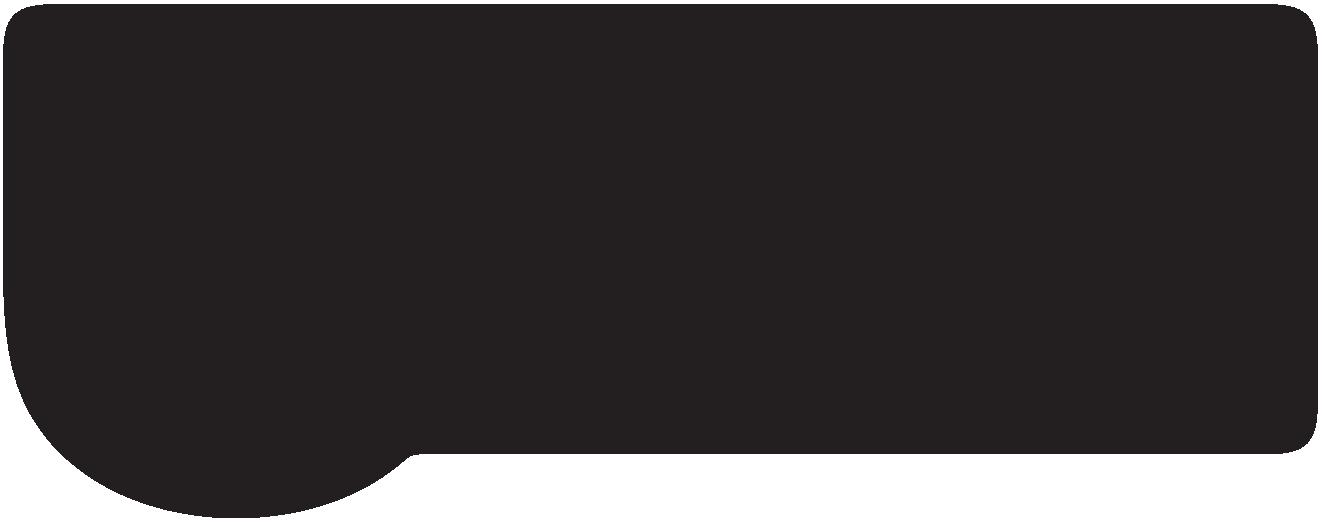
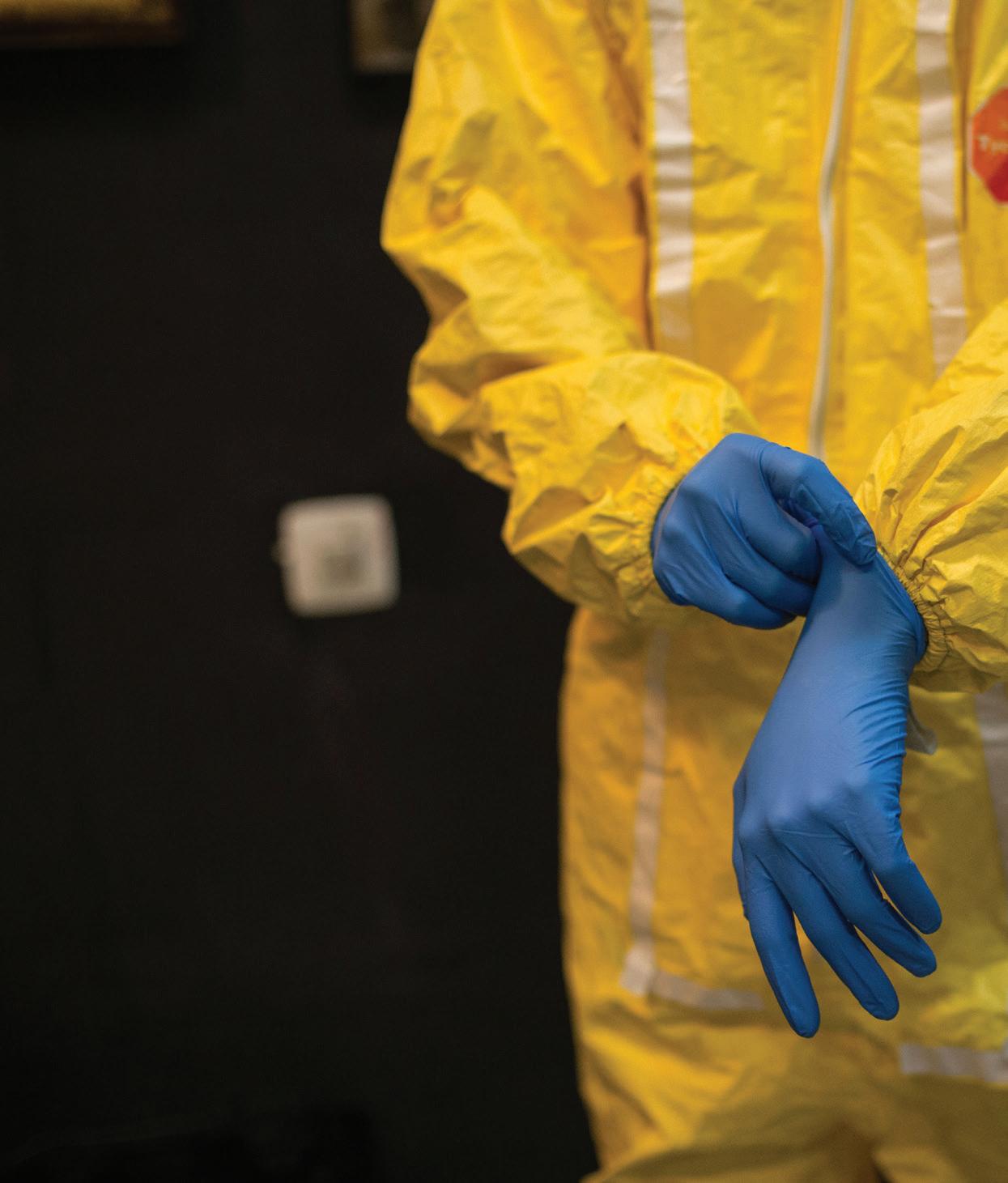
ENERGY STORAGE
PROJECT SUPPORTS
SMART GRID TRANSITION
URBAN AND RURAL COLLABORATION KEY TO SOLVING WATER
CHALLENGES
DIGITAL TECHNOLOGIES
CRUCIAL IN THE AGE OF SOCIAL DISTANCING
INDUSTRY
RESPONSE: COPING WITH COVID-19
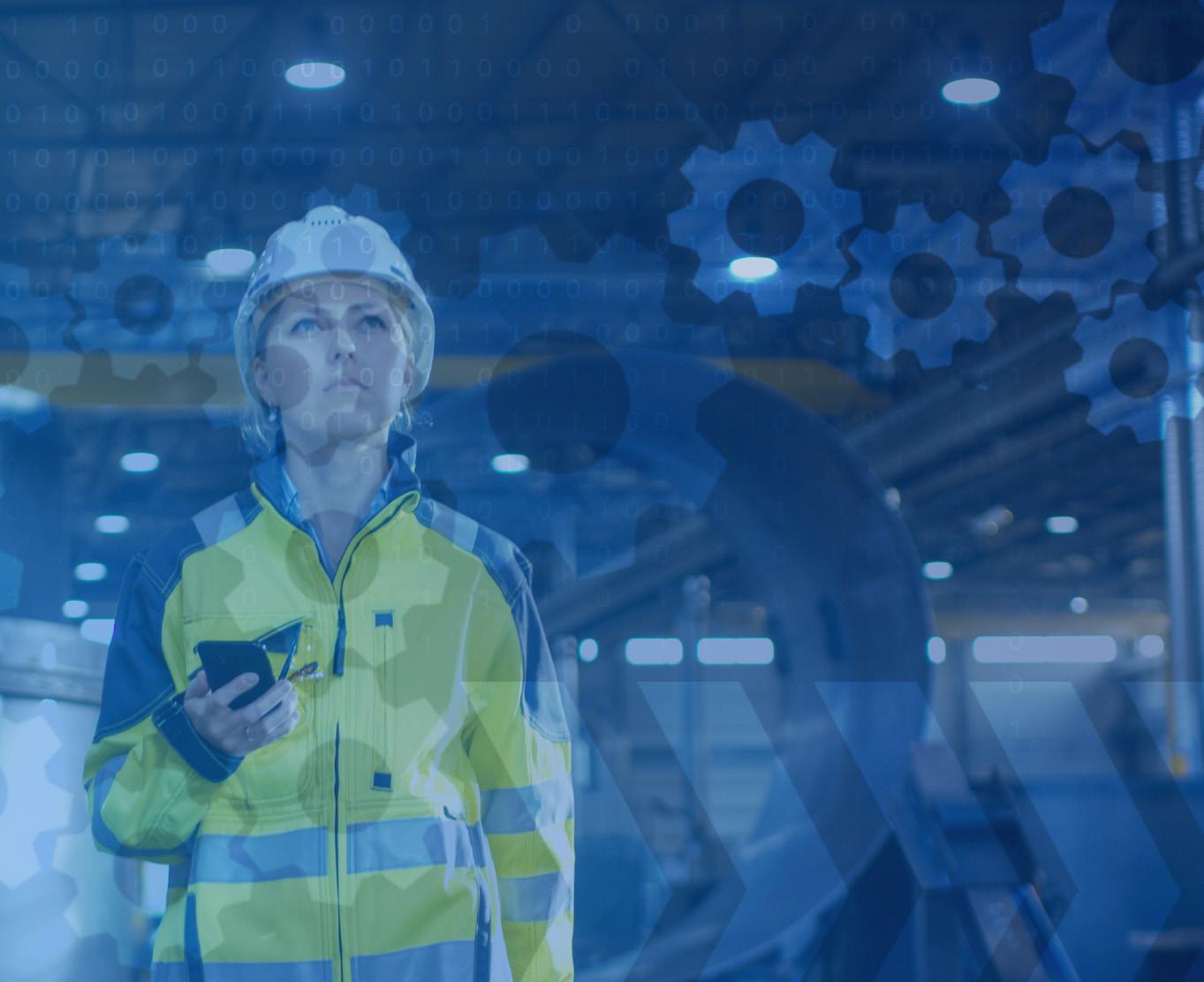
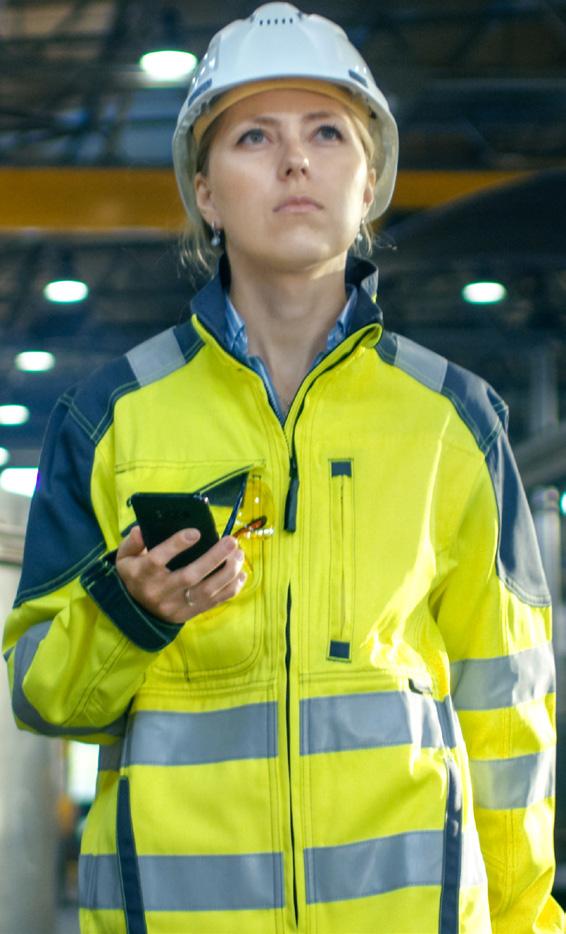
ENERGY STORAGE
PROJECT SUPPORTS
SMART GRID TRANSITION
URBAN AND RURAL COLLABORATION KEY TO SOLVING WATER
CHALLENGES
DIGITAL TECHNOLOGIES
CRUCIAL IN THE AGE OF SOCIAL DISTANCING
INDUSTRY
RESPONSE: COPING WITH COVID-19
With a SMART Motor Control system and the help of our condition monitoring products, NHP and Rockwell Automation help you keep your plant floor running by detecting potential mechanical issues before they impact production.
For more information on our realtime protection modules, sensors, surveillance software and portable instruments, call NHP today.
he May 2020 edition of Utility has gone to print amidst an unprecedented backdrop of change – with previously unknown terms such as “social distancing” and “flattening the curve” now part of our everyday lexicon, highlighting the strange reality in which we currently exist.
The industry response has been nothing short of remarkable – both the energy and water sectors have been working tirelessly to ensure the reliable and efficient operation of essential services in these challenging times.
