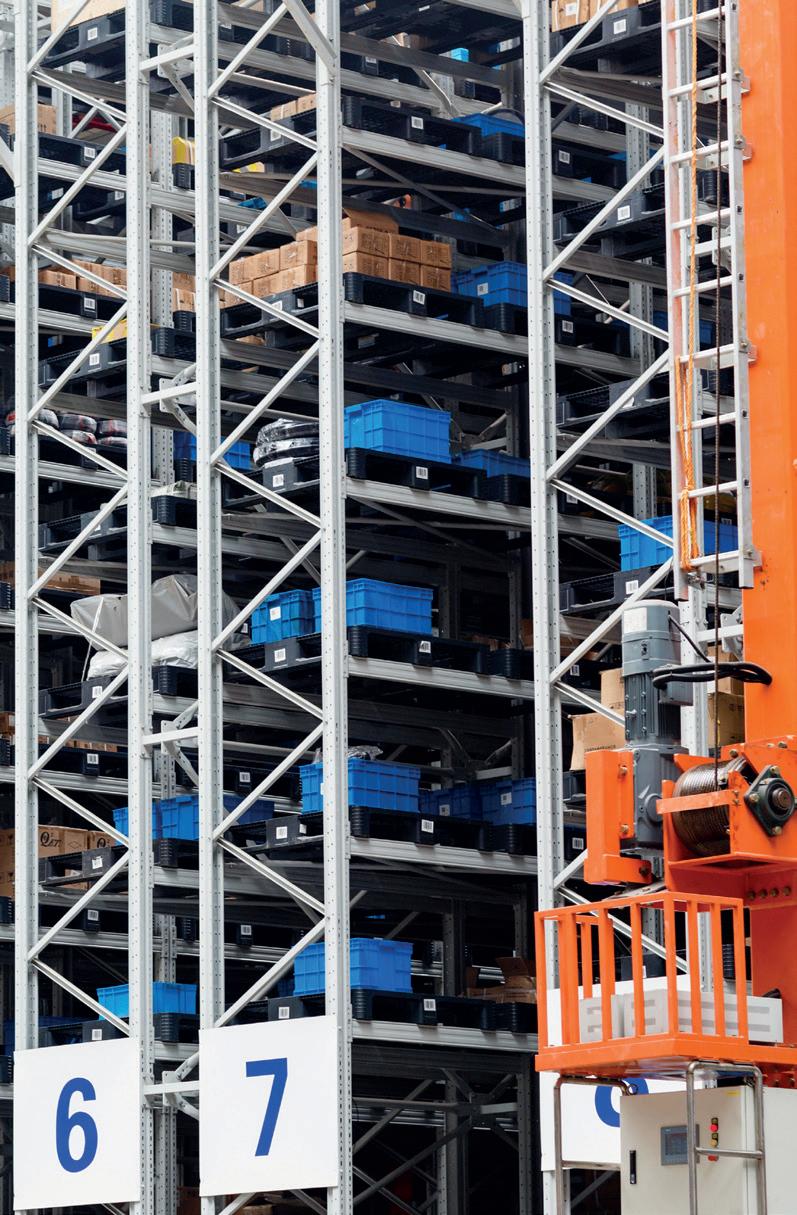
2. Production Line Intelligence Page 10—23
c. European sales data and evolution
b. Market size and coverage
As part of the development of tools and resources for members, this document is designed to add value to their commercial understanding of specific markets and production line processes. This document, on the Materials Handling industry, follows the success of the first report in 2016 on the Soft Drinks industry, the second in 2017 on Confectionery and most recently, the Automotive industry in 2018.
f.
This first section provides an introduction and overview to the material handling industry and gives key background information, market intelligence and major players within the industry. It has been organised as follows:
h. Major machine builders
This document has been divided into three parts:
g. Key producers in the materials handling industry
The purpose of this document is to provide distribution management and their sales forces with market and production line intelligence on the material handling industry, primarily in warehousing and fulfilment centres. This document explores trends, identifies products used in moving products from point to point, clarifies key challenges and considers the opportunities and how they can be capitalised.
a. Definition, segments within the industry and market share
d. Current and future market trends
This section illustrates several examples of material handling processes so as to provide an understanding of what is involved and where the opportunities lie. Key customer challenges, major product groups, typical maintenance and improvement projects are identified throughout the line, as well as highlighting potential areas of commercial opportunity for the distributor.
The opportunities within the material handling sector, both for MRO and OEM distribution are significant – an estimated minimum ‘scale of opportunity value’ (SOV) of 750 million€ has been estimated as available for distribution in the aftermarket. The final section proposes how the document could be used and provides open-ended questions that can be asked to prospective customers in order to reinforce the knowledge gained in parts one and two and to maximise the available opportunities.
Overview
3. Use of this Document Page 24—25
3
EPTDA’s mission is to strengthen its members in the industrial distribution channel to be successful, profitable and competitive in serving customers to the highest standards. The association takes great pride in its values which focus on being a premier community for qualified members through open dialogue and mutual respect; acting with integrity, honesty and fairness; and ensuring continuous growth and learning.
1. Industry Overview Page 4—9
e. Overview of challenges Key demographics
Purpose of this document
EPTDA continually strives to develop relevant tools for its members, helping them stay competitive in a constantly evolving marketplace and business environment.
EPTDA was founded as the European Power Transmission Distributors Association in 1998 in Marbella, Spain, on the initiative of a group of power transmission and motion control (PT/MC) industrialists who believed in bringing together PT/MC distributors and manufacturers on one unique platform. It has since become the largest organisation of PT/MC distributors and manufacturers in EMEA and is one of the most powerful and respected B2B executive platforms for the industry worldwide.
integrated within industries such as food and drink, automotive and pharmaceutical. However, the major growth is within the warehousing and stock management of goods for global companies such as e-commerce site Amazon, Allegro in Poland and Alibaba in Asia. As well as national players and logistics centres in food storage, major supermarkets and online retailers. It is in this area on which this document focuses – that is, on the handling of goods (post-production) in warehousing, distribution hubs, fulfilment centres and postal services.
Market size and coverage
In 2017 the global material handling equipment (MHE) market was worth over 112 billion€ and is expected to exceed 142 billion€ by 2022 with a CAGR of 5.5%. Driving this growth is the increase in production capabilities from rising demand for sophisticated automated systems, such as real-time inventory management, picking accuracy and safer operations. All of which enable manufacturers and warehouses to load and transfer at higher speeds, reduce labour costs and improve order fulfilment efficiency. 2
Storage equipment & AS/RSShelves,StackingRackssystemsframesbins&drawersMezzaninesUnitload guidedAutomatedvehiclesHand,platform&pallettrucksOrderpickersPalletjacksSideloadersWalkiestackers ReclaimersConveyorbeltsStackersElevators (vehiclesTransport&transfer) Robotics & AS/RS systems Bulk handlingmaterialequipment Product Application manufacturingmerchandiseE-commerceGeneralFoodretailFood&beverageDurable 3rd party logistics (3PL) Material handling AutomatedRoboticsSystemsretrievalConveyors Material handling equipment and application4 4
In 2015, Europe held the largest market share of the global material handling market, however China has since overtaken – now representing almost half the market (41%). Despite this, the European market still represents 34%, with the next largest market share at 19% by North America. 3
PART ONE
As a key driver of the material handling industry, it is of no surprise that the e-commerce sector generates almost 20% of the industry revenue but it is also heavily prominent in the automotive and electronic sectors for the storage and transportation of goods once they have left the production line as well as in the food industry especially in the growth of cold storage.
Material handling is the movement, protection, storage and control of materials and products throughout manufacturing, warehousing, distribution, consumption and disposal. This is normally within the confines of a single building or location, before the materials are then transported elsewhere. Further to this, material handling includes the protection, storage and control of those materials, products or services, using fluid or mechanical power and automated systems.1
Materialbusinesses.handlingis
Definition, segments within the industry and market share
Material Handling Industry Overview
Material handling is therefore an essential component and process for the movement of goods for many industries and service
AS/RS make up over a quarter of the automated materials equipment and are complex devices. They enable manufacturers to operate a seamless process of ordering and logistics management reducing human involvement and inevitably cutting expenses both in the short and long term.
ConveyorSystems
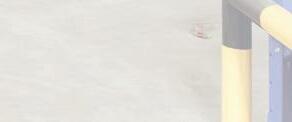
Conveyor systems
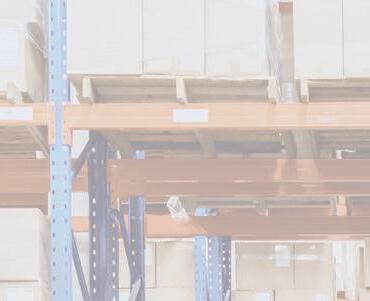
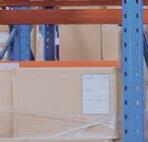

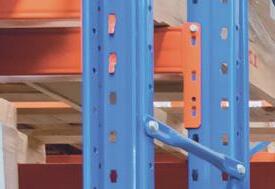
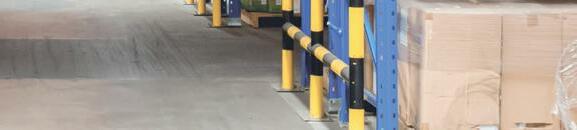
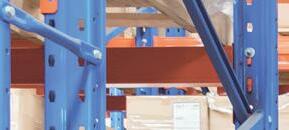

19% E-commerce Automotive Semiconductors&ElectronicsPharmaceutical Food Beverages&Aviation Chemical Other 16% 14% 13% 12% 12% 10% 4% 5
Global market share for material handling equipment in 2017, by region5
Robotic systems
AS/RS SystemsRobotic 27% 21% 9% 6%
Typically, the handling of smaller goods will see greater use of manpower over conveyor and robotic or automated systems. Despite this, adoption of automated material handling equipment (AMHE) is expected to be seen in 25% of all material handling processes in factories and warehouses by 2022.8

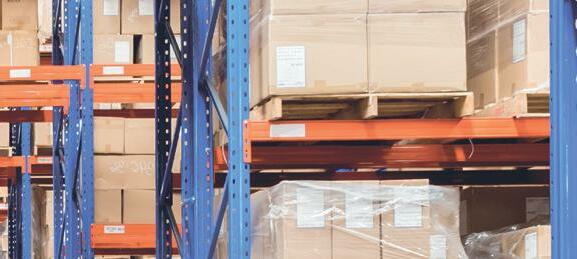
Global Automated Material Handling Equipment (AMHE) market share in 2016, by type6
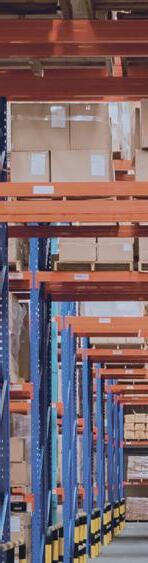

