5 minute read
Precisie 5-assig frezen voor maritieme sector
Marin freest precisie schaalmodellen van scheepsschroeven voor stromingsanalyses
Scheepswerven en rederijen uit de hele wereld komen naar Wageningen om hier hun schaalmodellen te laten testen. Want het Maritiem Research Instituut Nederland bootst op schaalgrootte elke zee, elke getijdestroom en elke storm na. Samen met 5-assige precisie freestechnologie voorkomt dit dat rederijen voor verrassingen komen te staan als hun schip in de vaart komt.
Scheepswerven worden afgerekend op de snelheid die de schepen halen als ze in de vaart worden genomen. Een paar procent afwijking, kan duur uitpakken. Heel vroeger grepen engineers naar de oplossing om de aandrijving over te dimensioneren. Dat willen de rederijen niet meer. Brandstof- en milieu-eisen spelen tegenwoordig ook hier een rol. “Net als wasmachines hebben de schepen energielabels en moeten we aantonen dat we tijdens de levensduur efficiënt omgaan met energie”, zegt Jan de Boer, senior project manager bij het Maritiem Research Instituut Nederland (Marin). Het instituut, ooit ontstaan als een samenwerking tussen de scheepvaartindustrie, defensie en de Nederlandse overheid, beschikt over zes grote sleeptanks, waarvan de grootste 250 meter lang is.
Fysieke modellen
CFD-software (Computational Fluid Dynamics) is onmisbaar geworden in de ontwerpfase van een scheepsschroef. Maar de fysieke modellen blijven voor de testen nog altijd hard nodig. “Scheepswerven willen de onzekerheid omtrent de efficiency van de aandrijving terugdringen tot 1 à 2 procent.” Daarom freest Marin gemiddeld zo’n 70 tot 80 schaalmodellen van de scheepsschroeven per jaar. Momenteel is het drukker, omdat voor een Joint Industrie Project alléén al komende anderhalf jaar zo’n 150 schroeven gefreesd moeten worden. De schroeven worden ingebouwd in exacte schaalmodellen van de schepen waarmee Marin vervolgens in een van de sleeptanks testen gaat doen. Heel nauwkeurig brengen de analisten de stromingen rondom de schroef in beeld; eerst
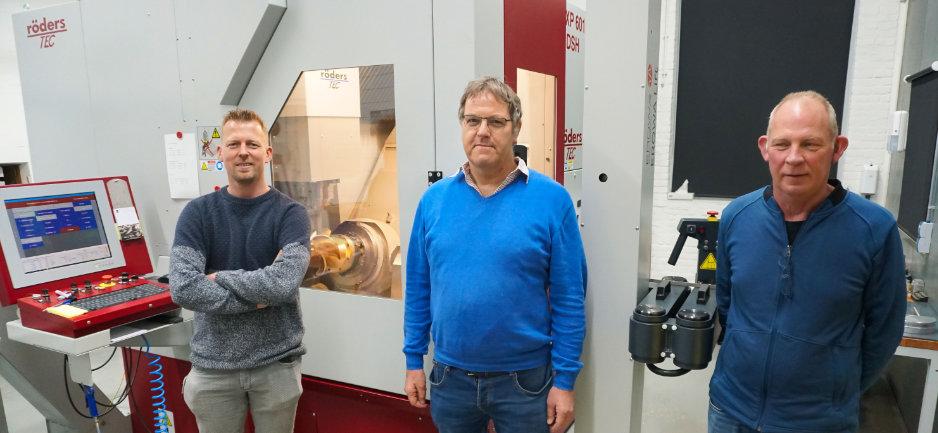
Van links naar rechts Geurt-Jan Hoogakker, Jan de Boer en Ronald Klomp.
met een stock schroef en daarna met een schroef die ontworpen wordt aan de hand van het volgstroomveld van het schip. Die data gebruiken ze om het noodzakelijk vermogen te berekenen wil het schip aan de eisen van de rederij voldoen. Ook testen ze op het ontstaan van cavitatie rond de schroef. Jan de Boer: “Over- en onderdruk bij de schroef zorgen voor de stuwkracht. Cavitatie zijn luchtledige bellen die ontstaan bij hele lage drukken op het schroefblad en die, als deze in een gebied met hogere druk komen, imploderen.” Er ontstaan drukgolven richting het schroefblad. Die zorgen voor trillingen, geluid en op de duur kan het materiaal uitbreken en de schroef beschadigen.