Utilities have also been quick to reassure customers that they have the necessary precautions in place to maintain supply while protecting the safety of employees and the community. Go to page 18 for a more detailed analysis of how COVID-19 is impacting the utility industry.
Across the world, COVID-19 is changing the way we live, work and communicate. As we remain, for now, physically distant from one another, digital technologies can at least help us stay socially connected.
Less than a week out from Utility’s flagship event, it became evident that an online conference was the only way forward for Digital Utilities 2020. It was a massive team effort to set up and test the Zoom tele-conferencing platform, adjust the program to reflect the new format and notify all delegates about the change of plan.
However, by embracing and adapting to the rapidly changing circumstances, Digital Utilities was able to create something of value for all participants and ensure conversations around the highly relevant topic of digital transformation could still take place. You can read more about how the event went in our wrap-up article on page 24.
Following the success of the Digital Utilities webinar, we will be hosting a series of virtual conferences on topics designed to assist the industry with the challenges ahead. The Disaster Management virtual conference will explore how Australia’s essential service providers have, and will continue to, manage the COVID-19 crisis, and what this means for future resilience operations.
The Smart Cities virtual conference will look at the essential skills and services the smart cities sector provides, and analyse the ways in which the sector will adapt and change as a result of COVID-19. This event is being delivered in conjunction with the Australian Smart Communities Association, the peak industry association in Australia for our rapidly developing digital, sharing and interconnected communities. To find out more about our different virtual conferences, please contact events@monkeymedia.net.au.
As Australians continue to face tight restrictions on all aspects of daily life, one of the key messages of hope is around unity and the idea that “we will get through this – together”.
Cameron FitzGerald, Managing Director of Southern Rural Water, iterates this message in our water management feature, emphasising that the urban and rural water sectors must work together to deliver a secure water supply, and identify opportunities to learn and grow from each other.
This edition also features ElectraNet’s Dalrymple Battery Energy Storage System (BESS), which won Energy Networks Australia’s 2019 Industry Innovation Award. The remarkable project is now in full commercial operation and is the first BESS in the National Electricity Market (NEM) to provide both regulated network reliability and security services alongside competitive market services.
The project has incorporated a knowledge sharing portal, which provides a significant amount of information to assist the entire utility industry in observing first-hand how the Dalrymple BESS is performing – another positive example of industry collaboration for the benefit of all. It is worth noting that some of the editorial in this edition predates the COVID-19 crisis, but there continues to be industry-wide consultation on pandemic response measures to ensure people, assets and security of supply are protected.
Thank you for your continued support of Utility – it is appreciated more than ever. If you’re working from home and haven’t updated your postal address, please get in touch and we can temporarily redirect your subscription.
Most importantly, stay safe.
Afreak storm event in late January 2020 knocked six transmission towers to the ground and damaged a seventh just north of the town of Cressy in Western Victoria. This event caused an outage on the Moorabool to Mortlake and Moorabool to Haunted Gully transmission lines.
Supply to the Portland aluminium smelter was interrupted, and the Heywood interconnector between Victoria and South Australia was impacted, separating South Australia from the National Electricity Market.
Despite the damage, AusNet Services, the primary declared transmission system operator for Victoria, had temporary towers in place for the Moorabool to Mortlake line in just over two weeks of the incident occurring.
Considering transmission towers are significant structures designed to withstand extreme weather, what happened to cause the towers to collapse?
It was an extreme localised storm event late in the afternoon on Friday 31 January that caused the damage.
Winds in excess of 160km/hr (44m/s) created a hefty downdraft known as a downburst that is believed to have flattened six steel transmission towers completely transversal/perpendicular to the wind direction.
Significant damage to transmission equipment is a rare event, so the emergency reconstruction of seven towers and two 500kV lines is no mean feat.
AusNet Services organised operators to isolate and earth the lines, and immediately deployed local delivery partners who quickly reached the site in Cressy to assess the damage.
At the same time, AusNet Services worked closely with the Australian Energy Market Operator (AEMO) to restore supply to the Portland aluminium smelter on a contingency basis, utilising the services of Origin’s Mortlake Power Station.
Preliminary design works for the temporary reconstruction of the transmission towers were completed two days after the storm.
TransGrid, ElectraNet and Powerlink provided a conductor which helped accelerate the restoration process of the first line.
Three days after the storm event, materials for the temporary towers arrived on site ready for construction works to commence the following day.
The seven damaged towers each held double circuit 500kV lines along the Moorabool to Mortlake and Moorabool to Haunted Gully transmission lines.
The two sets of temporary towers that have been reconstructed are each designed to hold one of the two restored 500kV circuits. In the interests of restoring the lines as quickly as possible, one 500kV line was restored at a time, building temporary towers for each line. This process also helped ensure a more secure transition for the Portland aluminium smelter from its contingency arrangement.
The first line was repaired and re-energised by 17 February and the second line was back in service by 3 March.
More than 110 experts from AusNet Services’ delivery partners and interstate transmission peers helped with the construction of the temporary towers and removal of the fallen infrastructure.
The Bureau of Meteorology had predicted some storm activity on 31 January, but not the extreme weather that was experienced.
At the time of the storm, more than 500MW was being exported from SA to Victoria via Heywood. Seconds later the interconnector had reversed and was importing 500MW into SA until the Mortlake Power Station reduced generation.
The 1,000MW turn around caused wind and gas plants to trip or back off in SA. Grid-connected batteries provided a significant amount of frequency control ancillary services (FCAS). This response avoided a high-frequency collapse on the SA power system.
The Portland aluminium smelter tripped off initially but was brought back on to avoid the potlines solidifying, with supply for the Victorian facility provided by Origin’s Mortlake Power Station.
System improvements instituted post the 2016 event helped the grid to remain stable in SA, given the severity of the disruption. The FCAS services from grid-connected batteries were vital to this task.
There will no doubt be plenty of learnings to come, but through an industry combined effort that included AEMO, TransGrid, ElectraNet and Powerlink, AusNet Services and its delivery partners were able to provide a temporary solution in a very short timeframe.
Strengthen industrial cybersecurity without compromising efficiency.
As industrial devices become more connected through the Industrial Internet of Things (IIoT) there is not only great potential for businesses to optimise operations, there is also a significant challenge – cybersecurity. Moxa’s range of robust network devices meet the technical security requirements of the globally recognised IEC 62443 standard, which ensures your industrial control systems are well protected against network intrusions or attacks.
Connect with confidence.
Madison Technologies has been distributing Moxa’s reliable networking infrastructure Australia wide for more than 14 years. Our team is dedicated to ensuring our Moxa portfolio is fully supported with an extensive range held locally across our national supply chain, and a team of Moxa certificated sales and technical support engineers.
Although the short-term focus for society and water utilities is managing the COVID-19 pandemic, WSAA also retains a focus on long-term issues.
Ensuring all water supply options are on the table is a key focus for WSAA. In October 2019, we released our All Options on the Table report, which focuses on one option that is sometimes left off the table – purified recycled water for drinking. The report looks at insights and perspectives regarding community engagement, from places around the world where it has been considered and in most cases, adopted.
It includes ten lessons and global case studies, as well as recommended actions based on the learnings from these case studies. The report includes world-leading maps showing that purified recycled water for drinking has been adopted by 35 cities around the world, with more to come. That does not include the myriad cities all over the world where unacknowledged reuse has long occurred.
The report is not intended to identify purified recycled water for drinking as the way forward for specific locations but to go through key lessons learnt and consider how to have a conversation with the community should it be a future supply solution.
Some of the key findings on community education engagement include:
• It can be done – many towns in many countries have chosen it among other options as a safe and sustainable part of their water supply
• The three ‘t’s – time, trust and transparency – are crucial elements in engaging with any community
• Seeing is believing – there is immense value in running a demonstration project to showcase and prove the technology. As part of this, establish a visitor centre or experience so that people can see the systems in action, learn how it all works and ask any questions in a calm, fun learning environment. This could include tasting the water
• Wording and imagery are critical – words and images create perceptions and reactions, so it’s really important to choose these carefully
• News media coverage has a profound impact on public acceptance, and political support is essential
• Grassroots education and engagement can be more effective than high-profile marketing activity or ‘above the line’ presence
• General education around the urban water cycle and context will help prevent stigma and encourage acceptance
• Regulators play a powerful role
In August 2019, the Australian Infrastructure Audit 2019 report from Infrastructure Australia stated that “ensuring all options are on the table, and can be deployed when required, is likely to be essential for governments and operators to effectively and efficiently ensure secure supply over the long term”.
Later in 2019, WSAA asked nearly 10,000 Australians if they were interested in hearing about how the water industry
can purify water from a range of sources to drinking water quality or better – 57 per cent said they were interested in hearing more.
Our customer research in late 2017 found that acceptance of different drinking water sources varies across demographics and regions. It found higher acceptance levels in Perth and Brisbane which have both engaged in higher levels of public discussion around this area compared to other locations. Based on that, we found a correlation between communities engaging in public discussion and having purified water recognised as a viable option.
We have produced materials about visitor centres around the world, which are often part of a demonstration project. It would be valuable to see a demonstration project established in eastern Australia – as Water Corporation did in Perth while considering its Groundwater Replenishment Scheme.
WSAA also has a range of easy to use videos, animations, posters, expert testimonials and other resources. These will help any utility looking to start or continue the conversation with their community about purified recycled water for drinking.
The All Options on the Table report is available on WSAA’s website: https://www.wsaa.asn.au/publication/all-optionstable-lessons-journeys-others
For more information on this work, please contact Danielle Francis at WSAA: Danielle.francis@wsaa.asn.au
The Queensland NSW Interconnector (QNI) upgrade project will advance to the next stage after clearing a major review from the Australian Energy Regulator (AER).
The AER announced it had approved the Regulatory Investment Test for Transmission (RIT-T) on 30 March 2020. This determination supports the options assessment, costs and net benefits of the QNI project.
The $230 million QNI upgrade project, proposed by TransGrid and Powerlink, aims to increase transmission capacity between Queensland and New South Wales.
The AER has fast tracked its consideration to support the timely completion of the project. TransGrid expected that construction of the project would start in March 2020, with delivery and completion of inter-network testing expected by June 2022.
The project is expected to add an extra 60 cents to the transmission component of annual customer bills in New South Wales.
AER chair, Clare Savage, said the Liddell Power Station was scheduled to close in 2023, which would reduce the generation capacity in New South Wales.
“The proposed interconnector upgrade will allow more electricity to be exported from Queensland to New South Wales avoiding the need for costly new generation,” Ms Savage said.
The RIT-T is a cost benefit
assessment of the proposed interconnector. AER tested the reasonableness of TransGrid and Powerlink’s inputs and assumptions across a range of scenarios.
It found that the project was robust and would deliver a net economic benefit to Australian energy consumers.
“The investment is expected to deliver $170 million in net benefits to consumers and producers of electricity, and to support the ongoing energy market transition. The cumulative benefits are expected to exceed the investment cost within seven years,” Ms Savage said.
“We’re saying that the assessment by TransGrid and Powerlink stacks up and that consumers will get value for money from this investment.
“The proposed interconnector will help to address potential system security problems and alleviate upward pressure on wholesale electricity prices.”
TransGrid has separately applied to the AER to amend its existing revenue determination to recover the efficient costs of delivering the project. The AER will make a separate determination on this element in April 2020.
TransGrid’s Executive Manager of Works Delivery, Michael Gatt, said the company welcomed the AER’s determination.
“The QNI upgrade is important because it will increase the capacity to share electricity between Queensland and New South Wales, and reduce current and forecast network
constraints,” Mr Gatt said.
“It will ensure greater reliability of lowest cost electricity, as we enable more efficient sharing on the NEM and introduce more innovative technology to the system. The project is expected to provide net benefits of $170 million to electricity customers and producers.”
TransGrid is upgrading the 20-yearold transmission lines and three substations at Tamworth, Dumaresq and Armidale.
“It will allow 460MW more power to transfer into Queensland, and 190MW more into New South Wales and the ACT when it’s needed, and it will link customers to the National Energy Market.
TransGrid began working with Queensland transmission business Powerlink to initiate the RIT-T process in November 2018 and a number of network and non-network options were considered.
The project has been supported by the Australian and NSW Governments which have provided joint-underwriting to enable TransGrid to accelerate the delivery of the upgrade.
Mr Gatt said early works have commenced on the upgrade project which is expected to be delivered in September 2021.
“TransGrid is already working to deliver the upgrade, conducting environmental, geotechnical and site surveys, and engaging with communities along the existing transmission line corridor.”
The Water Services Association of Australia (WSAA) has announced a new partnership to launch an industry-leading Innovative Technology Program.
WSAA will partner with Isle Utilities and ThinkPlace to deliver the program for WSAA and its members.
The partnership offers a unique synergy between humancentred design and technology due diligence; visioning and co-design through to the identification and evaluation of leading-edge technology and innovation.