Conveying systems are the third most popular automated systems equipment and are used to move bulk material from one place to another. Available in many forms from pneumatic, vibrating and vertical they are used to support many industries. This sector is expected to dominate the global market over the next few years.
Automated storage and retrieval system (AS/RS)
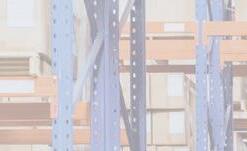
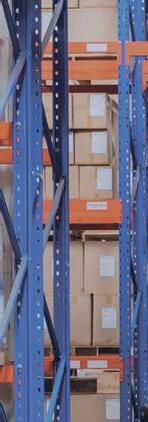
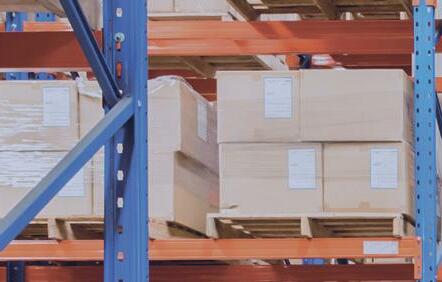
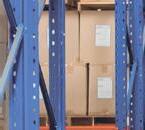
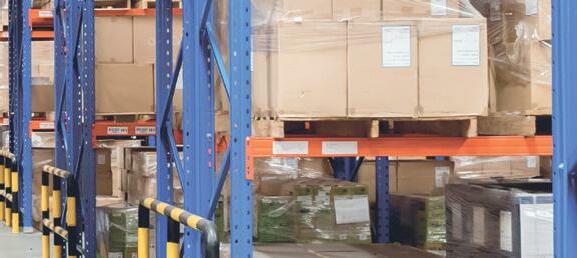
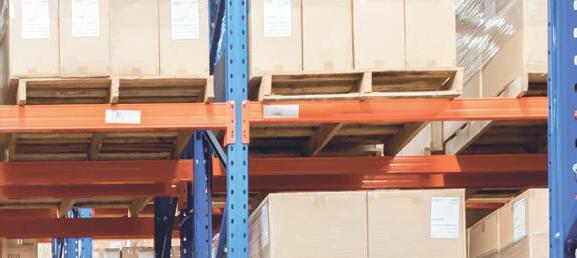
These systems are heavily used in packaging, automotive and manufacturing industries which can be explored further in their respective EPTDA Production Line Intelligence Reports.
Volkswagen Group Asia Europe North America 3% Central / AmericaSouth 3% Oceania 1% Africa 40% 34% 19% 37% Other AGV
Global material handling equipment revenue share in 2015, by end use7
Robotic systems make up over a third of the equipment and are used to continuously assemble, pick, pack and place products in an efficient and timely manner to reduce human error.
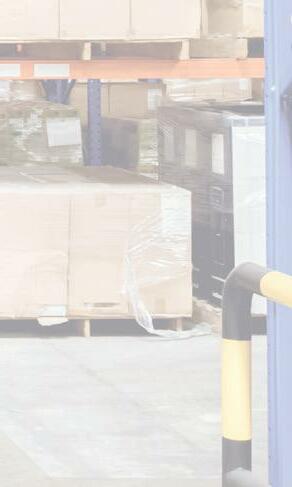
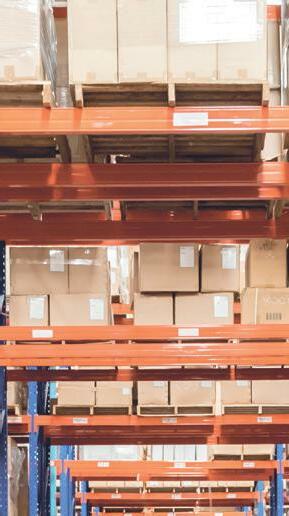
The European Logistics industry, which includes transportation as well as material handling, generates over 900 billion€ each year. Fuelled by Europe’s increasing urbanisation, GDP growth and demand for e-commerce to be located closer to customers,

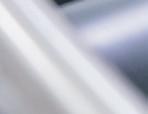

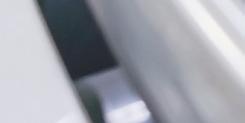
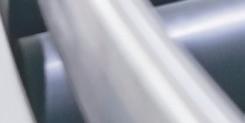
More recently, a second belt known as the ‘Golden Banana’ or ‘European Sunbelt’ – covering the coast between Valencia and Genoa – has seen the increasing development of logistical and materials handling centres.13
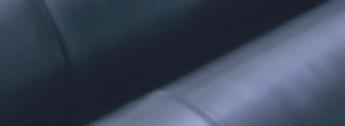
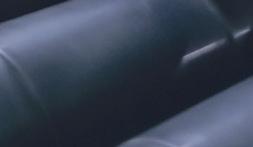
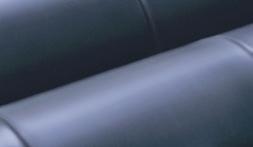
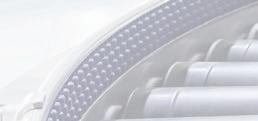
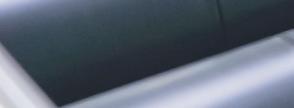
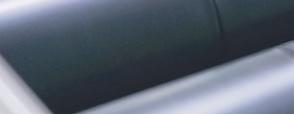
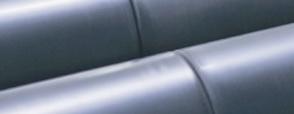
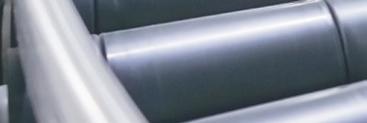