“Dankzij de lineaire Z-as kunnen we de voeding in alle richtingen gelijk houden”
Lineaire Z-as
De vorm- en maatnauwkeurigheid van deze schaalmodellen liggen op een hoog niveau. Een gevolg van de hogere nauwkeurigheid waarmee de uiteindelijke schroeven worden geproduceerd, zegt Jan de Boer. “Als je een schaal van 1:20 gebruikt, verklein je het tolerantieveld met een factor 20.” Daarnaast zijn de metingen waarmee Marin de testen uitvoert veel nauwkeuriger geworden, geeft Geurt-Jan Hoogakker, CAM-programmeur, als tweede reden aan. “Als je nauwkeuriger meet, moet je ook nauwkeuriger produceren.” Dat ging steeds moeilijker en kostte teveel tijd op de 3-assige CNC-machine waarmee het maritiem instituut jarenlang heeft gewerkt. Daarom is in 2018 de stap naar 5-assig simultaan frezen gemaakt. Daarbij is gekozen voor de Röders TEC 601 DSH CNC-machine. Het feit dat Röders in alle assen lineaire aandrijvingen toepast, ook in de Z- as, heeft de doorslag gegeven. De Duitse machinebouwer, voortgekomen uit de productie van nauwkeurige matrijzen voor de flessenindustrie, heeft in de voorbije twintig jaar veel ervaring opgedaan met lineaire aandrijvingen. Deze worden in eigen huis ontwikkeld. Ook de Z-as in de 5-assige bewerkingscentra wordt lineair aangedreven. “Dat heeft direct invloed op de dynamiek van de machine. Hierdoor kunnen we voeding in alle richtingen gelijk houden”, zegt Geurt-Jan Hoogakker. Dit draagt met name bij aan het frezen van scherpe randen aan de dunne schoepbladen. De lineaire assen voorkomen eveneens omkeerspeling bij 5-assig frezen met hoge snelheden.
Unieke besturing
Daarnaast beschikt de Röders TEC 601 DSH over realtime spindelcompensatie in de Z-as. Tijdens de bewerking compenseert de besturing voor een eventuele uitzetting van enkele microns. Een derde punt waarop de Duitse fabrikant van precisiemachines zich onderscheidt, is de eigen besturing die bij het berekenen van de freesbanen exact de punten in het CAM-programma volgt, waar andere besturingen het gemiddelde van de geprogrammeerde lijn pakken. Door veel meer punten te nemen, freest de machine nagenoeg 100 procent de vormnauwkeurigheid van het model. Jan de Boer: “We hebben vier machinebouwers gevraagd een schroef te frezen. Röders verraste ons met het resultaat.” De eigen besturing is hier een voordeel; het was wel een punt waar het Marinteam kritisch naar gekeken heeft. “Je koopt immers iets unieks; maar ze hebben ons overtuigd geen risico te lopen. De hoog frequent drives voor deze aansturing zijn uniek, voor de rest gebruiken ze off the shelf componenten.”

Om de hoge nauwkeurigheid te halen, worden de schroeven na een warmtebehandeling nog zo’n 10 tot 12 uur nagefreesd op de Röders TEC 601 DSH
Hoge nauwkeurigheid
De Röders TEC 5-assige bewerkingscentra halen een maatnauwkeurigheid van 5 µm. Bij Marin freest men de scheepsschroeven, tot 34 centimeter diameter, met een volumetrische nauwkeurigheid van 20 µm. Geurt- Jan Hoogakker: “De vele punten die de besturing volgt, is het grote voordeel van de Röders besturing. Daardoor haal je de hoge vormnauwkeurigheid.” Het vergt wel een juiste afstemming tussen machine, Hypermill als CAMprogramma en de postprocessor. Jan de Boer: “Vaak zie je dat de CAMleverancier het probleem over de schutting gooit bij de ontwikkelaar van de post processor en die weer bij de machinebouwer. Röders reageerde heel snel op onze vraag. Het is een sterk punt dat ze meteen een expert hierheen stuurden om met de CAM-ontwikkelaar en de ontwikkelaar van de post processor te optimaliseren.” Het zijn forse programma’s die de drie CAMprogrammeurs voor de ene Röders machine maken. Programma’s van 8 miljoen regels zijn geen uitzondering. De besturing en machine zijn daarbij zo nauwkeurig, dat iets dat op het scherm goed lijkt, in werkelijkheid een fout in het oppervlak kan opleveren. “Als je een scherpe leading edge hebt, moet je de spline interpolatie wat verder uit elkaar leggen. Dan frees je een goed oppervlak.” De CAM-programmeur geeft hiermee aan dat de kwaliteit uiteindelijk een optelsom is van alle processtappen. En als de machine heel nauwkeurig is, ontstaan er elders in het proces nieuwe uitdagingen. Ronald Klomp, instrumentmaker bij Marin: “Materiaaleigenschappen spelen nu een rol. Hierdoor gaan we afwijkingen zien. Als we tussen het voorfrezen en nafrezen de schroef spanningsvrij gloeien, zie je al direct een betere oppervlaktenauwkeurigheid.” Hij is er ook van overtuigd dat de overgangen tussen de segmenten, die je nu wel ziet maar die niet gemeten worden, kunt wegkrijgen door nog langer na te frezen. “We willen het handmatig polijsten helemaal elimineren maar dat vergt anderhalve dag extra frezen.” Die stap zet Marin pas als de 150 schroeven gefreesd zijn.
Dymato [www.dymato.nl] Marin [www.marin.nl]
.