WSAA Executive Director, Adam Lovell, said, “Our partnership with Isle Utilities and ThinkPlace has been created following a global, competitive tender, and it seeks to facilitate collaboration, knowledge sharing, networking and cooperation in technology innovation across the entire WSAA membership.”
Managing Director of Isle Utilities (Asia-Pacific), Dr Michael Storey, said, “We look forward to delivering a seamless, endto-end experience for all WSAA members to define strategy, provide access to technology and innovation, and provide expertise to assist implementing these technologies.”
Isle is a leader in technology innovation and has developed a global ecosystem of 350 water users, including 200 leading water utilities, and more than 6,500 technology providers.
Global Partner of ThinkPlace, Dr Nina Terrey, said, “We are excited to partner with Isle Utilities and bring our design thinking approaches to driving positive impact in the water sector.”
Isle and ThinkPlace have a specialised team of 100 across Australia and New Zealand as well as a global team of 200 spanning six continents and 13 countries.
The CEO of Hydro Tasmania, Steve Davy, will step down when his contract ends in late 2020.
Steve Davy has been serving as the Chief Executive Officer of Hydro Tasmania for almost seven years, and has been with the business for over 15. Prior to being the CEO, Mr Davy was the Chief Commercial Officer, managing commercial operations that include supporting mainland retailing, contract and spot trading, major customer negotiations, supplier arrangements, and a range of operational activities.
Hydro Tasmania’s Chairman, Grant Every-Burns, announced Mr Davy’s resignation, and explained that Mr Davy had led the business through the energy supply challenge to being at the forefront of Australia’s renewable energy transition.
“Under Steve’s leadership, Hydro Tasmania has laid the groundwork for our future success as a business,
taking a bold vision for the role Tasmania can play in a renewable energy future and turning it into an actionable plan through the Battery of the Nation initiative.
“On behalf of the board, I thank him for his dedication, passion and hard work,” Mr Every-Burns said.
Mr Davy said he was proud of the achievements of the Hydro Tasmania team over the past 15 years, particularly the business’ support for the Tasmanian community.
“Now in its fourth year, our Community Grants Program has funded 20 projects throughout Tasmania, supporting everything from music, dance, historical preservation, healthy eating and mental health initiatives.
“Our new education program ‘Generation Hydro’ is now helping Tasmanian students learn about renewable energy and the opportunities for STEM careers here in Tasmania.
“I have great pride in the way our people responded to the energy supply
challenge, and I am also very proud of the work that has been done to identify and drive the opportunity for Tasmania to help Australia’s transition to a renewable energy future, and I will watch with interest as the Battery of the Nation vision and Tasmania’s recently announced 200 per cent renewable energy target become a reality.”
Hydro Tasmania has engaged executive search firm Heidrick & Struggles to assist in the recruitment of a new CEO.
Trains the model to identify defect classifications.
Detect anomalies faster and fix infrastructure
sooner
Action insights more often
Streamline pipe asset management operations
More capacity for complex analytical tasks
Uses AI to review CCTV footage of pipes to identify cracks and anomalies.
Drafting and planning systems more accurately to achieve desired functions
Piping vibration, thermal and stress analysis
Sourcing more valuable engineering solutions
More thorough site inspections
Compliance with authority codes
Global application - applicable to any pipe material
Ability to apply expert classification and further train the model as the database builds
Concise classified defect report generated at completion of analysis
Generates a concise defect report to inform future maintenance plans or repair schedules.
Detect up to 15% more defects than a manual review
Contact us to find out how Pipe Ai can deliver better efficiencies within your organisation.
+61-7-3532 1300
enquiries@peakai.com.au
www.peakai.com.au
Longitudinal Crack Blockage Fine RootsThe Australian Energy Market Commission (AEMC) has published three milestone reports detailing its progress to deliver access reforms to Australia’s energy grid.
The reforms fall under the Coordination of Generation and Transmission Investment (COGATI) review.
Reforming the way generators access the grid remains critical to the future of the National Electricity Market (NEM) and represents the cheapest, fastest and fairest path towards a low-emissions energy sector.
AEMC’s access reforms are designed to integrate new technologies into the national grid in a way that’s reliable, secure and works in consumers’ best interests.
The reforms aim to rethink the NEM to develop price signals that will preference lowest cost and lowest emissions energy, keep power bills trending down and support transmission investment without repeating ‘gold plating’ mistakes of the past.
The three reports, which follow on from COAG Energy Council’s consideration of access reform at its meeting on 20 March, are:
• An update paper, which provides a recap of the case for change and updated key features of the model to address integration and congestion issues associated with the rapid transformation of Australia’s energy generation mix
• A technical blueprint for the access model that incorporates stakeholder feedback to date and will be used in further consultations during 2020
• A benchmarking study from NERA Economic Consulting on the benefits, costs and experiences of transmission access reform in other countries. The study estimates reform benefits that considerably outweigh the costs. NERA’s best estimate of the total benefits for consumers of the reforms is $387 million in savings per year – equivalent to two per cent off the cost of wholesale energy
AEMC Chair, John Pierce, said the Commission would, through the ESB’s market design process, continue to refine and develop the access reform model with stakeholders over the course of 2020.
“This will allow us to develop draft rules by the end of the year. While we have allowed extra time to further develop the detailed design for the model, what hasn’t changed is that this work was always, and will continue to be, integral to the Energy Security Board’s 2025 market redesign,” Mr Pierce said.
“This is because the transmission challenges facing the grid have a two-part solution. The first is actioning AEMO’s Integrated System Plan so that the right transmission is built and the second is implementing access reform so that the investments in that transmission are effective in the long term.
Through its innovative solutions, Veolia Water Technologies enables industry, local authorities and citizens to optimize their use of resources for more efficient, environmentally-friendly and socially responsible outcomes.
We understand the importance of increasing the value of water and we do so by supplying high quality water, treating and reusing wastewater, producing and/or recovering energy, extracting raw materials and capitalizing on valuable byproducts.
www.veoliawatertechnologies.com.au
“Both of these levers are fundamental to any market redesign because if you do the first and not the second, you pay billions to defer, not remove, current inefficiencies in the system. If we don’t tackle these issues holistically we also won’t keep power prices trending down – and we won’t realise the full emissions value of the renewable revolution.”
The access reforms rely on generators ‘doing their bit’ by improving the way they bid electricity into the market, making sure the cheapest, greenest energy gets dispatched most effectively. The result will be lower emissions and significant consumer cost savings.
In return, generators will receive better information on where to invest and more certainty on what profits they will make. For those more affected by the reform, the AEMC is proposing ways to help them through the transition, so everyone benefits in the long term.
“While these proposals are new for Australia, the changes we’re suggesting have been successfully in place for decades in many parts of the world including New Zealand, North America and Singapore,” Mr Pierce said.
“And they have shown significant benefits for consumers, as the benchmarking document we publish today shows.
“We are conscious though, that change must be managed carefully. This is why we have conducted an exhaustive
stakeholder engagement process around the reforms.”
Engagement to date includes:
• 151 written submissions on four consultation papers
• Six technical working group meetings
• Two public workshops
• More than 130 bilateral meetings and workshops with the ESB, AER, AEMO, consumers, Transmission Network Service Providers, incumbent and prospective generators, existing and prospective investors, government departments and other interested parties
“Our engagement will continue as we work together with our stakeholders on implementing these important reforms,” Mr Pierce said.
“Engaging with stakeholders in a considered way has always been fundamental to the way we work and will continue to be.”
Further detail on next steps for stakeholder engagement will be released shortly.
The AEMC has engaged NERA Economic Consulting to quantitatively model the reforms for the National Electricity Market. The results will inform the final access reform model blueprint.
•
•
•
Genex has signed a 30-year Energy Storage Services Agreement (ESSA) with EnergyAustralia for the 250MW Kidston Pumped Storage Hydro Project.
Key terms of the ESSA include:
• A term of up to 30 years, with an initial term of ten years and two options (at EnergyAustralia’s election) to extend for a further ten years each (Extension Options)
• Genex will provide the full operational dispatch rights for the K2-Hydro plant (including P&L responsibility) to EnergyAustralia in exchange for a fixed annual rental payment, escalating over the total term
• Following the expiry of the full 30-year term, and therefore conditional on the exercise of the Extension Options, EnergyAustralia shall have the right to acquire Genex’s shareholding in the project for a fixed cash payment
• The ESSA is subject to a number of conditions precedent, including achieving financial close for the project, which must be satisfied prior to the financial close sunset date of 31 December 2020
Genex remains deeply engaged with the other project stakeholders, including the Northern Australia Infrastructure Facility (NAIF) to complete the restructuring of the project financing on the basis of the agreed terms of the ESSA.
Genex CEO, James Harding, said, “Since November 2019, Genex has been actively working with all of its project stakeholders, including EnergyAustralia, NAIF and the Queensland Government, to complete the restructuring of the project financing for K2-Hydro and progress to financial close as quickly as possible.
“We have been extremely pleased with the support of our stakeholders and counterparties during this period and now believe, with today’s signing of the ESSA with EnergyAustralia, that we have the basis to move forward to financial close of the project.
“The K2-Hydro project will be the first pumped storage hydro project in the National Electricity Market in almost 40 years, and the first to be developed under private ownership.
“It will create over 500 jobs during construction and deliver significant economic benefits to Queensland through providing reliable generation for the grid and applying downward pressure on wholesale electricity prices.”
Seqwater’s Mount Crosby East Bank Water Treatment Plant, on Brisbane’s west, will undergo a filtration upgrade as part of a $35 million makeover to enhance water supply security for South East Queensland.
Natural Resources Minister, Dr Anthony Lynham, said the filtration upgrade would significantly improve the plant’s resilience to extreme weather events and climate change.
“The Mount Crosby water treatment plants, both East Bank and West Bank combined, are critical to the operation of the South East Queensland Water Grid and can provide up to half the region’s daily water supply,” Dr Lynham said.
The project, which is expected to take more than two and a half years to complete, will generate up to 100 jobs and deliver major improvements to the plant’s filter design and control.
“It will significantly improve the
plant’s ability to maintain water supply during extreme rain events and flooding to further improve the water supply security of our region,” Dr Lynham said.
Seqwater Chief Executive Officer, Neil Brennan, said the water grid would be used to supplement Brisbane’s water supply when the refurbishment works were being undertaken.
Mr Brennan said the work was being staged to ensure water supply was maintained, with six filters being taken offline at a time.
“Taking filters offline will result in reduced production at East Bank, with
the water grid and other treatment plants across the region helping to supplement supply to Brisbane and Ipswich during the project,” Mr Brennan said.
“This project will ensure that the East Bank can continue to supply safe and reliable drinking water to South East Queensland well into the future and be better equipped to deal with the impact of climate change.”
Filters play an essential role in the water treatment process, assisting with clarifying water prior to disinfection.
The upgrade work will help the plant be able to treat water with high levels of turbidity or sediment which can result from extreme rainfall events across the Wivenhoe catchment washing soil and debris into the creeks and waterways.
Water treated at the Mount Crosby water treatment plants comes from the Brisbane River, downstream from Wivenhoe Dam.
The Victorian Government has made the decision to remove the ban on onshore conventional gas exploration and production.
It introduced two bills to Parliament: one will enshrine Victoria’s fraccing ban into the state constitution, and the other allows for an orderly restart of the onshore conventional gas industry in the state. It will also introduce measures aimed at ensuring newly sourced gas within Victoria and state waters will be prioritised for domestic use.
In 2017, the Victorian Gas Program set about determining the potential for new onshore conventional gas discoveries and what would be the risks, benefits and impacts of allowing exploration and development.
The program has now delivered a large amount of work to answer these questions. The scientific studies have found there are likely to be onshore conventional gas resources in south-west Victoria and Gippsland.
The three years of studies has concluded that an onshore conventional gas industry would have no significant impact on farming because of the low risks to the environment or groundwater.
The gas program has shared the science with the community via more than 800 separate engagements.
Following the passage of the bill in Parliament,
the department will start working with industry and other stakeholders to amend the Petroleum Industry Regulations 2011
In line with the findings of the Victorian Gas Program, community engagement elements of onshore conventional gas projects will be strengthened.
In practical terms, the orderly restart will commence immediately with some specific milestones in place as the industry moves into gear from a standing start.
Onshore conventional gas development could potentially start from 2023-24 if industry makes a gas discovery, considers it commercially feasible to develop and secures the necessary regulatory approvals.
The Australian Energy Council (AEC) supported the Victorian Government’s decision. AEC Chief Executive, Sarah McNamara, said the decision was a sensible one supported by science.
“Ensuring reliable gas supplies into the future will help affordability for domestic, commercial and industrial customers,” Ms McNamara said.
“Readily available gas will also be an important, flexible backup fuel that is likely to help ensure the reliability of the state’s grid as older coal-fired power plants retire and more wind and solar generation comes into the system.”
As the fallout from the global COVID-19 pandemic continues to wreak havoc across the globe, Australian utilities have combined to tackle the challenges head-on. We take a look at the frontline response our essential service providers in the energy, water and telecommunications industries have rolled out in the immediate aftermath of the crisis.