Companies strive to locate their warehouses, fulfilment and distribution hubs within the ‘Blue Banana’ zone so to be able to reach customers as quickly and as readily as possible.12
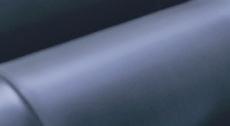
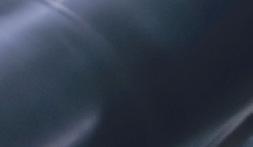
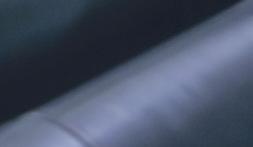
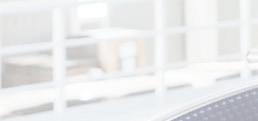
Cities with highest production value of transportation and storage tend to fall across the European area known as the ‘Blue Banana’ – featuring densely populated and wealthy cities.
Production value of transportation & storage in 2016, in million euros, by region9
it is currently one of the biggest industries within Europe.10 Of this, warehousing, terminal and contract logistics has a market share of just over 50%.11
Composition of material handling, lifting & storage equipment in Europe, in 201614 The Blue and Golden Banana arcs of Europe 78% Material handling & lifting equipment 14% Software automation& 8% Storage equipment& Country transportationofvalueProduction 20024001601208040 222.6 81.779.964.150.3 214.0 208.1 46.442.9 164.2 Germany NorwayPolandBelgiumSwitzerlandNetherlandsSpainItalyUnited KingdomFrance European sales data and evolution 6
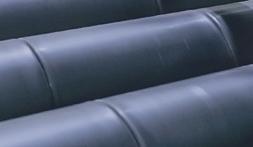
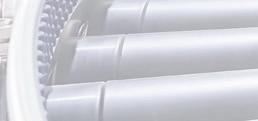
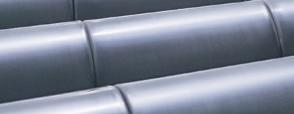
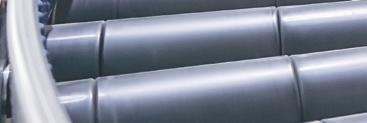
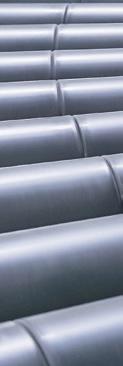
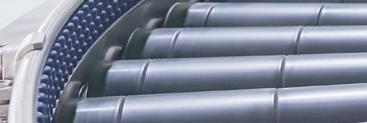
Plastic pallets are less likely to break or suffer misalignment than wooden pallets and therefore do not require as frequent replacements. As such, plastic pallets are particularly popular in industries such as dairy, pharmaceutical and beverages. 21 value of handling equipment
For example, with the increase in urbanisation, industries in power and mining have turned to material handling equipment and systems such as large conveyors, in order to respond to this growth.16 It is expected therefore that with the increase in urbanisation, so will the increase in demand for material handling solutions.
Key demographics
Current and future market trends
One way to improve speed is through the installation of robotics and automation (AS/RS). Industry 4.0 and the Internet of Things (IoT) applied to material handling will see smoother order picking and real-time tracking whilst making effi cient use of space for storage.
In addition, competition forces companies to fi nd ways of keeping production costs low and as sustainable as possible. Material handling equipment and systems offers a solution to this challenge by improving operational effi ciency and bettering the order-to-delivery process.
For example, fixed systems of interconnected conveyors which cross long distances, whilst also being able to sort dozens of packages every second. Additionally, articulated robotic arms are used to sort and pick out a variety of goods.19
Plastic pallets are identifi ed as offering greater benefi ts over traditional wooden pallets due to durability, safety and light weight for transportation. It is also estimated that the move from wooden to pallet could see overall costs of transporting goods or materials reduce by 35%.
material
With increasing demand for e-commerce and the digitalisation of the retail sector, whereby advances in technology, logistics and payments are paired with the rise of internet, mobile access and consumer demand for convenience, there is increasing need for speed and accessibility to products and services. Material handling systems are one of the ways in which manufacturers and courier services are able to respond to this demand.
in the EU in 2016, in billion euros, by sector 15 Sector materialsofvalueProduction 20015105 19.6 14.7 13.2 14.2
Speed is also a crucial factor for the development of new technologies in material handling. In UPS’s fl agship facility centre in Cologne, it takes, on average, 15 minutes for one item to move from entry to fi nal loading point.
Sensor technology is increasingly being used throughout the material handling process as it becomes more and more affordable. It can be used for detailed shipment tracking to provide consumers transparency in real time (from sorting, picking and packing, through to delivery). 20
7
Material handling technology is constantly being advanced with rising synchronisation between different systems expected to result in the development of machine-to-machine co-ordination and communication.17 This will help warehouses and fulfi lment centres to optimise workfl ows and to reduce downtime of machinery or equipment through the detection of Researchmalfunctions.anddevelopment has also seen material handling equipment that is smaller, yet more effi cient, so that technology is less expensive to install and easier to operate, whilst also offering a solution to maximising utilisation of available space – an increasing premium across Europe.18
Cranes & lifting storage&ContinuoushandlingequipmentIndustrialtrucks
are also seeing age groups being more willing to buy ‘big ticket’ items online now than fi ve years ago, for example cars.14 This could see material handling equipment and systems becoming more and more integral to industries that have previously been less impacted by the demands of the digital and e-commerce sectors.
Packing
In response to this premium cost, warehouses are bringing in engineering expertise, of a variety of sizes, to modernise, extend, develop and create new conveying systems that make the most of available space.
Whilst Generation X (born between 1966 – 1981) have greater disposable income than Millennials (born between 1981 –1996), Millennials were found to make more online purchases than other age groups, with 45% admitting that they prefer to purchase online due to the ability to compare products and for Increasingly,convenience.retailers
Production
The rising awareness of high performing automated handling equipment and its benefits is enticing companies to replace the use of traditional human techniques. Optimising their systems not only increases productivity but enables the users to control these automated systems remotely, offering features such as precise operational capability, real-time inventory control, order picking accuracy and safer operations.
Although smaller in scale, this has led to the increase in warehousing facilities being set up throughout Europe in order to speedily meet customer demand.
As a result, warehouses are now found in a variety of shapes and sizes from the ultra-large to smaller centres where space is at a high premium.
As the world speeds up, so do the demands of the customer. This paired with increased online sales climbing every quarter is putting pressure on the industry to ship the goods faster, as demonstrated by Amazon’s ‘Prime’ service whereby goods are delivered the very next day.
As equipment becomes increasingly sophisticated and more automated, warehouses and fulfilment centres become even more reliant on continuous support and maintenance. This is both an opportunity and a challenge for maintenance-oriented service companies, to be able to prove they have the capability to meet expectations and help with improving efficiency.
Storage
In contrast, the ultra-large warehouses, typically national players such as Zalando in Mönchengladbach, Germany, Morrisons in Sittingbourne, England, or Amazon in Dunfermline, Scotland, will operate on a much wider scale. 25, 26 Instead they are less heavily reliant on automated processes, with greater emphasis on a the human workforce.
As government bodies and industries begin to implement stricter regulations on recycling, such as the withdrawal of single-use plastic, the material handling player will need to respond accordingly.
Recycling
Due to a scarcity of prime warehouses in Europe, it has led to a series of bidding wars where space is priced at a premium.23 Online retailers have responded to this by adding smaller warehouses (up to 2,500 sqm) to their logistics networks, enabling them to provide quicker delivery services.
As this demand increases for property, so do the prices for renting or purchasing land to house these distribution or fulfilment facilities. Therefore, manufactures look to find other areas within the process for cost-cutting, or turn to innovative material handling equipment so to meet greater demand with tighter deadlines. 24
These smaller warehouses, in order to keep footprint as small as possible, will either construct their material handling process in a vertical fashion, which in turn requires greater mechanical power transmission. Or, they will rely on automated processes to maximise the available space, where manual input is kept at a minimum.
Overview of challenges
In addition, as the end-user of the materials or goods being handled, become increasingly aware of the environmental impact of their purchases, the process of material handling becomes another area in which manufactures must consider their environmental strategy.27
European leaders in logistics and e-commerce28, 29 Top ten logistics companies in terms of revenue Top ten retailers in terms of revenue Value Rank (as of 2017) Company Primary GeographyBusiness Value Rank (as of 2017) Company Primary GeorgraphyBusiness 1 Deutsche Post DHL Germany 1 Schwarze Gruppe Germany 2 Deutsche Bahn AG Germany 2 Aldi Germany 3 Keuhne + Nagel Intl. AG Switzerland 3 Carrefour France 4 SNCF Group SA France 4 Tesco United Kingdom 5 La Poste France 5 Edeka Germany 6 UPS Europe NV Belgium 6 Rewe Germany 7 The Royal Mail Holdings United Kingdom 7 Amazon Unites States 8 DSV A/S Denmark 8 E.Leclerc France 9 Dachser SE Germany 9 Les Mousquetaires France 10 XPO Logistics Inc. United States 10 Auchan France 8
• Witron Logistik + Informatik GmbH | www.witron.de | Parkstein, Germany
SSI Schaefer | www.ssi-schaefer.com
7 TGW Logistics Group Austria
• Flexlink AB | www.flexlink.com | Gothenburg, Sweden
2 SSI Schaefer Germany
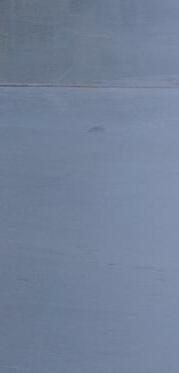
Daifuku Company Ltd. | https://www.daifuku.com/
Daifuku specialises in conveying, storage, sorting, picking and controls, specifically for the material handling industry. In 2017, Daifuku reported sales of over 400 billion yen. 31
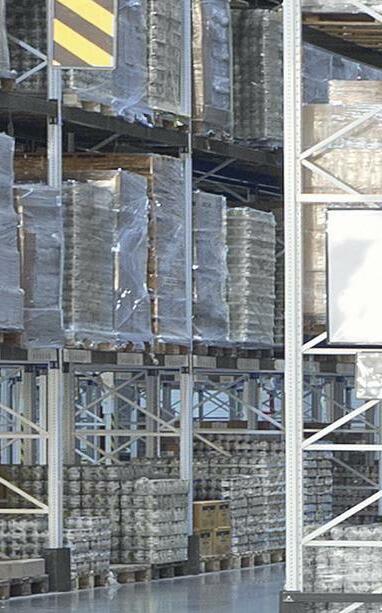
Providers of logistic process automation at airports and for postal services, Vanderlande Industries move 10.1 million pieces of luggage per day on its baggage handling systems. 34
• Egemin Automation | www.dematic.com | Zwijndrecht, Belgium
Primary GeographyBusiness
10 Swisslog AG Switzerland

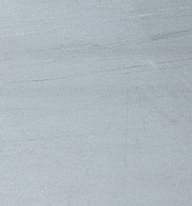
Value Rank (as of 2017) Company
• Kardex AG | www.kardex.com | Zurich, Switzerland
Murata Machinery Ltd | www.muratec.net
4 Vanderlande Industries BV The Netherlands
9 Fives Group France
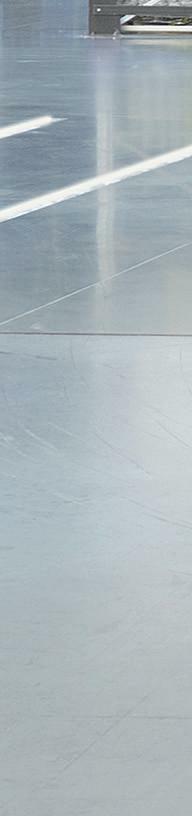
Honeywell | www.honeywellaidc.com
8 Buemer Group Germany

• Elettric 80 | www.elettric80.com | Viano, Italy
5 Murata Machinery Ltd. Japan

Dematic build automated system solutions for warehouses, distribution centres and production facilities. 33
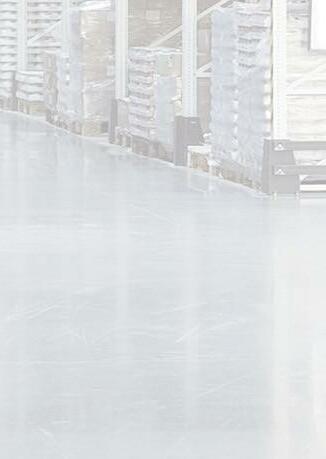
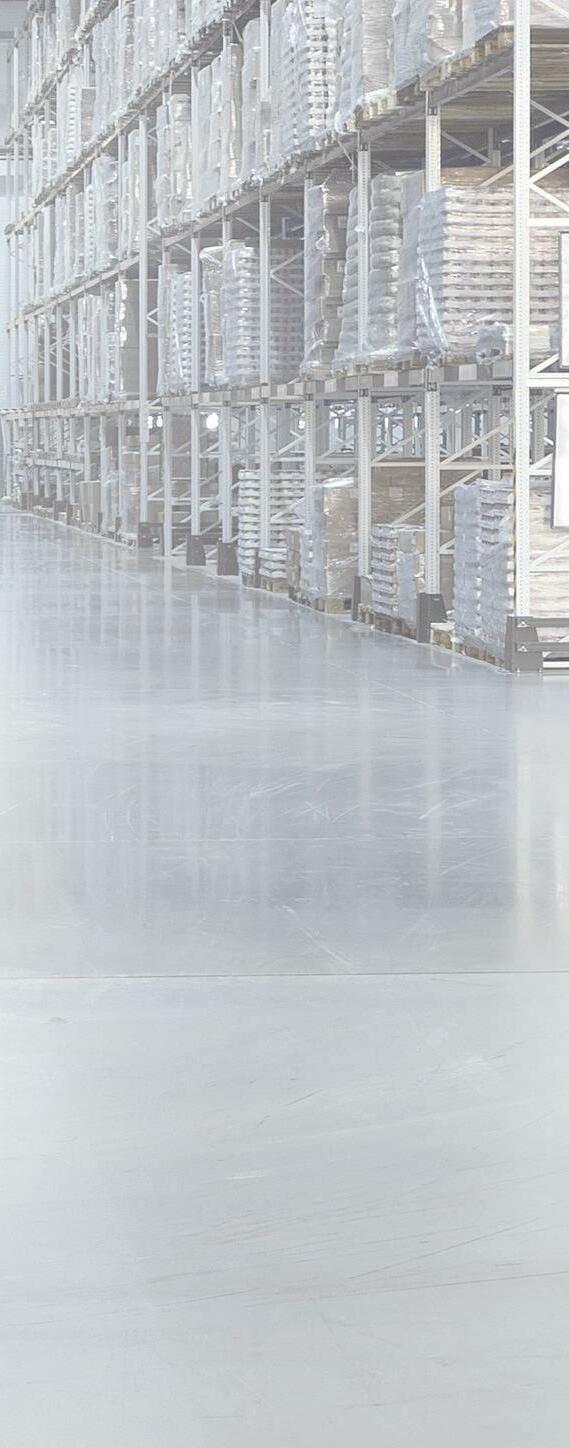
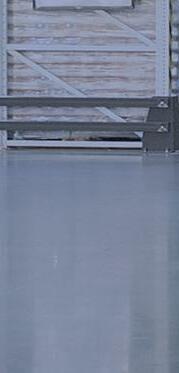
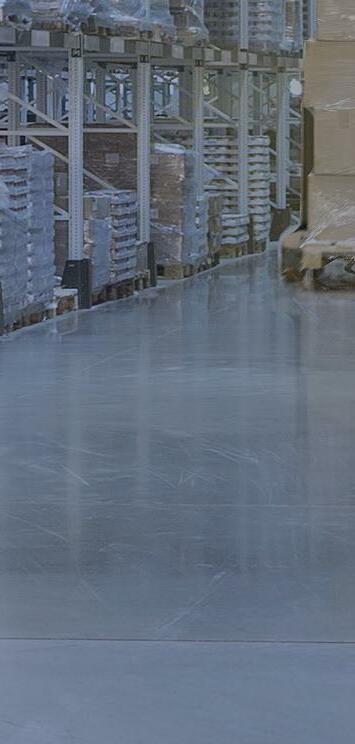
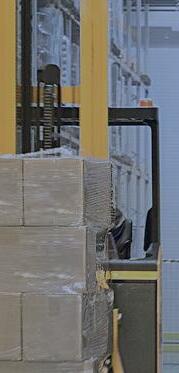



Key machine & system builders30
Operating across six continents, SSI Schaefer primarly develop storage, conveyor and logistics systems, as well as waste management technology. 32
TGW Logistics Group | www.tgw-group.com
Buemer Group | www.beumergroup.com
Fives Group supplies multi-sector machines and key process equipment for industrial materials and intralogistics. 39


Swisslog AG | www.www.swisslog.com
Dematic | www.dematic.com
1 Daifuku Co. Ltd. Japan
• Stö cklin Logistik AG | www.stoecklin.com | Aesch, Switzerland
TGW Logistics develop supply chain technologies, products and turkey solutions for material handling, intralogistics and warehouse automation. 37
A global company and a member of robotics supplier KUKA, that designs automated solutions for logistics and healthcare industries.40
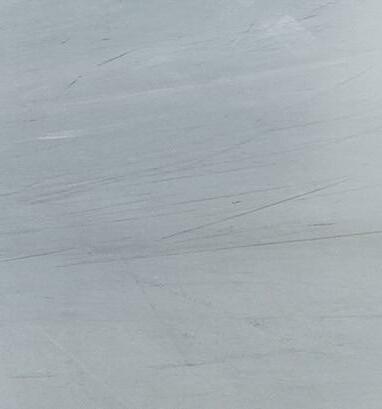
Also known as Muratec, Murata Machinery operate in logistics and automation, machine tools and sheet metal machinery. 35
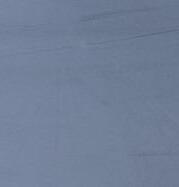
Other significant players in the industry
Buemer create design a variety of systems, including airport baggage handling, postal and warehousing. They also operate in the food and beverage sector. 38
• Knapp | www.knapp.com | Hart bei Graz, Austria
Large warehouses will often use multiple system builders. The top ten global materials handling equipment systems in terms of revenue are ranked as such:

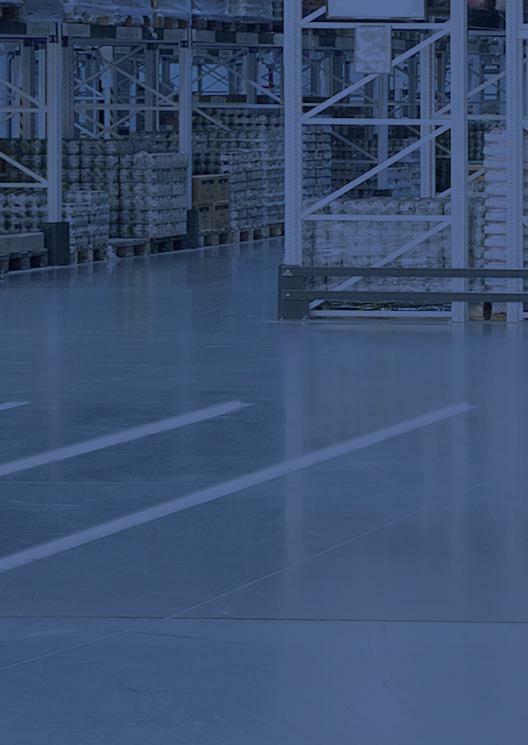

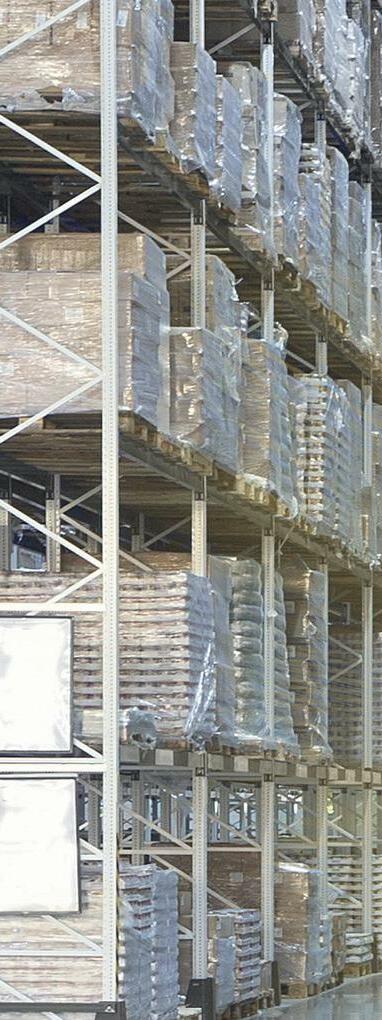

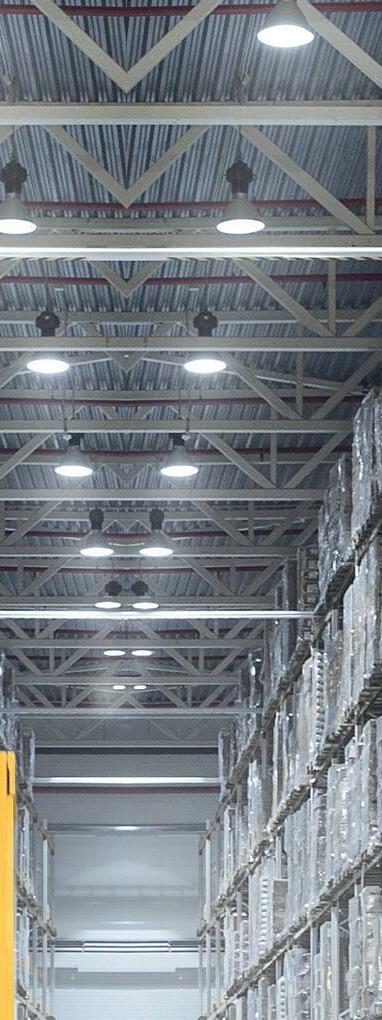
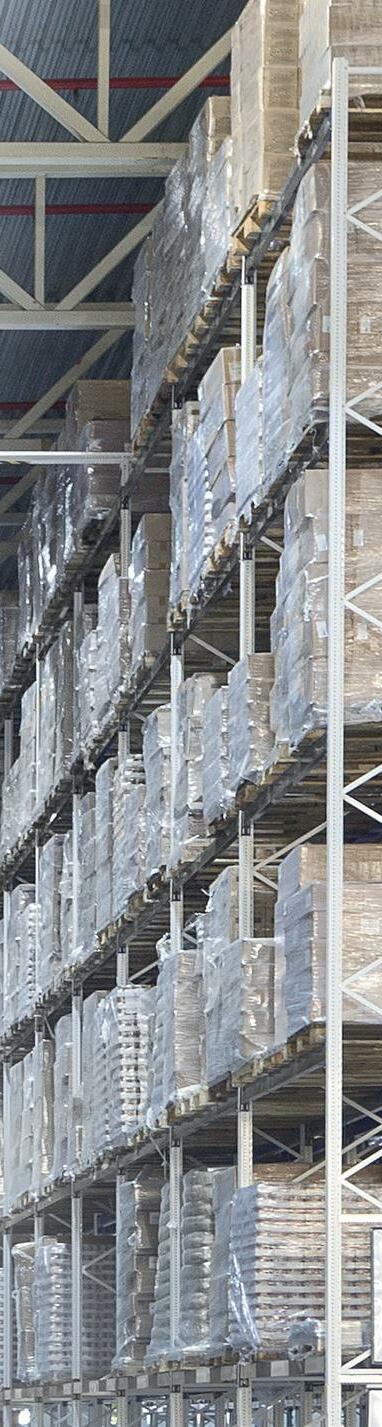
3 Dematic United States
Vanderlande Industries BV | www.vanderlande.com
6 Honeywell United States
Fives Group | www.fi vesgroup.com
9
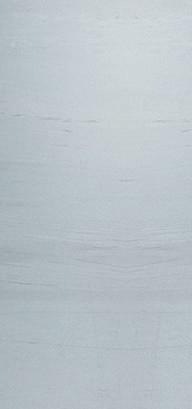
A multinational group that produce a variety of commercial and consumer products, including solutions for transportation and logistics and systems for distribution and postal facilities. 36
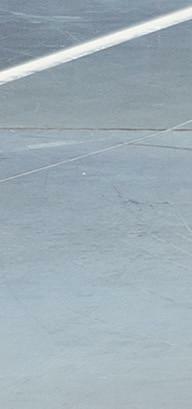
This section also highlights the key customer challenges specific to material handling. It describes the key product categories used in the process and typical projects in maintenance, repair and overhaul that are often undertaken in such a plant. Key sales opportunities are identified in relation to products and maintenance projects that are supported by distributors with real technical expertise.
PART TWO
The following are key challenges that are often found within material handling. Supporting the schematic, additional key challenges relative to specific stages of the production process are identified.
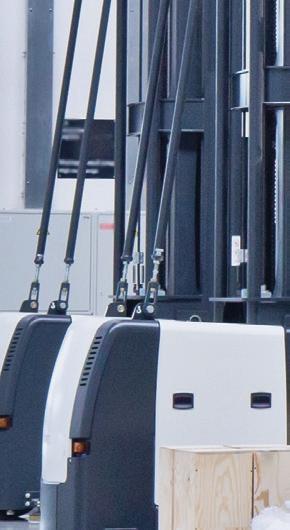
Cleanliness and health and safety
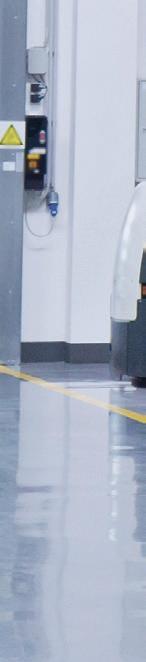