The COVID-19 pandemic has rocked the global community to its core, wreaking a path of destruction across the world and prompting government responses not seen since World War II.
While economies globally have been battered and unemployment rates have skyrocketed, providers of essential services – like utilities – have found themselves run off their feet in a race to continue to meet customer needs, while maintaining new societal norms such as social distancing and working from home.
Here, we take a look at the steps the energy, water and telecommunications industries are taking to keep operating our essential services in these challenging times.
In the energy sector, federal and state governments have established a coordinated national approach to managing the impacts of COVID-19, fully supported by industry associations and energy utilities.
Federal Minister for Energy and Emissions Reduction, Angus Taylor, said the energy sector remains well-prepared to deal with the virus, and early action taken by governments and industry should ensure energy supplies for the coming months.
“One of my top priorities will always be to keep the lights on for Australian families and businesses,” Mr Taylor said.
“We also want to make sure that generators, retailers and networks are ready to support any customers who find themselves in difficulty due to the Coronavirus.
“The energy sector is good at responding to disruptions. The industry has well-established risk management, emergency management and business continuity plans, which are regularly tested and improved.”
A number of the state governments have announced payment freezes or subsidies for household and business energy bills.
The Western Australian Government has developed a $607 million stimulus package to freeze household fees and charges until at least 1 July 2021. The freeze will apply to the entire “household basket”, including electricity, water, motor vehicle charges, emergency services levy and public transport fares.
In New South Wales, a $30 million boost to the Energy Accounts Payments Assistance Scheme (which helps people experiencing a short-term financial crisis or emergency to pay their electricity or gas bill) has been announced.
Queensland meanwhile is giving sole traders, small and medium businesses a $500 rebate on their power bill for this year; and the Tasmanian Government has announced a $985 million stimulus package that will cap energy prices for 12 months and will waive the first quarterly bill after April 1 2020 for small business customers and community service organisations.
The Federal Government, through the Australian Energy Regulator (AER), has also set reasonable expectations of energy companies to protect householders and small business customers during the COVID-19 pandemic.
The AER’s Statement of Expectations sets out a range of measures, including:
• Waiving any disconnection, reconnection and/or contract break fees for small businesses which have gone into hibernation, along with daily supply charges to retailers, during any period of disconnection until at least 31 July 2020
• Offering all households and small businesses who indicate
they may be in financial stress a payment plan or hardship arrangement
• Not disconnecting customers who may be in financial stress, without their agreement before 31 July 2020 and potentially beyond
• Deferring referral of any customer to a debt collection agency for recovery actions, or credit default listing until at least 31 July 2020 and potentially beyond
• Minimising the frequency and duration of planned outages for critical works, and providing as much notice as possible to assist households and businesses to manage during any outage
The Australian Energy Council (AEC) confirmed that energy retailers stand ready to provide scalable, accessible and tailored assistance to all affected customers.
AEC Chief Executive, Sarah McNamara, also welcomed the AER’s recognition that the viability of energy businesses must be protected. Retailers often cannot control costs from other parts of the energy supply chain, such as wholesale power prices and distribution costs, that are charged to customers.
“For that reason, over the coming months, a whole-of-sector response is vital to achieve the best outcomes for customers. We look forward to working with the AER and other market bodies, governments and stakeholders on the best ways to share the risks and costs across the sector, and work through these expectations,” Ms McNamara said.
Commenting on the release of the Statement of Expectations, Energy Networks Australia CEO, Andrew Dillon, said networks were working to assist customers.
“Networks continue to discuss with governments, regulators and retailers about the best ways to support customers through this difficult period,” Mr Dillon said.
“Energy networks understand many households are also facing challenging circumstances. With many customers now
working from home, networks are doing what they can to minimise the impact of planned outages for critical work and to keep them as short as possible.
“Safely keeping the lights on and the gas flowing for the months to come is critically important, and networks are continuing to undertake critical works to keep energy supplies safe and reliable.”
Mr Dillon was also quick to point out that the industry has been working for some time now to start to prepare for the challenges this crisis will continue to present for a number of months.
Together with ENA, Ms McNamara confirmed that their members have been working to maintain the safety of their people, the security of the energy system and to support customers who are experiencing difficult circumstances.
“Safety is always our top priority. Energy companies have undertaken a range of measures in response to this pandemic to ensure its workforce, assets and energy supply are protected,” Ms McNamara said.
“There continues to be industry-wide consultation on pandemic preparations and necessary responses, with AEMO in regular discussions with generators, network and transmission companies and gas companies.”
Pandemic response measures underway include:
• Ensuring essential supplies, including the stockpiling of fuel supplies
• Reviewing any scheduled plant or network outages for maintenance and assessing the need and potential for rescheduling
• Further restricting access to control rooms and limiting access to areas required by critical staff
• Splitting of teams and establishment of multiple, separate teams
COVID-19: utilities unite to respond to the crisis
ENERGY COMPANIES ARE WORKING TIRELESSLY TO MAINTAIN NETWORKS AND ENSURE CONTINUITY OF SUPPLY DURING THE COVID-19 CRISIS.
• Rostering changes
• Non-contact and social distancing for shift changes
• Implementing new working arrangements, including having staff work remotely when feasible
• Monitoring of essential service providers
• Maintenance of personal protective equipment stocks
The ENA also moved to remind customers that part of keeping the lights on and gas flowing during these uncertain times is continuing to carry out scheduled maintenance works across our networks. Many utilities have reported frustration from customers having their services shut down during this challenging period; however Mr Dillon reminded customers that “there is a need to continue critical maintenance to protect lives, prevent damage to properties and keep the power on for the future”.
In the upstream energy sector, the Australian Petroleum Production & Exploration Association (APPEA) and Australian Pipelines and Gas Association (APGA) are both working with members, governments and energy users to ensure the delivery of essential gas supply to local customers.
APPEA Chief Executive, Andrew McConville, and AGPA Chief Executive Officer, Steve Davies, confirmed members were taking all steps necessary to ensure the production and delivery of gas supplies continued.
Mr Davies said the upstream and pipeline industries had robust operational integrity measures in place at all times, but were vigilant to the additional challenges posed by COVID-19.
“We are ensuring good information flows and open channels of communication as they are absolutely essential elements of the response in this rapidly changing situation,” Mr Davies said.
“We are continuously monitoring the situation and are taking appropriate precautions to ensure the energy we need in our homes, commerce and industry is delivered.”
The country’s energy utilities have been quick to reassure customers that they have the necessary precautions in place to maintain supply while protecting the safety of employees and the community.
Common themes in the response from energy utilities have been strict isolation protocols; limits on face-to-face interactions where possible; additional cleaning of sites and workplaces; additional personal protective equipment for staff; telephone contact with customers before crews arrive; and phone notification of future outages, rather than face-toface.
Other measures include increased infection control measures, ceased business-related international travel and teleconferences rather than face-to-face meetings where possible.
Most companies have also established separate locations, backups and staffing in critical service areas like control rooms; and have limited access to, and contact between, those teams to sustain customer operations in the event a case is confirmed.
Power companies have also noted that while it is too early to see a significant change or shift in demand for power supply due to COVID-19, it is likely we could see energy demand in commercial or industrial areas decrease, but a peak load in residential areas – similar to what we experience on an average weekend.
Contingency plans are underway across the country too, which includes a strong focus on completing urgent tasks on the network to ensure it is as resilient as possible in the event
of weather or other events that could happen in conjunction with the challenges COVID-19 presents.
AGL CEO, Brett Redman, reassured customers that there will be help for those in need as Australians face difficult financial times due to the Coronavirus outbreak.
In a letter to more than two million customers, Mr Redman acknowledged there are “difficult times ahead” for the country and urged any AGL customer experiencing difficulties paying their bill to get in touch.
“During the evolving COVID-19 pandemic, we want to reassure you that we are committed to supporting our people, customers and the community.”
EnergyAustralia has also reaffirmed its commitment to customers doing it tough during the Coronavirus pandemic in Australia.
Chief Customer Officer, Mark Collette, said that EnergyAustralia is already helping customers through this difficult period – but customers need a whole-ofindustry response.
“The COVID-19 situation is unlike anything we have seen or experienced before. We support the call by the AER for a whole-of-industry response to help households and businesses nation-wide get through this challenging time,” Mr Collette said.
“The AER has highlighted the need for network companies to support energy customers by waiving fees and extending payment terms; retailers alone cannot deliver what is needed to support customers.
“Our message to EnergyAustralia customers is this: If you're worried about not being able to pay your energy bill, reach out to us.”
Origin Energy has also reassured its customers that help is available for anyone impacted by COVID-19, and that it continues to take action to ensure access to reliable energy supply is maintained throughout the pandemic.
Origin CEO, Frank Calabria, said, “This is an unprecedented situation and we are focused on protecting the health and safety of our people and the communities in which we operate, while maintaining safe and reliable operations.
“We encourage any customers who are having trouble paying their bills to request a payment extension through our website or call us to discuss other types of support available.
“As a provider of an essential service, we plan extensively for these sorts of events and I’m proud of how our teams have responded and coordinated with industry to maintain reliable supply of power, natural gas and LPG to our millions of customers across the country.”
Leading energy infrastructure company Jemena has also taken significant steps to ensure the lights stay on and gas continues to flow to its more than 1.7 million customers during the COVID-19 pandemic.
“This is a dynamic and evolving scenario, and we have enacted our crisis management and pandemic response plans in response to the COVID-19 outbreak so we are able to maintain our operations while ensuring the safety of the community and our people,” Jemena Managing Director, Frank Tudor, said.
“At the same time, we are looking with a critical eye at our normal operating arrangements, so we can move beyond our standard approach to responding to hardship, noting the
extraordinary circumstances facing many Australian households and businesses.”
In the water industry, it’s a similar story as members of the industry come together to develop and provide a coordinated response to the crisis.
“Water utilities supply the most essential of essential services to our communities,” Adam Lovell, Executive Director of the Water Services Association of Australia (WSAA), said.
“Our drinking water remains high quality and safe to drink. In these unprecedented and challenging times, the industry is taking actions to ensure the continued safe supply of high-quality water and wastewater services in Australia and New Zealand.
“WSAA has held online meetings of its Customer and Leadership Committee and Utility Excellence Committee, which allowed members of the industry to discuss and share current actions in relation to COVID-19.”
Water utilities have been quick to assure customers their priority is delivering reliable water and sewerage services, and ensuring the safety and wellbeing of water industry employees.
Water authorities are establishing dedicated teams focused on the COVID-19 response, implementing measures to minimise risks to staff, and liaising with key government agencies on a daily basis to monitor and understand the health impact of COVID-19 as it develops.
Water utilities have also moved to shut down any public payment and processing facilities; and many have issued requests to customers to not approach staff in the midst of this crisis, to protect essential service workers as much as possible.
Unitywater Executive Manager Customer Delivery, Rhett Duncan, said, “We’re asking everyone to give us space so that our crews can do their job for the benefit of the broader community.
“Our crews work tirelessly to keep the water on for you. If our crews are in your street or your property is affected by our works, please phone us or visit our website rather than approaching them. They will keep their distance from you and we ask you to do the same.”
Other common measures being implemented by water utilities include:
• Activating pandemic response teams and business continuity plans
• Promoting and enforcing good hand hygiene practices
• Implementing mandatory social distancing measures
• Implementing work from home arrangements where possible, and isolating critical networks staff and teams to ensure the ongoing operation of water and wastewater networks
• Putting a stop to non-essential international and domestic travel
• Assessing customer hardship programs and developing a coordinated response for customers unable to pay their water bills.
Water utilities have also had to contend with increased wastewater network blockages, as users flush products outside of the “three P’s” down their toilets.
UTILITIES HAVE REQUESTED THAT CUSTOMERS DO NOT APPROACH CREWS WORKING ON NETWORKS DURING THE CRISIS.
Queensland Urban Utilities (QUU) RTL Trades General Manager, Mick Bradley, said the number of blocked drains his crews had attended to had skyrocketed since the toilet paper shortages.
“Usually we’re called out to around seven blockages a week, but at the moment we’re dealing with more than 20 a week,” he said.
“The majority of blocked drains are caused by people flushing wipes down the toilet and the costs can run into the thousands.”
SA Water’s General Manager of Customers, Strategy and Innovation, Anna Jackson, said SA Water is dealing with the same challenge.
“In the current situation we’re all in, we understand people are trying to conserve their toilet paper use and are perhaps starting to use another household item to clean up,” Ms Jackson said.
“Unfortunately, flushing things like tissues, paper towel, wet wipes or newspaper down the toilet can lead to problems for both you and our crews, because unlike toilet paper, which is deliberately designed to break down in around 30 seconds, these other items don’t disintegrate in the sewer system.
“Keeping the sewers healthy is a shared responsibility, so we’ll keep doing our part through ongoing sewer main cleaning and replacement programs, and using various technology to inspect the pipes and help predict where a fault may occur before it can impact the community.”