• Electronic intelligence in machines requires that workers are educated and trained about the safety of operating material handling equipment and systems
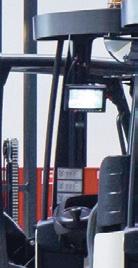
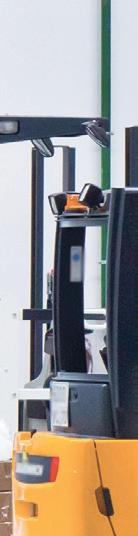
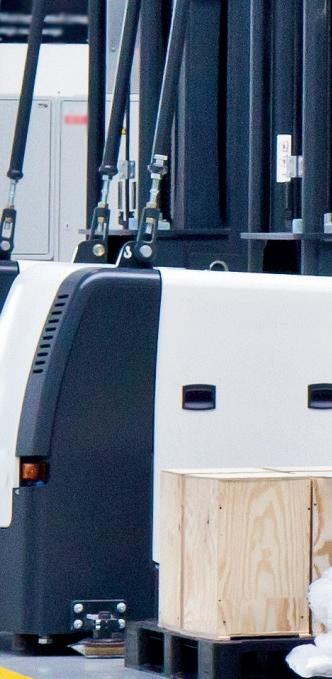
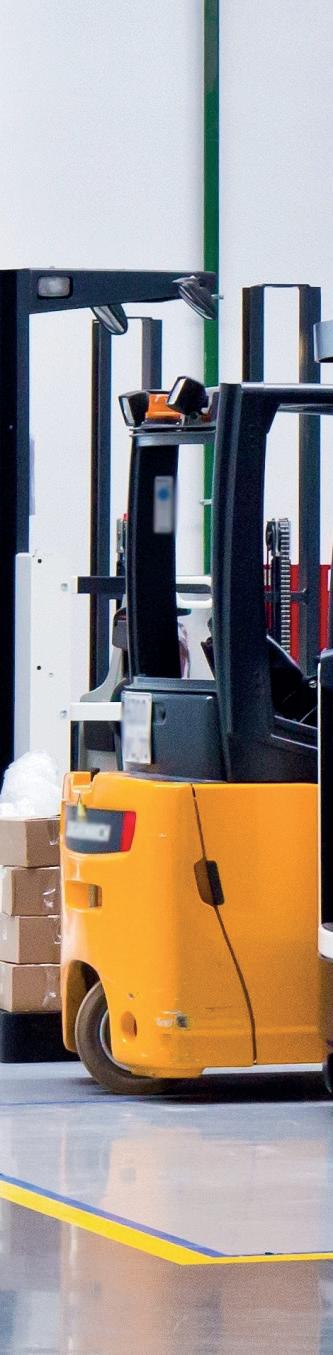
Material handling process - Market Intelligence
• Ionisers are vital to remove the significant risks of static electricity frequently present in various points of the process
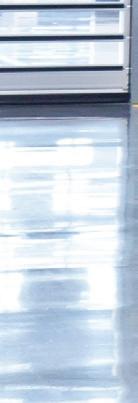
Cold stores
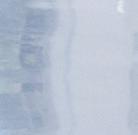
Introduction
This schematic describes the typical process used for material handling in a warehouse, detailing the six key stages: receiving, putting away, storage, manual sorting & picking area or automatic sorting & packing areas, and dispatch.
• Security system controls for electrical and pneumatic parts e.g. Safety of Machinery Standard ISO13849-1, due to be reviewed in 2020
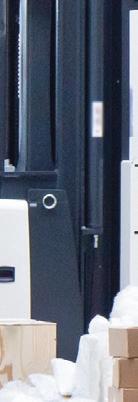
• Depending on the type of material being handled, parts must be able to withstand the varying environments e.g. cold storage or goods that must be kept sterile
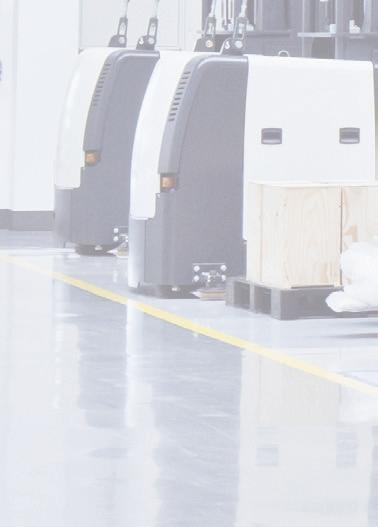
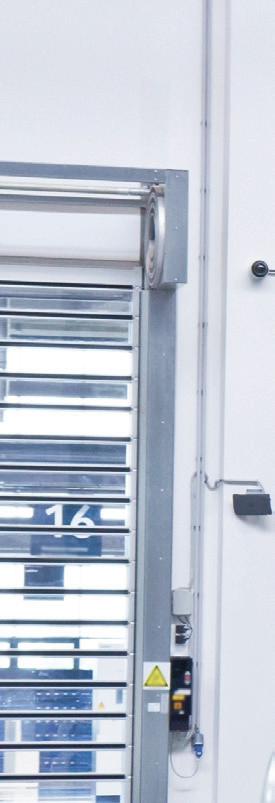
10
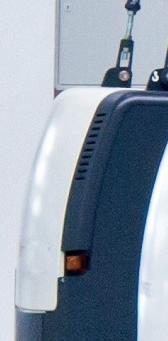
Key challenges and themes
• Due to the harsh environments, parts need to be selflubricating, or even adapted from lubricated to hardened plastic (PU) which can cope better with the cold and not require lubrication at all
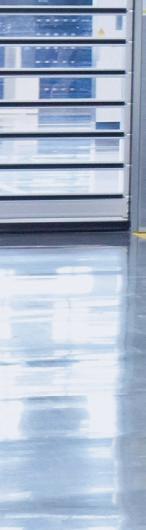
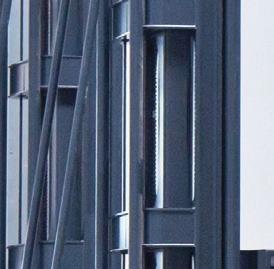
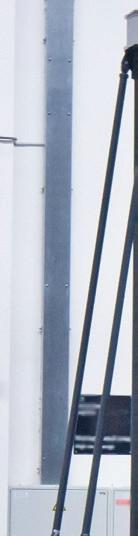
This process, whilst being typical, does not represent all material handling. This is because actual plant processes may vary according to the type of material handling and plant scale and facility. For example, warehouse operations are considerably different to those of air baggage handling. However, the key stages described here will be common to most types of facilities and there will be similarities that can be seen across all segments of the material handling industry.
• Equipment throughout the process has to be automised due to extreme conditions. For example, in some cases equipment must be able to function in up to minus 40 degrees celsius

• Depending on the type of goods or materials being handled, there will be different storage and system requirements
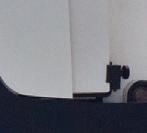
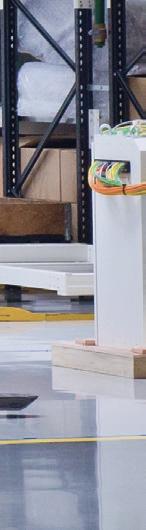
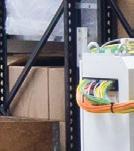
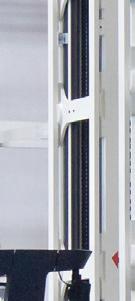
After market warranty
Industry 4.0
• When system builders supply systems to retailers or logistics providers they often include exclusive warranty in the initial sytem purchase within the first two to three years
• With the use of sensors, real-time data and the Internet of Things (IoT), reliable predictions can be made about the status of material handling equipment and systems, so that repairs happen before a critical incident happens, thus reducing downtime and associated costs
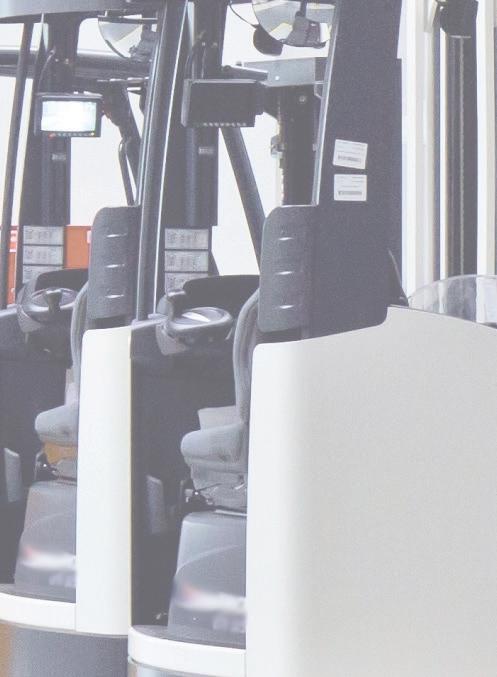
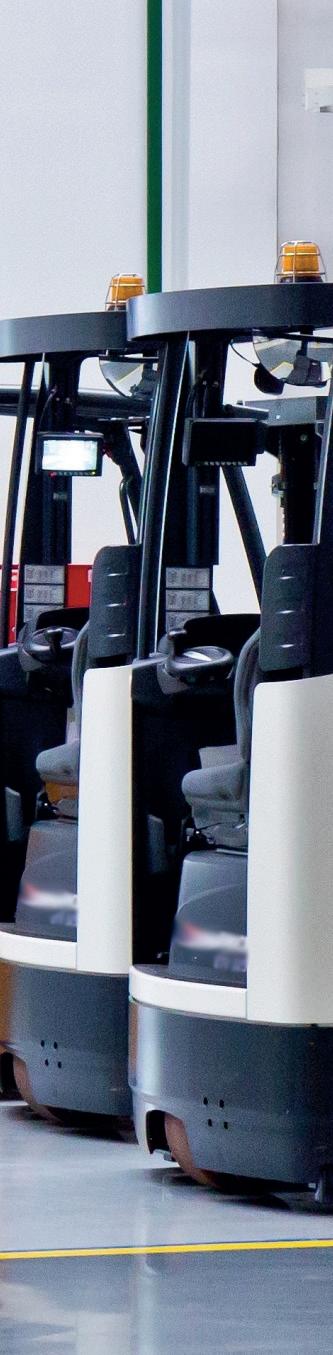
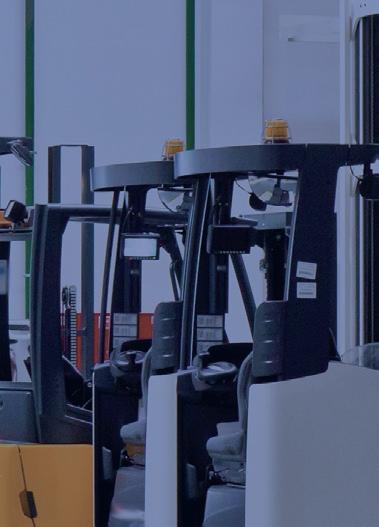
11
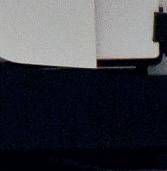

• The ability to transport goods and materials at speed is vital to the operation of most facilities, especially online retail centres
• Industry 4.0 is the practise of interconnected devices communicating with one another, providing human interfaces with real-time data
Speed and accuracy
• This enables manufacturers to move away from reactive maintenance i.e. repairing equipment once broken to preventative maintenance i.e. maintaining, repairing or replacing on a schedule and also to predictive maintenance i.e. using algorithms and monitoring systems to predict when operations require maintenance
Types of material handling
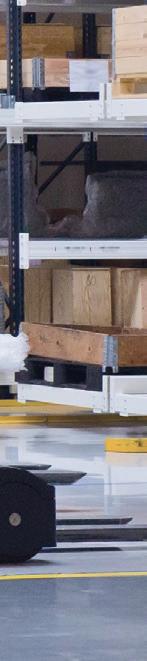
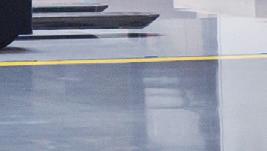
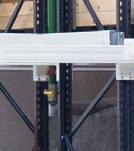
• For example, replacing forklift trucks with internal conveyor systems so to improve speed and accuracy of pallet storage per day
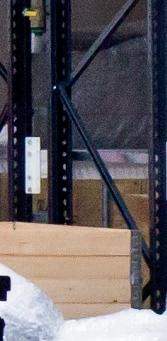
• Industry 4.0 will see more efficient use of materials, selfmonitoring and network connectivity, and thus less downtime of machinery
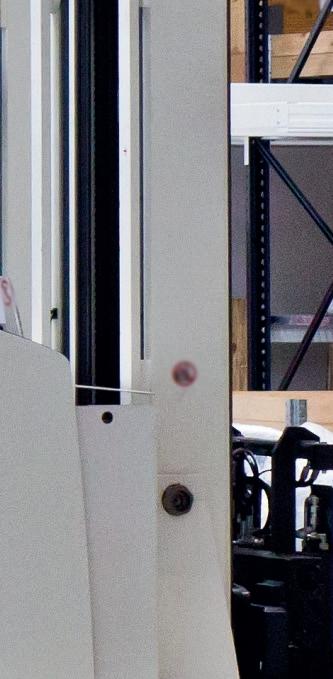
• Once storage capacity reaches 18,000 europallets (without conveying systems) processes should move to automisation and see up to 520 pallets moved per hour
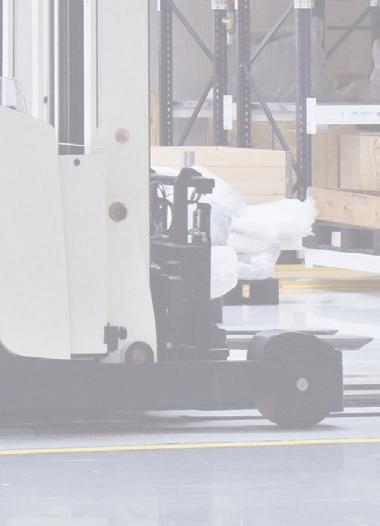
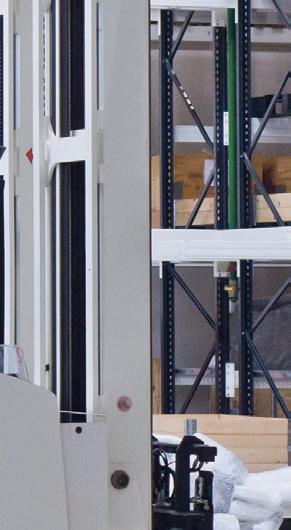

• Goods that require a 48-hour, 24-hour or 4-hour turnaround will have varying needs e.g. food or building supplies may require a faster turnaround from receipt to storage to dispatch, than that of sporting equipment or clothes
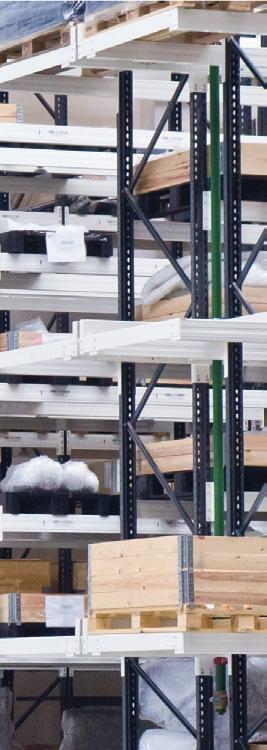
Fireguardsafety
Low-levelenvironments.storageis
RFID scanners
Receiving Putting away
RFIDscanners Dispatch
Material Handling ProcessProcess
1. Receiving Goods or materials are received by the warehouse from delivery trucks at loading and unloading bays sometimes with an integrated truck bed chain-driven conveyor. Goods are scanned by an RFID reader either manually or at automated points along the conveyor system.
High-level
High-levelrequired.storage,
typically operated by manual putting away and retrieval. The goods are picked up from conveyor systems by workers in the warehouse and registered with handheld RFID
2. Putting away After being unloaded from delivery bays, the goods are transported along conveyor systems to their allocated storage space. This can either be automated through conveyor and warehouse management systems or scanned using handheld devices before being transported manually by hand or by industrial trucks such as forklifts. This is to ensure the journey of goods are tracked throughout the warehouse process before being allocated to correct and/or vacant storage spaces.
Explaining the process
such as multi-tier racking uses a mixture of manual and automated retrieval systems (ASRS) to place goods and materials into storage. Stacker cranes for palletized loads typically operate up to heights of 30-40m. This is ideal for large warehouses requiring optimum use of available space, as well as catering to a variety of environments e.g. cold, clean or other harsh
12
3. Storage The materials or goods are transported according to warehouse capabilities and requirements for storage until later
Low-level storage
Storage
Automated storage
5. Automatic sorting & packing area Larger warehouses, or those with automatic systems in place, will transport goods from storage to the dispatch area. These processes are very similar to the receiving and putting away stages, but in reverse. As with manual sorting, automated systems are used for packaging and labelling.
scanners before being placed in low-level storage solutions. These are easily accessible in person or with the aid of forklift trucks or robotic pickers.
&Sortingareapicking
Automaticsorting&packingareaPalletiser
Process
4. Manual sorting & picking area Having been retrieved from storage, the materials are manually sorted and prepared for dispatch. This may include packaging and labelling goods for onward delivery.
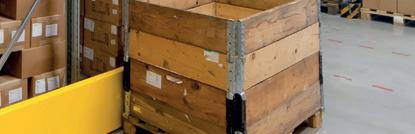

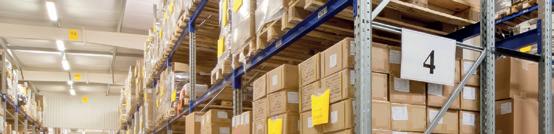
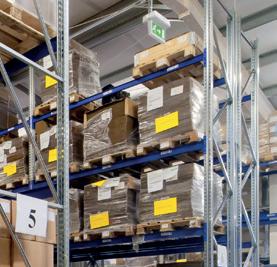

6. Dispatch Similarly to receiving, materials or goods are moved from conveyor systems to trucks. This can be done either by manual transportation of goods e.g. forklift trucks, or through integrated truck bed conveyors.
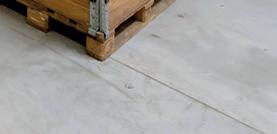
High-level storage
Automated storage provides warehouse with compact storage solutions, from mobile shelving fitted with a tracking system that identifies where goods are stored and how to access them when required. These systems are so compact that manual retrieval is often not possible, with serious impact when goods are unable to be retrieved due to machine malfunction or downtime.
13
• Conveyor systems
• Drives
Explaining the opportunities and projects
• Linear guides and drives
• Special timing belts
• Truck bed conveyor - unloading of goods from delivery trucks is increasingly being conducted by chain-driven conveyors embedded in the floor of the truck. This removes the need for forklift or manual input and increased automisation possibilities
• Sensors
• Conveyor power belts
• High replacement of telescopic boom conveyors due to surface wear on belt. SOV: 60k€ for repair and 1.5m€ for replacement
• Multi-ribbed belts
Receiving Key product groups
• Timing belts for power transmission are changed every 3 4 years. SOV: 70k€ per line
• Gear motors rightangled, parallel
14
• Maintenance of belt-tracking units. SOV: 5k€ per line, with an annual saving of 15k€
• Speed of the material handling process is often influenced by the weight of the materials or goods being handled. For example, heavy-weighted goods and materials, especially when being moved vertically, will be transported utilising chain-driven conveyor. In contrast, lighter goods in horizontal positions will typically move along a belt-driven conveyor
RFID scannersTruck bed conveyor
• Replacement cost of refurbishment of conveyor power belts. SOV: 5 - 30k€ every 3 4 years
Key criticial projects within the receiving and putting away areas have been highlighted along the schematic to make it easy to identify which areas of the process have most opportunity. Other typical product groups to look for in the process include:
• Timing belts
• Invertors
Material Handling ProcessReceiving
flat-top conveyorconveyors,belts
• Roller chain
• Synchronous asynchronousandmotors
Receiving
• Palletising deepgroove ball bearings, bearing units
Receiving Critical projects
• In food and beverage application maintenance of robotic palletiser and actuator/valve replacement. SOV: 10k€
• Roller conveyor without drive
Putting away
Putting away – Key product groups
• Aluminium profiles
• Air preparation FRL
Putting away Critical projects
• Frequency converters
• Frame steel/galvanized, painted or powder-coated
• Conveyor belts have high MRO requirements. SOV: up to 25€ per square metre, with additional costs for welding
• Belt-tracking units
• Advantage of modular link belts are that they are very flexible, and easy to exchange, reducing minimal downtime
• Chain in automation of pallets storage has a 3 5 year life span, with guides and sprockets replaced at the same time. SOV: approximately 50€ per metre of chain
**Please
15
• Hinge bands – plast ic, steel or stainless stell
• Sensors – light and scanners
• PU/PVC Conveyor Belts depends on requirements e.g. oil-resistant, FDV-compliant, temperature
• Drives motor directly placed on shaft
• Automisation capacity of up to 520 storage pallets per hour
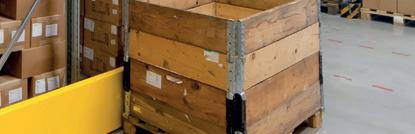

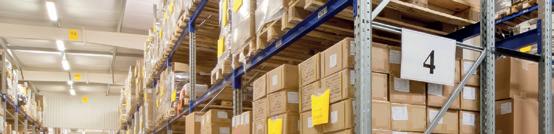
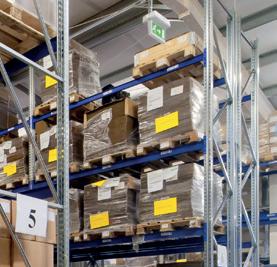