The telecommunications sector has also faced its own challenges in response to COVID-19, with significant growth in usage as customers driven indoors turn to streaming services, and the massive influx in home usage from employees working from home.
nbn co’s team of data scientists and network engineers have been studying data consumption patterns in other countries that have been significantly impacted by the pandemic in recent weeks. At the same time, the company’s engineering teams have been planning for, and strengthening the network to help meet residential data demand that will likely surge, based on overseas examples, at different times of the day and night.
nbn co is well-advanced with its contingency plans and will
incrementally increase its data capacity allocation to retailers to accommodate the expected growth in residential data demand. It is requesting that retailers place their forward orders for capacity in the normal way, and nbn co will increase capacity as required to meet demand.
The company is also planning to limit non-essential maintenance to minimise scheduled, planned outages in the weeks ahead to maintain network availability as much as possible.
nbn co Chief Executive Officer, Stephen Rue, said, “The NBN is part of Australia’s critical infrastructure, and the role of the network has never been more important than now and what we see unfolding over the weeks ahead. For many Australians, the NBN and other broadband and mobile networks will become the primary channel for work, study, entertainment, ordering food and maintaining contact with the outside world.
“As a telecommunications industry, we will work together to keep Australians connected and productive through this crisis. These are unprecedented times and we are already seeing a steady increase in demand on the NBN, and this is set to continue. In terms of the expected requests for additional capacity, we will work with the industry to find the best solution. Clearly we all need to play our part.
“We are in the fortunate position that more than 90 per cent of the national broadband network rollout has been delivered across the country, so the vast majority of Australians already have access to fast, reliable, secure broadband, which will serve them should they need or want to spend more time at home.”
Like all industries in Australia, utilities are grappling with a rapidly changing situation, with every day presenting different challenges to the day before.
The work already undertaken across our essential service industries has been exemplary and is something the industry should be incredibly proud of.
We wish all of our utility colleagues and stakeholders all the very best in the coming months as we continue to manage the impacts of this crisis.
50Hz to 480kHz Frequency Range
Large High-Contrast LCD Interface
Lightweight & Ergonomic
GPS & Data Logger Compatible
Remote Link Between TX & RX
84wH Lithium-Ion Batteries
12 Watts of Output Power
Constant Depth & Current
8 Locating Modes
www.rycominstruments.com
The COVID-19 pandemic has resulted in state-wide lockdowns, mass event cancellations and the closure of workplaces, as social distancing measures become key to slowing the spread of the disease. Despite the restrictions on travel and in-person meetings, the Digital Utilities event was able to connect utility leaders across the country by moving quickly to deliver a successful digital conference.
Hosting an event can be challenging at the best of times, and a global pandemic is an unprecedented situation for most event organisers. With the Coronavirus situation changing far more rapidly than anyone could have anticipated, on Friday 13 March it became clear that Digital Utilities 2020 could and should not go ahead as a live event.
In only three business days, the entire conference program was transferred to an online format, ensuring the safety of attendees by removing the need to travel and meet face-to-face in large numbers.
In the utility industry, embracing digital technologies and business models is vital for optimising asset management, improving network operations and keeping up with changing customer demands – as video conferencing and remote working becomes the new normal, Digital Utilities was able to create something of value for all participants and ensure conversations around the highly relevant topic of digital transformation could still take place.
From 19-20 March, over 130 delegates tuned in to watch the Zoom webinar live, with many others intending to watch the presentation recordings at their leisure. A lot of valuable information was exchanged and there was plenty of social interaction through the in-built Q&A and chat functions.
The support for the digital conference from speakers, sponsors, exhibitors and delegates was overwhelming, with many commenting how glad they were that the event still went ahead, with the majority of industry gatherings cancelled or postponed for the foreseeable future.
Bentley Systems – a global software development company with a portfolio of solutions that accelerate project delivery and improve asset performance –maintained its role as the Event Partner for a third year running, kicking off day one of the webinar with an informative presentation about digital twins.
John Da Mina, Regional Director ANZ at Bentley Systems, discussed the applications of digital twins for utilities, offering practical advice on how the technology’s immersive visualisation and analytics visibility can help achieve a deeper understanding of utility infrastructure assets.
In his presentation Using technology to highlight the risks overhead, Aaron Smith, HSE Business Partner & Community Safety Manager at Energy Queensland, discussed the lifesaving tool developed by the utility to improve safety around powerlines.
“Lookupandlive.com.au is an online mapping application that pinpoints the location of 178,000km of overhead powerlines and 1.7 million poles across Queensland,” Mr Smith said.
“At Energy Queensland, a team of community safety specialists has been collecting statistics on accidental powerline contacts for over ten years to better understand why these incidents are occurring and how they could be prevented. From the outcomes of the investigations a clear issue stands out – a distinct lack of planning and powerline awareness.
“The team has fostered a positive and proactive association within the community by building awareness of the dangers of accidental contact with powerlines. The Look Up and Live tool is an extension of this
Event Partner
Major Sponsors
Sponsors
and enables behaviour change by helping workers to adequately plan work and put effective controls in place, assisting businesses to keep their workers safe and be legislatively compliant.”
Natasha Ogonowski, Water Sensitive Cities Program Manager at Water Corporation, and Peter Condon, Data Science Team Leader at Western Power, both shared case studies that demonstrated the practical applications of digital technologies in real-world situations as part of the conference’s Technical Session.
Ms Ogonowski took delegates through Water Corporation’s H2OME study, which utilises the most advanced technology available to determine how much water Perth should be using to preserve the liveability, amenity and quality of life of its community.
“H2OME is a one-year mixed methods study followed by a four-year longitudinal study that will give Water Corporation the insights it needs to help secure our water future,” Ms Ogonowski said.
“The study of 2,500 households combines digital metering data with household data on fixtures, fittings and appliance efficiency, attitudes, demographics, billing, marketing and communications with big data sets comprising weather, spatial land and CSIRO photogrammetry data to understand the drivers of water use.”
Mr Condon explained how Western Power is improving operational response to incidents by embedding automated forecasts from its Short Term Operational Response Model (STORM) inside scheduling and dispatch processes,
resulting in faster response times, shorter outage duration and more efficient spending.
“By blending traditional engineering knowledge with geomorphological analysis and state-of-the-art machine learning, STORM forecasts more incident categories with higher spatial and temporal accuracy than was previously possible,” Mr Condon said.
Digital twins proved to be the hot topic for 2020, with AVEVA’s Strategic Account Manager – Water, Paul Banfield, delving into the major hurdles to success for utilities looking to implement the technology.
“The digital twin can predict the potential failures of its physical counterpart well before they happen and can suggest ways to prevent those failures – but there is a potential flaw,” Mr Banfield said.
“The digital twin can only be as good as the detailed data that it is built on, combined with the real-time data it gathers. It also requires accurate contextual information and real-life understanding of the system, area, units and rooms in which it exists. Only then can the twin represent the true ‘as-operated’ state that the business can trust.”
Matt Rennie, Oceania Power and Utilities Leader at EY, rounded off day one of the event with a forward-thinking presentation titled Not a time for perfection, exploring the challenges and opportunities present in the energy transition. Mr Rennie also highlighted the lack of action taken to make Australia the global vanguard of new energy, despite its abundance of natural resources.
“Voltaire once wrote that ‘perfection is the enemy of good’ – Australian energy policy has had neither. Over the past 15 years, as the early embers of technological and customer-driven change began to simmer through the industry, energy policy in Australia has veered from the reactive to the counterproductive,” Mr Rennie said.
“Time has now shifted against us, and Australia finds itself lined up as one of the first global countries to experience the energy transition, with grid parity for batteries expected in 2021 and EV/combustion engine parity in 2024.
“This is a time of challenge for our regulators and policymakers, which stand at the cusp of a maturity curve like never before. New funding compacts, new branches of cooperation and new approaches to attracting and retaining human capital are required. Will they meet the challenge? The energy transition depends on it.”
Lucia Cade, Chair at South East Water, commenced day two proceedings with her domestic keynote presentation
Digital transformation: the boardroom perspective
“Technology plays a vital role in enabling South East Water to bring value to its customers and community, so we are always thinking ahead and implementing new digital solutions in our network to help create a better world for our customers,” Ms Cade said.
Ms Cade focused on how South East Water is harnessing and inventing digital technologies to stay ahead of challenges like climate change and population growth to make its customers’ experience better and to provide fair and affordable services – all while minimising its impact on the environment.
This was followed by a panel discussion featuring Katherine Gee, Executive Manager of Customer and Community at Unitywater; Matt Grantham, Head of Strategy and Business Development at Billcap; Neil Horrocks, Director at the University of Queensland’s Centre for Energy Data Innovation; and Aaron Everingham, Country Manager Australia and New Zealand at Quadient.
This panel looked at the impact of digital transformation on people, exploring how utilities can create a digital culture and use data analytics to enhance service quality, lower costs, and preserve and deepen customer relationships.
This was followed by an individual presentation, Situational awareness and the operational twin, from Zoltan Borbas, Industry Consultant at Hexagon PPM, who discussed how utilities could transform unstructured information into a smart digital asset to visualise, build and manage structures and facilities of all complexities, ensuring safe and efficient operation throughout the entire lifecycle.
“Fusing the real world with the digital world is at our core,” Mr Borbas said.
Delegates also heard from Angela Lam, Manager Information Technology at Horizon Power; Paul Siemers, Manager – Digital Strategy, Architecture and Innovation, Information Technology at Melbourne Water; Michael Joffe, Energy and Utilities Industry Lead at Publicis Sapient Australia; Mark McCormack, Group Manager Digital Utility Program at South East Water; and Tyson Hackwood, Head of Growth at Monoova as part of a panel discussion focused on processes.
This panel explored how utilities can transition from legacy systems and manual operations to more streamlined digital processes, and the convergence of IT and OT as a critical component of digital transformation.
In her presentation, Your digital twin: what could possibly go wrong?, Anna Murray, Senior Account Director, Engineering, Construction and Infrastructure at IFS Australia, explained that the key to the success of your digital twin is to make sure that your processes are data driven rather than document driven.
“You don’t want all that hard won, critical asset data to sit in yet another silo of dark data. Structured asset information needs to flow directly into the systems used to build and manage it,” Ms Murray said.
“Without integrating your digital twins into existing enterprise solutions and processes, these transformational technologies will create data silos unto themselves and the organisation will struggle to achieve asset management efficiencies.”
Justin Parr-Davies, Partner & APJ Head of OT & IoT Security, Cybersecurity & Risk Services at Wipro then went on to talk about why a unified approach to IT and OT cybersecurity is critical to achieving cyber resilience in utilities as they take up the challenge of Industry 4.0.
“Industry 4.0 digital transformation programs require consideration of the digital processes, systems, machinery and objects that could be impacted with the convergence of IT, OT and IoT,” Mr Parr-Davies said.
“Industry 4.0 provides one of the greatest increases in cyber risk to business over the last 50 years and will directly impact utilities and other areas of critical infrastructure.”
The event ended with a session from independent technology consultancy, Isle Utilities, who went beyond the buzzwords to explore the real impact and strategic implementation of digital technologies. Delegates had the opportunity to meet a range of innovators and learn how emerging technologies can provide practical value to utility organisations.
The featured technologies included:
• Kieran Mackenzie, Founder/Chief Executive Officer at Presien, demonstrated Toolbox Spotter, an artificial intelligence computer vision system optimised for heavy industries
• Glyn Addicott, Operations Director at Hydraulic Analysis Group Limited, demonstrated VariSim, a dynamic, real-time pressure transient simulator for water networks
• Chad Moulden, Commercial Lead (Australia) at Open Energi, demonstrated Dynamic Demand 2.0, demandside response technology that reduces the cost of delivering and consuming power
• Matt Smith, Chief Executive Officer at MyPass Global, demonstrated MyPass, a digital workforce management platform that connects all of industry –workers, training organisations, service providers and end users
Major Sponsors, GHD Digital and DXC Technology, and Sponsors, BidEnergy and Amazon Web Services, are also helping accelerate digital transformation in the utility industry through their innovative product and service offerings.
Digital communications, video conferencing and remote working have fast become the new normal, and the two-day digital conference is just the beginning for Digital Utilities 2020
There will be a live Digital Utilities event later in the year once circumstances allow, where the winners of the 2020 Digital Utility Awards will be announced and celebrated.
Unfortunately, several speakers were not able to take part in the online conference because of the COVID-19 crisis – either due to illness or their involvement in coordinating emergency responses to ensure the delivery of essential services to all Australians.
These speakers will have the opportunity to participate in the live event so delegates can still benefit from their insights.
All delegates and supporters have also received an invitation to an exclusive online networking group, which will work actively to facilitate social networking between utility professionals until they can meet in the real world again.
This will help create a Digital Utilities community that will extend beyond the event and open up real communication possibilities in a more digitised world.
As Victoria experiences a rise in climate emergencies, population growth and threats to food security, it’s now more important than ever for the rural and urban water sectors to work together, says Cameron FitzGerald, Managing Director of Southern Rural Water.