• Rollers - plastic, aluminium or steel
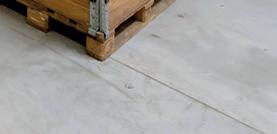
• Standard roller chain
• Centring units
• Stopper cylinders
• Modular linked belt – used in most new systems for longer conveyor lines with curves
• Where water and cleaning agents are used to a large extent, especialy in food/beverage industries, roller bearings and motors are replaced. SOV: up to 25k€ per annum note that all figures represent the Scale of Opportunity value (SOV).
Putting away Fireguardsafety
• Laterally-driven roller conveyor
• Labelling & printing pneumatic cyclinders and valves
Material Handling Process
• Modular systems for pallet-storage based on EU pallets
Storage – Key bearing product groups
• Pillow blocks
16
• Auto-lubrication plain bearings [PTFE cover]
• Rollers
Key criticial projects within the storage and sorting & picking areas have been highlighted along the schematic to make it easy to identify which areas of the process have most opportunity.
Please note that storage facilities may include a combination of automatic or manual equipment. Typically, automatic storage will be implemented for large scale sites and warehouses.
• Belts and timing belts
• Bearing units
Storage
• Couplings metal bellow, backlash free, clamping elements, chain, gear, elastic [for system closure], precision u-joints
• ready]systemsCondition-monitoring[Industry4.0
Storage
Low-level storage
• Standard conveyors
Storage – Key product groups
• High-resolution sensor bearings [Industry 4.0 ready]
Explaining the opportunities and projects
• Bearings [ see key bearing product groups table]
• Cam followers
High-level storage
• High-level/vertical storage is in increasing usage with special chain/belt applications e.g. linear motion guides and open-end timing belts
Manual picking area
• Some storage facilities have roller workshops onsite due to regular maintenance requirements
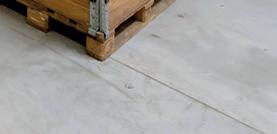
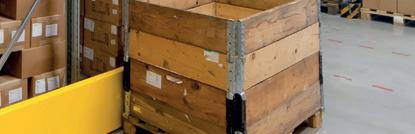

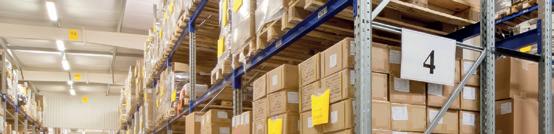
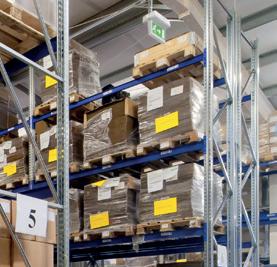

• Replacement of standard chain with self-lubricating roller chain for use in cold storage. There may be up to 2.5km of chain and associated sprockets c. 85k€
17
• Replacement of deep-groove ball bearings, gear motors/reductors and guide profiles. SOV: 400k€
• Use of open-end timing belts and with long-length steel core for moving stacker cranes to the picking rack or pallet location. SOV: 25 40k€
Storage Critical projects
• Replacement of linear motion belts. SOV: between 75 140k€
• Single-point lubrication with centralised system up to 80€ per point
**Please note that all figures represent the Scale of Opportunity value (SOV).
Automated storage
Sorting & picking Sorting & picking area
• Aluminium profiles
• Bearing units
• Pillow blocks
• Frame – steel/galvanized, painted or powder-coated
Automatic sorting & packing
• Actuators - pneumatic and electric
• Pressure-relief valves
• Top-line ball bearing systems
Sorting, packing & dispatch
PalletiserAutomatic
• PU/PVC Conveyor Belts depends on requirements e.g. oil-resistant, FDV-compliant, temperature
• Synchonrous asynchronousandmotors
• Rollers plastic, aluminium or steel
• Spherical roller bearings
• Sensors, light and pneumatic scanners
• Air preparation FRL
• Fieldbus operating systems
• Modular linked belt used in most new systems for longer conveyor lines incorporating curves
Key criticial projects within the automatic sorting, packing area and dispatch have been highlighted along the schematic to make it easy to identify which areas of the process have most opportunity.
• Grippers
• Safety products
Sorting, packing & dispatch Key product groups
• Visioning systems
• Vacuum cups and ejectors
• Standard chain and toothed chain
• Control valves
– Key product groups
• Roller conveyor without drive
• Centering units
• Stopper cylinders
Explaining the opportunities and projects
• Auto-lubrication [PTFE cover]
• Roller rollerO-rings,conveyorslinkbelts,drives,pulleys
• Drives motor directly placed on shaft
18
• Roller chain
• Linear guides
Key bearing product groups
• Strut ball bearings
• Hinge bands plastic, steel or stainless steel
• Belt-tracking units
• Laterally-driven roller conveyor
Key pneumatics product groups
sorting & packing area
• Deep-groove ball bearings
• Invertors
• Cam followers
• Frequency converters
Material Handling Process
• Static control systems i.e. ionisers
• Gear motors - rightangled, parallel
• Advantage of modular link belts are that they are very flexible, and easy to exchange, reducing minimal downtime
• Major overhaul projects for belts, v-belts, elasticated belts. SOV: 500k€
**Please note that all figures represent the Scale of Opportunity value (SOV).
• Chain in automisation of pallets storage has a 3 5 year life span, with guides and sprockets replaced at the same time. SOV: 50 75€ per metre of chain
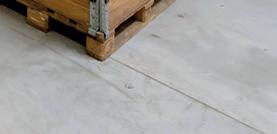
• Elasticated profile belts for gapping, induction and merging. SOV: 600k€
• Maintenance of roller chain. SOV: 2k€
• Timing belts for power transmission are changed every 3 4 years. SOV: 70k€ per line
Dispatch RFID scanners Dispatch
• Automisation capacity from 520 storage pallets per hour
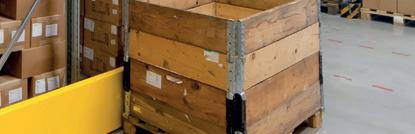

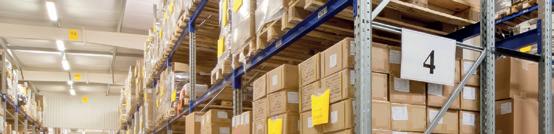
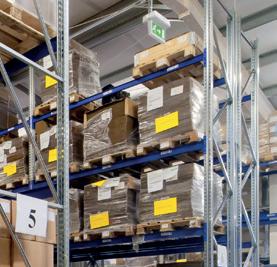

• Where water and cleaning agents are used to a large extent, especialy in food/beverage industries, bearings and motors are replaced. SOV: up to 25k€ per annum
• Replacement cost of refurbishment of conveyor power belts. SOV: 5 - 30k€ every 3 4 years
• Annual replacement of chain for roller conveyors. SOV: 50k€
• Replacement of round belts, O-ring belts and extruded kevlar core belts with integrated guides in linear sorters. SOV: up to 350k€
Sorting, dispatch & packing Critical projects
19
• Maintenance of PVC conveyor and elasticated thin belts for circular sorters. SOV: between 300 - 400k€
• Conveyor belts have high MRO requirements. SOV: between 25 300€ per square metre, with additional costs for welding
Sorting, dispatch & packing area Critical projects
Material handling process – ‘Putting it all together’ Material Handling - 'Putting it all together' Process RFIDscanners Dispatch Automaticsorting&packingareaPalletiser RFID scanners Fireguardsafety &Sortingareapicking StorageReceiving Putting away High-level storage Low-level storage Automated storage The approximate value of aftermarket sales in the material handling industry750m€ 20
• Using automatic lubrication systems for cost reduction can result in cost savings of up to 30%
Product: SOV:
• Align with suppliers to provide training to support reduction of cost of ownership. SOV: 5 10k€ per session
Material handling process – Case studies Key issues

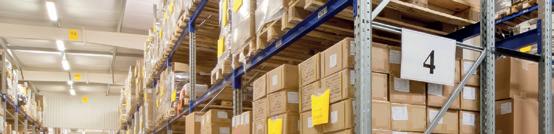
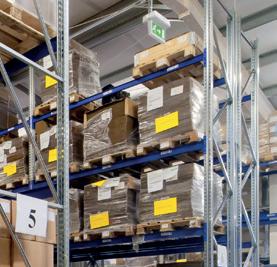

• Support rollers
• Gear boxes for food storage facilities
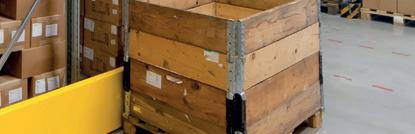
• Timing belts
• Standard conveyor chain for glass storage and packaging
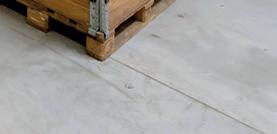
86010k€70k€15k€ 35% 30% 20% 5% 5% 5% Belts Rollers bearings& Pneumatics Drive Chain Couplings Pneumatics Belts Rollers bearings& Couplings Chain Drive 25% 25% 20% 20% 5% 5% 25% 15% 5% 5% 25% 25% Rollers bearings&BeltsChainPneumaticsCouplingsDrive - motors & gearboxes Proportion of replacement products in the process line Low-level E-commerceFast-movingHorizontal driven High-level AutomatedWeightedCold-store General Low-level High-level 21
Annual replacement per customer
End of product case studies – annual replacement per customer
Product group:
• Condition monitoring is used to monitor and keep track, in real-time, the status of stages along the process and identify parts that may need maintenance or repair (Industry 4.0)
SOV:
• V-belts
2 6k€ 4 20k€ 5 25k€ 6 15k€
• Standard conveyor chain for bottle transportation postproduction
• Roller chains
Opportunities to add value
Low-level storage High-level storage
and storage
Baggage Handling
and postal services, which contain similar elements from the warehousing schematic, but will differ in order, scale and extent of automation.

Whilst warehousing is a predominant sector within material handling, there are other segments and industries that material handling plays a signifi cant role in. The following schematics showcase the processes within baggage handling
Other applications of material handling
Materials Handling Production Line Schematic - Postal Services DispatchLargesortingparcelandReceivingsorting
Postal Services

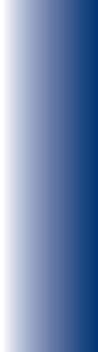

Material Handling Process transit
BaggageclaiminspectionSecurityIn
22
Turntables, lift tables and 4-way turntables are examples of transfer units using mounted conveyor modules that can change the direction of pallets by 90 0 and at speeds of up to 250 unit loads per hour.
Electric monorail
23
Key elements of conveyor systems
Automated dispensing or collection of empty pallets to and from a conveyor system.
Control devices
The below diagrams illustrate the six most common types of conveyor systems and their applications.
Chain conveyor
Pallet destacker/stacker
Similar to the roller conveyor, accumulating roller conveyors transport pallets along the conveyor in a longitudinal direction, whereby each pallet has an individual drive and control logic for precision speed control.
Accumulating roller conveyor
Transfers horizontal loads with chain, roller conveyor or telescopic forks for lighter loads.
Transfer units turntables
Whilst most conveyor systems are traditionally fl oor-based, overhead hangers can be used to maximise fl oor space, such as creating room for additional storage space and greater movement throughout the warehouse or facility for workers.
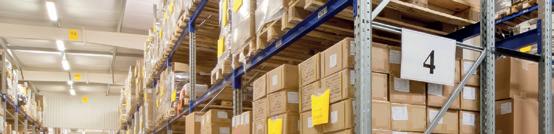
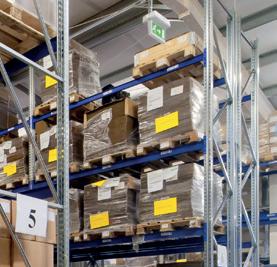

Transfer carriage with lifting device
Roller conveyor
Transports pallets up to 1.5kg along the conveyor in a longitudinal direction.
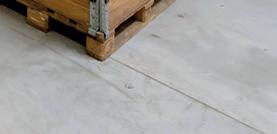
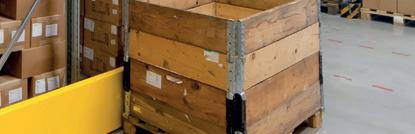

Control devices such as light or barrier sensors and mechanical devices are used to automatically determine the load capability of a particular section of conveyor and detect when a pallet passes along.
Conveyor systems are featured heavily throughout the material handling process with various capabilities depending on the conditions and requirements of the warehouse, site or facility.
Transports pallets up to 1.5kg along the conveyor in a transverse direction.
• Who are you going to see?
A manufacturing plant that has to store its postproduction goods in warehousing?
A warehousing facility that stores post-porduction goods ready for dispatch to the end user?
1. Preparing (before any visit takes place) – this provides questions to think about and address before attending the company’s site. This further breaks down into two sections being:
• What is your initial summary as to the main challenges they face in relation to purchasing the types of products you can supply?
BreadthPresentationExploratoryofservice
• What kind of questions will you ask (in relation specifically to who will be seen)?
• How old is the facility?
b. The people to be seen and which department
• Do they have inhouse maintenance engineers?
24
• How many people do they employ?
PART THREE
• What is your plan for follow ups to this meeting (further meeting/proposal/meeting with other people)?
The 'Material Handler'
Preparing – before the visit
3. The follow up – questions to ask or to reflect on, at the end of the meeting or afterwards
• What kind of support material do you need to take with you?
• What are the fall-back objectives if the primary objectives is unachievable?
• What is your proposed agenda?
2. The meeting – questions to ask during the meeting to understand the needs, requirements and potential sales opportunities in the prospective customer
• What do you already know about:
The stages of the material handling process it has (loading and unloading bays, putting away, storage, picking, packing and/or dispatch)?
• Who decides on purchasing?
• What are you visiting?
Do the system suppliers provide after market warranty service?
The people to meet
• Does this company have other facilities in your region/ territory?
The size and throughput?
a. Detail of the company itself
• What do you know about them already? (hint: search LinkedIn)
Using this document to develop business
• What is their role or speciality (facility maintenance/repair/mechatronics/purchasing)?manager/
• What are your primary objectives for the meeting – what do you want to achieve?
There are three parts that deal with:
For many of these questions you may already know the answers. Others might be used on a regular basis when you visit customers and prospects in other industry sectors. It is meant as a resource to act as a prompt and reminder allowing your business to fully capitalise on this market intelligence and production information.
The following provides the reader of this document, either General Management or Sales Team, with some template questions to help to generate revenue from this Production Line Intelligence overview and so develop business in the material handling industry.
General
Its scale in terms of capacity, pallet load, speed, output etc.?
• Who in your business do you need to share this information with?
What are they caused by?
DispatchPicking/packingStoragePuttingReceivingaway
Are you using partners – suppliers or distributors – to assist you in this process?
• Where is the process most prone to failure or maintenance problems?
• What is your biggest current problem with your parts suppliers?Howdo you like your supplier partners to assist?
• What other types of follow up will you undertake and why?
• How much of the process is reliant on manual input or automation?Doyouexpect this to change in the near future?
• What are the processes used from receipt to dispatch?
• What are the next steps? Can we come back with a proposal to help you with some of this?
The most utilised products
• How will you ensure that these follow ups are completed?
• How will you complete these?
• Where are your rollers repaired or do you have your own rollers workshop?
• What sort of regular maintenance does the plant undergo?
Are existing partners – suppliers or distributors –assisting?
• What are the next steps you need to take and when?
• What are your main issues in relation to maintenance?
What are your main issues in relation to maintenance?
• How are you going to use this information?
Suppliers
• What kind of support do you look for from your distributor in relation to planned maintenance?
(If not already known, any of the preparation questions above can be asked during the meeting to establish warehouse or site type, size, capacity, age, type, as noted).
• Do you have existing projects carried out in relation to maintenance or energy management etc?
• What are the key maintenance/industrial supplies objectives for the facility?
The actual meeting 'material handling facility'
• What type of storage facilities do you have and maintain (high-level, low-level, automatic, manual)?
The facility
The follow up
25
Maintenance, planning and issues
• What is the estimated annual spend on that maintenance?
• What are the ‘bottlenecks’ in the process that affect speed or reliability?
• What are your main concerns in relation to type of production parts that you need to maintain and improve the line (e.g. bearings, mechanical power transmission, pneumatics, etc.)?
What have been the success stories? How can these be replicated?
Are there on-going projects to deal with this?
• What parts do you particularly utilise most on an annual basis?What are the issues/challenges you have with getting those parts?
• What do you value most in relation to a supplier like us?
• What sort of plant or facility is this (end of production, food storage, online fulfilment centre, major warehouse)
• What were the main points you learned from the visit?
• How are you going to store this information?
achievable from various
Sources: 1. FEM European Materials Handling Federation, 'The European Materials Handling Industry 2010' 2. GM Insights, 'Material Handling Equipment Market' 3. Statista, 'Global Market for Material Handling Equipment by Region' 4. GM Insights, 'Material Handling Equipment Market' 5. Statista, 'Global Market for Material Handling Equipment by Region' 6. Business Wire, 'Global Automated Material Handling Equipment Market Forecast' 7. Grand View Research, 'Material Handling Equipment Market' 8. Market Watch, 'Automated Material Handling Equipment in Europe: Increase in Automation of Material Handling to Drive Growth' 9. Savills IM, 'European Logistics: Warehousing the future' 10. Fraunhofer IIS, 'Top 100 in European Transport and Logistics Services 2015/16' 11. Colliers, 'EMEA Q2 2012, Top European Logistics Hubs' 12. Sky Rise Cities, 'The Blue and Golden Bananas of Europe' 13. FEM European Materials Handling Federation, 'Statistics 2016' 14. Eurostat, 'Data Explorer' 15. Statista, 'Material Handling Equipment Production Value in Europe' 16. Technavio, 'Material Handling Equipment Market in Europe 2015 – 2019' 17. Technavio, 'Material Handling Equipment Market in Europe 2015 – 2019' 18. Mordor Intelligence Europe, 'Automated Material Handing Market' 19. Financial Times, 'Robots Gain Ground in E-commerce Warehouses' 20. Savills IM, 'European Logistics: Warehousing the future' 21. Technavio, 'Pallet Market in Europe 2018 – 2022' 22. Technavio, 'Material Handling Equipment Market in Europe 2015 – 2019' 23. eCommerce News, 'Wanted in Europe: Prime Warehouses' 24. Savills IM, 'European Logistics: Warehousing the Future' 25. eCommerce News, 'Zalando's Logistics Centre will be Biggest in Europe' 26. Avanta UK, 'Top 14 Largest Warehouse in the World' 27. UMD Automated Systems, 'Top Five Material Handling Trends Changing the Industry' 28. Modern Materials Handling, 'Top 20 Material Handling System Suppliers in 2017' 29. Retail Index, 'Top 30 Retailers in Europe' 30. Modern Materials Handling, 'Top 20 Material Handling System Suppliers in 2017' 31. Daifuku, 'Latest Financial Information' 32. SSI Schaeffer, 'Company' 33. Dematic, 'About' 34. Vanderlande Industries, 'Company Profile' 35. Murate Machinery, 'Muratec Profile' 36. Honeywell AIDC, 'Home' 37. TGW Logistics, 'Company' 38. Buemer, 'About Buemer Group' 39. Fives Group, 'A Unique Organisation' 40. Swisslog AG, 'About'
Finally to the individual members of the EPTDA Know Your Market Committee and particularly to its Task Group, who have freely given their advice, guidance and inputs throughout the process of producing this document.
Acknowledgements
Disclaimer: costed examples document illustrations taken from real practice. They are, however, predictions of future value projects be undertaken in this sector. commercial decisions examples.
The
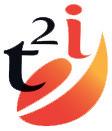
The authors, contributors and EPTDA do not accept any liability for any
are
Also to a number of technical experts from distributor members of EPTDA operating in this sector, who have provided the concrete examples included in the text and without whose contribution the document would lack its operational and commercial relevance and power for distributors.
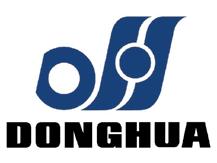

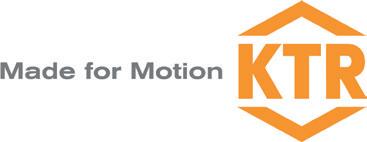
26
that can
Acknowledgements and a sincere thank you to the following manufacturer members of EPTDA for the generosity of the technical and commercial information and advice that they have supplied and which has given real authority to the document.
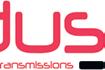
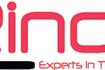
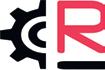
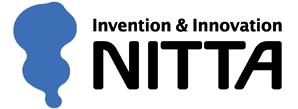
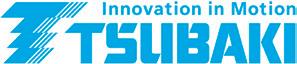
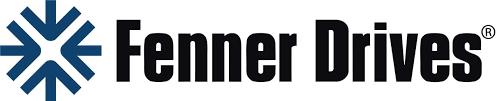


Authored by:
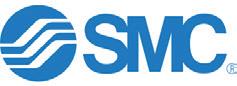
that may be taken as a result of these
contained in this
not
WWW.EPTDA.ORG Copyright © 2019 EPTDA. All rights reserved. This work is registered with the IP Rights Office Copyright Registration Service Ref: 284729428