Operating across 88,000km² of southern Victoria – a landmass greater than Ireland – Southern Rural Water services the needs of diverse customers via the regulation of access to surface water, groundwater and management of irrigation districts.
The utility’s operations support food and fibre production, contributing more than $14.2 billion to the Victorian economy each year. Its operations also power generators critical to the electricity grid operating across Australia’s southeastern seaboard, as well as providing raw water to a number of urban water authorities who transform this water into highquality drinking water for metropolitan customers.
According to Mr FitzGerald, excellence in water management requires a whole-of-sector approach, where the urban and rural sectors identify opportunities to learn and grow from each other.
“Drawing on my fifteen years’ experience in the urban sector, I see opportunities for the two parts of this industry to work better together,” Mr FitzGerald said.
“Drought response and climate emergencies are a significant part of this. How we manage irrigation water and how urban utilities manage water for cities and towns are fundamentally interlinked.
“When impacts of climate change take their toll, all communities face challenges in how they deliver water.
“Rather than making these challenges either rural or urban issues, we must shift our thinking and look to solve problems holistically.”
According to Mr FitzGerald, the urban and rural landscapes are not only linked through physical pipes and assets, but through customer expectations and the provision of services.
“From the CBD to the furthest tips of the state, customers want the same things. They want their utility to be easy to deal with and to demonstrate value for money,” Mr FitzGerald said.
“They want to know that the rules that apply to them are applied fairly to others, and that the rules won’t be changed without effective consultation.
“Most importantly, all customers require dependable water services that ensure the water gets to where it is needed, when it is needed.”
The impacts of climate change don’t discriminate. Whether a region is faced with increased average temperatures, low rainfall or flooding, the management of both rural and urban water is put to the test.
“We don’t need to look too far to see the impact that climate change is having on our customers. Last year, the Glenmaggie Weir failed to spill for the second year in a row – the first time this has happened in four decades,” Mr FitzGerald said.
“If there is less water, we as an industry have to get better at identifying opportunities to work together and to efficiently deliver the water we have.”
According to Mr FitzGerald, the water industry’s response to the current bushfire emergency is a strong example of what can be made possible when the sector works together.
“I was really pleased to see the industry stepping up to support the bushfire emergency and recovery efforts,” Mr FitzGerald said.
“At Southern Rural Water, our teams came together to assist in delivering critical water to livestock. We did this by opening up emergency supply points for farmers that took the pressure off main supplies.
“By doing this, we were able to meet an important community need while also supporting East Gippsland Water’s systems.
“It was a small contribution in terms of the overall response, but it demonstrates what can be achieved when our colleagues and the industry work as one.”
Southern Rural Water currently assists with climate emergencies, providing real-time information to the Bureau of Meteorology on local flood conditions, as well as using new technologies to enhance the value of the data it provides.
“The use of remote sensors and big data offers us all the opportunity to build better models and enhance the value we create not just for the Bureau, but for all stakeholders,” Mr FitzGerald said.
“Additionally, our ability to use the Bureau’s data analysis to drive our own decisions during climate emergencies will be critical to a successful emergency response.”
Southern Rural Water is looking to the future to plan how it can manage its assets, focusing on resilience in the long term for customers and communities.
“Over recent years, we’ve committed to an extensive modernisation program, ensuring the districts across our network are more efficient, reliable and resilient to a drier climate,” Mr FitzGerald said.
“For example, the Macalister Irrigation District, the largest irrigation district in southern Victoria, is undergoing an upgrade consisting of pipelining, channel automation and regulator upgrades.
“More than $92 million in works have been completed to provide 22,000 megalitres of water savings for irrigation use within the district.
“Investments of $30 million and $12.3 million into the Werribee and Bacchus Marsh Irrigation Districts have also been made to complete piping and modernisation.”
Mr FitzGerald knows that building a passionate, knowledgeable team and high-performing culture is vital in supporting collaboration across the sector.
“Southern Rural Water’s people bring our vision to life, and I believe that our success comes from being able to pool our wide range of expertise to collaborate and solve common problems,” Mr FitzGerald said.
“Great practices inside one irrigation district, for example, can be transferred to deliver better outcomes in others, and it’s really important to recognise and share these synergies.”
In recent months, Southern Rural Water’s senior leaders have also been involved in a significant leadership program focusing on self-awareness and equipping participants with individualised coaching to assist them on their leadership journey.
“With such a large area to manage, leading an inspired team spread across the state can be a challenge,” Mr FitzGerald said.
“There is no right way to build a great culture, but it does start with self-awareness and meeting people where they are on their journey, then encouraging them to explore their potential.
“As leaders, we must remember that it’s our people who are the ones delivering value to our customers. They are in the field installing, developing and managing our assets, and it’s critical that we are equipping them to thrive.”
The science, technology, engineering and mathematics (STEM) space is constantly evolving with the development of new systems, technology and practices, as well as an increasing ratio of women in the workplace. With this evolution set to impact the next generation of STEM professionals, it’s more important than ever for companies in the STEM space to partner with organisations and education providers to train, educate and inspire future professionals.
Aholistic approach to investing in future STEM professionals happens at all levels, from primary school students right through to university level and beyond. Pipeline repair, restoration and renewal provider, Interflow, is one of the companies leading the way when it comes to creating opportunities for young, innovative minds.
Saadia Ali, a Project Manager at Interflow in New Zealand, can trace her love of STEM back to her childhood. A love of building things, along with a flair for maths and physics, led her into engineering studies at university and on to a successful career in STEM.
Interflow is working alongside Engineering New Zealand on initiatives such as the Wonder Project, which is a free program for schools designed to get more young students excited about STEM subjects. For Ms Ali, this is an opportunity to pass on her passion for engineering.
“I spend an hour a week in a classroom at a local school. They take soda bottles and build rockets out of them – they learn the concepts of physics and what will make their rockets fly well and what will make them fail,” Ms Ali said.
“It’s about getting kids excited about things that might seem nerdy or not cool to do at school.”
While the majority of STEM roles are still filled by men, initiatives like this are paving the way for a greater number of young women to pursue STEM careers.
“Part of the Wonder Project’s aim is to get kids excited who need a push from female ambassadors. There’s a definite push for those young females who are coming through school to know that they can do it if they’re female, it’s not just a boys’ club,” Ms Ali said.
To provide budding STEM professionals with these basic skills and opportunities, Interflow has partnered with university students to offer mentoring and paid internships, many of which lead to permanent work.
One of the reasons this is so important is because Interflow
operates in a specialist area of civilised engineering where knowledge is not widespread. John Monro, Technical Support Officer at Interflow, said that because the area of trenchless technology is not taught in STEM degree courses, specific teaching and training must be developed by practitioners.
“Undergraduate STEM interns arriving at Interflow require training in both the industry and the specifics of Interflow’s practices – training which is not available externally,” Mr Monro said.
“They are also exposed to technologies and concepts that are an extension of those encountered in their studies, exploring the potential for thinking beyond merely applying known formulae and standard methods. The skills they can develop can be beneficially applied in whatever STEM-related career path they ultimately follow.”
The Interflow internships started through an association with the University of Technology Sydney (UTS) which runs a five-year engineering course requiring a junior and senior internship.
With practical support and training from Interflow, Keith Gover, a Human Relations Business Partner at Interflow, said he has watched many interns develop into graduate engineers and later into project engineers.
“We support the students and they help build our organisation. It’s a win-win,” he said.
While many companies offer unpaid internships, Interflow has mandated that all interns be paid to give them a real working experience. Mr Gover said that this changes the relationship to a typical employee and employer relationship rather than simply doing students a favour.
“We’re not looking to take advantage of students who want to get ahead, so we offer paid internships in Melbourne and Sydney – with plans to extend the opportunity for internships in other office locations as the business grows – and that’s really increasing our support of the next generation of STEM professionals,” Mr Gover said.
“I’m really proud of the people who have worked their way up the company after coming to us as interns, and for the contribution they’ve made to Interflow.”
Moncrieff's Winery contacted FILTEC for an advance water filtration system to improve its water quality for the entire wine-making process – clean water is critical for the winery to obtain the Organic Wines Certification.
The winery sourced water from the local river, then filtered it through a treatment system that consisted of bag filtration with UV disinfection. During the long, hot summer season, organic concentration in the river increased by at least double, and the existing UV system did not perform well.
Understanding Moncrieff’s issue, FILTEC worked closely with the winery to come up with a solution. Having more than ten years’ experience with the local river water and fluctuations in raw water quality, FILTEC designed a robust filtration system with membrane technology to handle high turbidity (max 200NTU).
The design consisted of two ultra filtration system trains with polypropylene (PP) modules as an alternative to the standard polyvinyl difluoride (PvDF) module. As most wineries ban chlorine in their water, using PP modules reduced the cost for the customer.
The water treatment process includes disc filtration, ultrafiltration and UV disinfection. FILTEC was involved in all aspects of the project, including minor civil works (i.e. concrete pad, shed), process design, equipment supply, installation, commissioning, training and ongoing service.
The new treatment system produces water quality that meets Australian Drinking Water Guidelines, meaning that Moncrieff can now reapply for the Organic Wines Certification.
FILTEC has worked with many wineries across Victoria to solve their water treatment needs, including Buller Wines. If
Steel Mains is proud to be Australia’s largest manufacturer of Mild Steel pipes for the water industry. We continue to manufacture Sintakote® Steel pipe with manufacturing facilities located in both Victoria and Western Australia. Materials and labour required to manufacture our pipes are sourced locally, ensuring our pipes enjoy greater than 98% local content.
Local stock, delivery and design & installation support mean that Steel Mains is able to reduce all your pipeline supply risks. Local manufacture and product Standardsmark certification provide you with that additional supply security, with all aspects of our manufacturing meeting Australian quality standards. When the lifespan and security of your asset are important to you, Steel Mains Sintakote pipeline systems are your ideal choice for your next pipeline project.
Melbourne Water has partnered with waste and water resource management company SUEZ in an innovative project to optimise and automate distribution throughout its drinking water supply network and reduce its overall energy consumption.
SUEZ was awarded the contract to implement its proven Aquadvanced® Energy solution across the drinking water network, which supplies residents with over 400 billion litres of water each year. The real-time optimisation software automates scheduling of production and management of distribution throughout every stage, ensuring high-quality water is delivered when and where it is needed at the lowest possible cost.
Aquadvanced® Energy has been successfully deployed across numerous networks in the US and Europe, and is being adopted across Hunter Water’s networks on the New South Wales Central Coast following highly effective trials in 2018. The system is proven to reduce energy costs while maximising operational performance, water quality and energy efficiency for an enhanced environmental footprint.
Evan Atkinson, General Manager at SUEZ Smart Solutions, said the implementation will be rolled out in three phases over two years, due for completion by mid-2021.
“Our Aquadvanced® Energy solution is a proven solution that remains at the leading edge of innovation in water sustainability and smart networks. We’re seeing incredible results applying this solution in diverse networks both overseas and here in Australia, generating network efficiencies and cost savings,” Mr Atkinson said.
“Our objective is to drive increased network resilience, reduce likelihood of water quality events and greater operational consistency for Melbourne Water and the city’s residents. Embedding this technology will also enable the network to further leverage its hydro generation assets and exploit opportunities in the evolving energy market.”
The project is expected to realise significant energy and cost savings for Melbourne Water, and will help futureproof its workforce through the capture and retention of network knowledge.
Melbourne Water Automation Team Leader, Russell Riding, said that the move to automation of its water network is a fundamental step towards achieving the company’s ambitious targets.
“Melbourne Water is committed to reducing our carbon emissions and our energy consumption, which ultimately will provide value for our customers. The implementation of Aquadvanced® Energy supports the digital transformation of our network,” Mr Riding said.
“Melbourne Water is always exploring new and innovative solutions to deliver sustainable water services.”
The first phase of the project will see Aquadvanced® Energy implemented on the Winneke Water Treatment Plant supply system leading to the Melbourne CBD before subsequent extension across the remainder of Melbourne Water’s network. Find
With the drought, bushfires & Covid-19, some important lessons have been learnt. To value the essentials of life & to look after each other most of all.
As an essential service, water to all communities might now be universally accepted. Such infrastructure can include Abberfield Technology’s pre-paid water dispensing stations
Another essential is rebuilding the economy, which means creating employment & supporting Australian companies, keeping the earned income in Australia. Abberfield Technology is wholly Australian owned, producing world leading-edge technology, developed here in Australia, for Australian conditions.
At the time of print, the Abberfield factory in Sydney is taking over an adjoining property, doubling productive space, so staff can work in total isolation & production can be maintained.
Then, with a converted RV as a mobile office/workshop & complete with a delivery trailer in tow, Abberfield can travel anywhere at any time. Abberfield are recognised as an Essential Service Provider & in very recent times have travelled to Queensland, Victoria & outback New South Wales. This is done in total isolation as the
van, designed for the purpose, is fully selfsufficient & fitted with long range fuel tanks.
Social distancing is maintained by the engineering team operating from home & using internet conferencing, which allows Abberfield to continue meeting even more challenging applications. Selling water was no longer sufficient and controlling the sale of water became essential. This is now done in many ways, such as pre-registration of credit cards, pricing for different categories of customers & limiting volumes per delivery, or per week & much more.
Previously, only potable water was dispensed, now raw water is controlled, for road work, cattle watering & horticultural use. This can include the control of pumps & these pumps can now be fitted within the Abberfield Filling Station, or installed remotely (bore pumps etc.), yet can still be controlled by the Filing Station’s electronics.
Smaller Filling Stations are also being designed for Recreation Vehicle filling in garages, Information Centres & caravan parks. Also, a compact rugged version is for irrigation purposes, raw water delivered farm to farm & automatically paid for by an Abberfield control system.
Financing this infrastructure in depressed economic times has required a considerable capital injection, being a measure of the shareholders commitment to the business & community. Shareholders know how tough it has been for rural communities; they see it in their travels & experienced it when having to abandon their own decades old weekend vineyard.
Altruistic? Perhaps, but also economically sound, in the knowledge that Councils, Water Authorities & Government must invest in water security & in economic re-development.
REALIGNING ATTITUDES HOW POWER AND WATER’S PROACTIVE APPROACH IS HELPING WATER SOURCES GO FURTHER
A focus on changing attitudes towards water has enabled the Northern Territory’s Power and Water Corporation to prolong the life of precious water sources.
Power and Water, the Territory’s multi-utility, has about 51,000 water customers spread across an area spanning 1.3 million square kilometres.
Most water sources are isolated, with around 90 different sources for 92 communities, including the major urban centres of Darwin, Katherine, Alice Springs and Tennant Creek.
With customers located in some of the most remote parts of the country and facing unique water challenges, Power and Water rolled out its Living Water Smart program in 2013.
“Whether you’re in Katherine or Kaltukatjara, water is socially and culturally central to everything,” Living Water Smart Program Manager, Jethro Laidlaw, said.
“We’re trying to get people to change the way they think and act when it comes to water, giving them a sense of custodianship and responsibility.”
Territorians are Australia’s highest water users, with more than 60 per cent of household water use in the garden.
“We didn’t have the millennium drought in the Territory, so locals weren’t subject to the behaviour-changing water saving programs and restrictions those in other states were,” Mr Laidlaw said.
“The Top End normally has a monsoon topping up Darwin’s water supply, adding to the perception we have unlimited water.
“There’s a disconnect between valuing water as a concept and valuing what’s coming out of the tap.”
Living Water Smart is run in Darwin, where households regularly record the highest water use for any capital city in the country, and in Katherine, where per- and poly-fluoroalkyl substance (PFAS) contamination in groundwater has restricted available supply.
Demand management programs are also gaining momentum in remote Aboriginal communities with limited water supply.
The rollout of Living Water Smart, which followed a similar program in Alice Springs, cemented the utility’s broader, decade-long approach to water management.
This slant has worked well in the Territory, where funds spent on drilling programs in remote communities do not necessarily yield results.
“Traditionally the water industry has focused on increasing supply instead of managing demand, but demand management works,” Mr Laidlaw said.
“We spend less on reducing demand. It prolongs the life of water sources by years and helps customers develop an understanding of the value of water.
“We’ve also seen digital metering and leak detection technology improve significantly, which has helped us detect and fix leaks within our own network.”
In his time at Power and Water, Mr Laidlaw has seen a range of attitudes to water use, from very conservative to households running sprinklers on their roof 24/7 to cool their dwellings.
“People don’t really think about what it takes to extract water from the ground, treat it and get it to their taps,” he said.
It is this disconnect that the Living Water Smart program aims to address.
News broke of Katherine’s bore water testing positive for PFAS in 2017, linked to firefighting foam used at the nearby Tindal RAAF base.
The town of around 10,000 was subject to compulsory water-saving measures, including only watering their lawns three days a week.
These measures limited the amount of contaminated bore water used to ten per cent – the maximum amount that can be treated each day to remove PFAS – to supplement the supply from the Katherine River.
With Katherine’s per capita water use more than double the national average, Power and Water needed to work quickly and closely with the community to educate, inform and engage them on their water use.
Living Water Smart scored some significant wins in that time, most notably reducing peak day water use by more than 33 per cent and overall water use by 20 per cent.
“Compulsory measures started in August, the peak demand period,” Mr Laidlaw said.
“Behaviour change generally takes time, but we needed the reduction in use straight away.
“During peak demand, the town used 16 million litres a day, and we needed to bring that down to a maximum of 11 million litres.
“We rolled out every measure we could think of, including rebates, checking for customer and network leaks, using
water loggers, and auditing and engaging with high water users.”
It was a move that paid off as the whole community rallied together.
“We had the mayor and local water-saving champions on board and used our digital communication channels heavily,” Mr Laidlaw said.
“At one stage, we had 15 per cent of the community on our website in a month, which was phenomenal.”
Despite community anxiety, Power and Water’s biannual customer satisfaction survey score index improved during the response period.
Presently, an interim PFAS water treatment plant uses Ion Exchange (IEX) resin to remove PFAS from one million litres of groundwater a day.
The treated bore water is then blended with river water after going through the normal disinfection process.
A longer-term solution is underway, with Power and Water working with the Federal Department of Defence to construct a permanent PFAS treatment plant.
The new plant, which will treat an additional ten million litres per day, is expected to be commissioned by the end of 2020.
The remote water space brings additional challenges. Among some of the considerations include huge distances, seasonal rainfall, unpredictable groundwater recharge, high water use amid extreme temperatures, high groundwater mineral content and hard-to-study isolated supply aquifers.
Despite and because of these challenges, Mr Laidlaw and his team of six have a heightened awareness of the importance of water in communities.
“Our work is essential to helping keep culture alive and strong in communities,” he said.
“We have an amazing culture more than 60,000 years old in our patch and we are lucky to help these customers live on country.”
Demand management strategies are carefully considered for each community and their respective water issues.
“A remote community can be on an island, by the seashore or in the middle of the desert. Residents speak many different languages and cultures vary considerably,” he said.
“Many communities are at risk of unsustainable water use. This is where we focus our resources and strategies.
“For communities less at risk, we carry out our school education program, 'That’s My Water!', to help promote a better understanding of where water comes from and what’s involved in taking it from source to tap.”
A coup for 2020 was getting the Territory’s own superstar rapper and 2019 Young Australian of the Year Baker Boy to feature in a series of videos for school children in remote communities.
The videos introduce traditional water stories from the Darwin, Katherine and Alice Springs regions and encourage children to think about how they can look after their water.
Other strategies that work well in remote communities include one-on-one conversations about water use and sponsoring local football games with advertisements in language on water conservation.
“We’ve introduced signboards in communities similar to the fire danger ratings in southern states, which indicate where water use is at,” Mr Laidlaw said.
“The kids change the signs, which are usually outside the store or school. It helps give people an idea of how they’re tracking.”
With a range of tools to deliver water saving messages and numerous locations to visit, the work is diverse and meaningful.
“One day, you could be sitting in the dirt with someone in 45°C heat, and a week later, launching a water saving initiative with government ministers,” Mr Laidlaw said.
“We’ve had some good wins along the way, with a few national and international awards. It just reinforces that what we’re doing is worthwhile and important.”
With the ever-increasing need to improve the efficiency and delivery of water services for customers, Programmed is driving smart solutions to assist water suppliers in achieving these goals. Programmed has steered this innovation in the water industry for over 25 years, through its client City West Water, where Programmed implemented the use of real-time data to deliver a more effective service.
Programmed, City West Water’s mechanical and electrical, and civil maintenance contractor – together with City West Water’s operations and maintenance teams – is using real-time data to dynamically schedule and divert crews and responders to optimise resource utilisation.
The use of real-time data has been in practice at City West Water for several years through its partnership with Programmed. Together with data analytics, Programmed has implemented a ‘First-Time Fix Rate’ initiative to correct faults on the first call out. This is possible by reading the data provided and assigning operators accordingly, allowing for minimal disruption and shorter response times to customers during maintenance activities.
But it is not only data that has brought about innovation. Programmed’s mechanical and electrical teams also have a fleet of ute-mounted cranes, which has helped in reducing manual handling. The cranes also reduce the need for traffic management, as they are positioned without blocking roadways or footpaths, leading to minimal disruption for customers.
These significant innovations around operations and maintenance, and Programmed’s continued pursuit of zero harm, has led to over 1,000 days with no Lost Time Injury (LTI). Programmed and City West Water are very proud of this milestone, and the holistic way Programmed proactively manages safety risks.
In response to the COVID-19 situation, Programmed has implemented a customer support crew to assist rectification
teams while out on the job. The support crew operates the main isolation valves, allowing repair teams to complete work at a faster rate and minimising the water outage timeframe.
Safe interactions with customers focused on answering questions and providing a temporary water supply highlights Programmed’s emphasis on supporting the community in this changing environment.
City West Water’s General Manager of Infrastructure and Delivery, Amanda Smith, said Programmed provided crucial responsive and preventative maintenance services across the City West Water network.
“We consider the vital work they undertake as an extension of City West Water in servicing our customers and community every day,” Ms Smith said.
“We have recently committed to extending the partnership with Programmed and look forward to exploring opportunities for us to continue to grow, succeed and improve the way we work together for our customers.
“On top of this, since starting our long partnership, we have worked hard to continuously improve results in operational performance and safety, and have seen Programmed proactively work with us to incorporate our customer-first focus into their programs of work.”
Programmed has an extensive footprint in the water sector, providing operations and maintenance services to water companies across Australia for the past 25 years.
For more information, contact Programmed via info@ programmed.com.au or visit programmed.com.au.
Driving smart solutions for over 25 years in the water industry, Programmed uses a combination of data, backed with a culture of safety and customer focus, to deliver innovative network operations and maintenance solutions to our water customers.
Programmed also provides effective change management processes to optimise service delivery and customer experience, making us an expert in delivering the best results for your water network operation maintenance.
Download our Capability Statement to find out more.
fm.programmed.com.au
APP Group’s water treatment plant at Pindo Deli 2, processes 33 million litres of water per day, for paper and pulp production. Eight filters, containing, two hundred and fifty tonnes of DMI-65®, remove iron and manganese to below the Indonesian Standard of <0.02ppm Fe and <0.05ppm Mn
IRON AND MANGANESE REMOVAL: Build up of iron and manganese in the filter system results in very high maintenance overheads, loss of production and potentially system failure. DMI-65® efficiently removes dissolved iron to the almost undetectable levels as low as 0.005mg/L and manganese to 0.001mg/L as well as particulate, effectively removing this risk.
REMOVAL OF TOTAL SUSPENDED SOLIDS AND TURBIDITY: The DMI-65® also provides the perfect filtration coefficient resulting in excellent mechanical filtration lowering total suspended solids (TSS) to less than 1mg/L and turbidity levels less than 1 NTU.
REDUCED COSTS: The total cost of the iron and manganese removal water filtration system is significantly less than alternative solutions, the effectiveness, but relative simplicity, of DMI65® based systems reduces the upfront capital expenditure on plant complexity as well as the ongoing operational expenditure in chemicals, power and backwash waste water recovery.
HIGH FLOW RATES: The infused technology of DMI-65® promotes the highest oxidation rate of any catalytic filtration media. This permits a significantly higher water flow rate to achieve the same level of iron and manganese removal. DMI-65 can operate at linear filtration velocities up to twice that of conventional media with a corresponding reduction in capital equipment costs.
HIGH LOAD CAPACITY: DMI-65® also has higher iron and manganese load capacity which can extend the duration of filter runs and the time between backwashing, thereby reducing downtime, operating expense and wastage.
REGENERATION NOT REQUIRED: The media operates with a continuous injection of sodium hypochlorite at low residual levels (0.1 to 0.3mg/L) which eliminates the need for Potassium Permanganate.
WIDE OPERATING ENVIRONMENT: Stable and satisfactory performance at pH 5.8 to 8.6 and a maximum operating temperature of 113° F (45°C) reduces the need for investment to alter the operating environment.
LONG LIFE: DMI-65® is not consumed in the process giving it an expected operational life of up to 10 years, providing considerable advantages over other processes or media. The media does not display a decaying capacity to do its catalytic work. Over the 5 to 10 year period, through many backwashing operations of the bed to remove retained solids, an attrition loss of the media occurs by contact between particles and mechanical abrasion.
“Advanced Filtration Media”
Development of the urban fringe surrounding major population centres can be held up or prevented due to existing municipal sewerage infrastructure being too far away or at capacity.
Generally, development throughout Australia has placed pressure on traditional sewerage servicing methods with state and federal governments and utilities agreeing a change in approach is needed to meet regional demand.
The current centralised model requires sewage to be conveyed via extensive pipe networks to a single point for treatment and environmental discharge. Large networks incur high operation and maintenance expenses. These municipal networks are central to service provision but limited when faced with lower population density or distance.
Sustainable sanitation options must combine reliable technology with economic feasibility. One solution is decentralisation which involves the collection, treatment and potential reuse of wastewater from homes and buildings within a single development or community.
From an economic point of view, the most important advantage of decentralisation is reduced investment costs for the network. If wastewater treatment facilities are located at the source (housing areas), the construction of an extended sewage conveyance network is no longer necessary.
Instead, sewage is treated in smaller volumes and reused for applications nearby at lower cost. Given the growing problem of water shortages, particularly for drought effected communities, the more efficient use and reuse of water is a key benefit.
True Water Australia offers innovative sewage management, treatment and reuse solutions for community and urban applications. Through its partnership with global leaders Kubota, True Water has developed an infrastructure model to specifically meet the servicing challenges of regional towns, satellite communities and the urban fringe. In addition, each decentralised system can be tailor-made to suit local climatic conditions, aesthetic requirements, water quality objectives and end uses.
This model was applied in the Greater Flagstone Priority Development Area, south-west of Brisbane. The area has potential to meet the housing needs for the region, but the lack of access to traditional municipal sewerage services was a stumbling block. True Water designed a decentralised solution utilising Kubota’s sewage treatment technology. It provides the best economic outcome, secures operational compliance and satisfies environmental regulations, allowing the development of otherwise unserviceable sites.
The successful collaboration between True Water Australia and Kubota results in the installation of state-of-the-art biological sewerage infrastructure across Australia and the Pacific. The Kubota sewage treatment plants are easy to manage and cost effective, using refined but uncomplicated technology to achieve the highest level of treatment and safety.
Compared to other treatment options, this Japanese technology delivers a highly robust treatment process and low operating costs. The modular systems satisfy rigorous quality benchmarks and manufacturing standards guaranteeing quality, performance and longevity. True Water chooses to utilise Kubota’s state-of-the-art treatment technology to deliver fit-for-purpose, high-quality solutions for every project they are involved in.
Decentralised systems offer great potential to reduce capital investment and ongoing costs for sewerage networks. Consequently, this alternative approach to integrated wastewater management offers a promising alternative to conventional centralised systems, not only to municipalities but also to the private sector.
For more information, visit truewateraustralia.com and contact True Water to discuss your community wastewater treatment needs.
PROVIDING SOLUTIONS FOR:
• Municipal Sewage Treatment
• Commercial & Industrial Estates
• Government Projects
• Residential Developments
• Urban Subdivisions
• Resorts & Caravan Parks
• Mining Accommodation
• Airports & Infrastructure
• Service Stations
• Defence Assets
Non-network solutions are increasingly used to ensure reliability during peak demand events, requiring network distribution businesses to engage with customers to reduce load. By understanding consumer household decision-making and electricity use, CitiPower Powercor created insights to engage customers with messaging, solutions and tactics to maximise participation in peak demand events.
CitiPower supplies power to a 157 kilometre square area across the Melbourne CBD and inner suburbs.
Electricity is distributed in the region via a network comprising over 7,500km of wires, supported by more than 58,123 poles and associated infrastructure. Residential households account for 83 per cent of CitiPower’s 343,000 customer connections. Its network also supports a diversity of commercial and industrial customers, including 51,000 small businesses.
Powercor distributes electricity to 835,000 customers across the western suburbs of Melbourne and through central and western Victoria to the South Australian and New South Wales borders. Electricity is distributed in the region via a network comprising over 88,400km of wires, supported by more than 577,420 poles and associated
infrastructure. Residential households account for 86 per cent of connections. Its network also supports 11,200 medium, commercial and industrial businesses, and 106,500 small businesses.
From April 2018-February 2019, CitiPower Powercor embarked on its Energy Partner project, with the goal of increasing registration and participation in network-initiated demand response (DR) programs.
A CitiPower Powercor spokesperson said that non-network solutions are about managing the ‘peaks’ in the most efficient way possible.
“Historically, to manage such high energy loads on constrained parts of the network, major infrastructure like zone substations would need to be upgraded at great cost to consumers – all to manage just a few hours of high demand.
Easing the load: boosting consumer participation in demand response
“Instead, programs such as Energy Partner allow us to manage those demand peaks much more efficiently and help avoid those costly upgrades that will go underutilised 99.9 per cent of the year.
“By identifying high-usage customers in the areas of potential network constraints, we can then optimise our outreach to households, further reducing the cost of customer acquisition for our programs.”
Customer engagement strategies are considered immature in the electricity sector, with communication channels and messaging broadly targeted without tailored value propositions or segmentation to maximise event participation.
The Energy Partner project team engaged CitySmart to examine household personas within its service areas and overlay those personas with electricity load profiles.
“CitySmart is a social enterprise that works with Energy Consumers Australia and helped them develop household energy personas for tariff research in 2016. CitySmart partnered with Queensland University of Technology (QUT) to provide statistical analysis and deep insights using behavioural econometrics,” the spokesperson said.
QUT qualitatively surveyed customers to identify persona alignment, subsequently overlaying these personas with customer load profiles to apply load profile archetypes.
QUT also administered quantitative surveys and undertook a statistical analysis of results – descriptive analysis of measures, reliability and validity testing of self-report scales, significance testing and segmentation analysis using twostep cluster analysis.
The networks engaged with the Royal Automotive Club of Victoria (RACV) as a channel partner to help support the mixed methods research conducted by QUT. Collaboration with RACV was sought to leverage the member organisation’s brand reputation and awareness to drive customer outreach and engagement in the research.
“QUT provided the technical and academic acumen to ensure robust research outcomes. RACV supported this project in customer outreach to survey on both quantitative and qualitative assessments,” the spokesperson said.
This analysis was then tested through focus groups and customer outreach to determine the most effective messaging and channels to drive DR event performance among different household types.
The research provided CitiPower Powercor with a number of insights around consumer household decision-making and electricity use – information that is all crucial in enlisting the help of customers during peak demand events.
“We broke down the total kilowatt-hours used by 70,000 customers and compared it to their time of use. This provided us with some great insights into where our marketing efforts should be targeted,” the spokesperson said.
“We can also break down customers into lifestyle segments, to which we can tailor messages and increase uptake and performance.
“By correlating load profile ‘types’ with lifestyle segments, we were able to demonstrate clearly how attitudes lead to behaviour in relation to electricity choices.
“In one striking example, we found that 30 per cent of usage at a certain point in time comes from just 0.3 per cent of households – so a fantastic group to target with specific messaging.”
The spokesperson also commented that having an established relationship with customers is critical to achieving marketing cut through.
“Once customers hear about the benefits, the conversion rates are quite high. The primary barrier is the initial communications and conversion in the marketing funnel. For utilities this is particularly challenging as we do not, historically, have a strong relationship with end-use residential energy consumers.”
Energy Partner received funding through the Australian Energy Regulator’s (AER) Demand Management Innovation Allowance mechanism, which provides distributors with funding for research and development in demand management projects that have the potential to reduce long-term network costs.
The mechanism also incentivises distributors to share their knowledge and understanding of innovative demand management projects.
The program has delivered the following outcomes, all of which have the potential to benefit the wider industry:
• Detailed understanding of customer motivations, preferred communications channels, drivers and barriers to uptake for demand response/demand management programs
• Segmentation of energy consumers by communication channel, energy use and messaging will drive registrations and event participation
• A methodology for prioritising “high value” households for both controlled load and behavioural demand response programs to reduce the cost of customer acquisition
The CitiPower Powercor spokesperson said that application of the research has been extremely successful.
“Energy Partner is just one of a number of demand response programs where we applied the learnings from the CitySmart/QUT research.
“For example, after segmenting households into five usage types, based on load profiles, we were able to determine what percentage of our customers fitted each ‘type’ –and which households were the best target to reduce peak demand.
“Forty per cent of households fitted into a category we determined to have a high evening peak use, making them an attractive group of customers to target for any demand response program.”
Industry 4.0 is ushering in a new era for industry, with more intelligence and connectivity, combining machines, computers and the internet to make systems smarter. This has implications for industrial motor control, especially for mature technologies like soft starters.
With the right technical capability (e.g. interchangeable smart processor cards), soft starters can control a whole system by connecting directly to other devices such as pressure, flow and depth sensors in a pumping application.
They can also become more efficient. According to the International Energy Agency, electric motors account for 69 per cent of total industrial electricity consumption in the world. Reducing this consumption is important. Around 80 per cent of motor applications are most effective with fixed speed. Selecting the correct control mode for the application (fixed or variable speed) is critical for true energy efficiency.
Engineers are embracing the use of new generation ‘premium efficiency’ motors. IE3 motors are more efficient than IE2 motors, resulting in lower lifetime energy usage and energy costs, which has obvious value. However, other IE3 motor characteristics are affected by the changes made to achieve this efficiency.
This includes starting issues such as higher inrush and starting currents that stress electrical supply circuits, and spiky pull out torque curves that can make smooth control of acceleration and deceleration more difficult.
Soft starters can address this by limiting inrush and starting current to the minimum necessary to start, which enables design of efficient distribution circuits and prevents breaker
trip due to motor starting. Soft starters also precisely control the starting and stopping of IE3 motors, offering control over acceleration and deceleration to cater for motors with tough torque curves.
An internally bypassed soft starter is 99.5 per cent efficient when running, which equates to a potential 80 per cent reduction in waste energy compared to a misapplied variable speed drive. It also produces no harmonics during run, improving overall power quality and eliminating system losses resulting from harmonics.
In addition to energy savings, Industry 4.0-ready soft starters offer:
Ease of use for technical staff: A graphical display with multiple languages and in-built intelligence such as application setup menus make installation and commissioning easier and faster. The ability to replicate these settings across multiple starters by extracting parameter information using a standard protocol like USB is also important.
Ability to extract and share data: Connecting with other devices and support services must be straightforward, including a range of communications modules enabling network connections. Mobile technology is also being leveraged by soft starter manufacturers, with smartphone app access to extracting starter and performance information for analysis and sharing.
Automation capabilities: Built-in timers and schedulers improve system efficiency and allow operations to be tailored to a site’s requirements. Automatic resets and flexible protection options can be programmed to eliminate manual interventions and ensure continued operation.
Operational reliability: This includes starter, motor and system protection functions and associated notification and alarm capability, and features like emergency override to suppress all protections for a situation when the machine simply has to run.
Fully featured motor control solutions
AuCom’s EMX4i now available in the full range of current ratings
And now introducing 1000V soft starters to the EMX4i range Features
• XLR-8 control to prevent water hammer
• Emergency run mode
• Real time metering & monitoring
• Automated pump clean function
• Extended motor protection functionality
• Clock & calendar scheduling
While renewable energy solutions are gaining traction in Australia, only homeowners have been able to access the benefits of in-home solar power and battery systems. More people living in rental accommodation will soon have access to cheaper, renewable energy as part of an Australian-first microgrid project led by energy solutions company Ovida.
Offering renters in multitenanted sites with green energy solutions has always been associated with high costs and complex installation and operation. However, Ovida is seeking to prove that occupants of commercial and residential multi-tenanted sites can easily access and benefit from solar power and battery storage through a community microgrid.
According to Ovida Community Energy Hubs Project Manager, Elissa-Jane Bowden, this could be made possible by trialling a flexible microgrid solution that would remove the barriers, such as high upfront costs, lengthy payback periods and difficulty surrounding solar installation approvals from property owners.
On 19 December 2019, the Victorian Minister for Energy, Lily D’Ambrosio,
launched the first site of Ovida’s $2.3 million Community Energy Hubs project – a 52-resident community housing apartment building in Preston with a solar and battery storage system, making solar energy available to all residents.
The initiative is supported by a $980,000 grant from the Victorian Government’s Microgrid Demonstration Initiative and includes project partners
Allume Energy, Australian Energy Foundation, Housing Choices Australia, RMIT University and Jemena.
“Ovida established a Consortium Partnership with Allume Energy, who designed the Australian-first SolShare technology that monitors each apartment’s energy demand and distributes the electrical energy,” Ms Bowden said.
Ovida Executive General Manager, Chris Judd, said the initiative uses smart technology to bring renewable energy to people who were not able to access it in the past such as renters and low income earners.
“It will drive down their electricity bills by providing solar power that is cheaper than their grid electricity costs,” Mr Judd said.
“Ovida installs, operates and maintains the solar panels, batteries and energy distribution technology free of charge. Residents and tenants have the opportunity to opt in to the initiative and will continue to have choice over their electricity retailer.
“This is an exciting milestone as it is the first time this microgrid technology has been used to allow one solar and battery installation on an apartment building to be shared with all apartments.”
Solar panels on the rooftop of the Preston apartment building convert the energy from sunlight, with solar inverters converting the electrical energy into the type of power required for homes and the electricity grid. These inverters then send the power to Allume Energy’s SolShare technology.
The SolShare technology shares electricity between residents by distributing power on an on-demand basis to maximise on-site solar usage. SolShare directs solar energy to the apartments in relation to how large their load is at any given time.
“This optimised sharing means that the on-site solar usage is 30-35 per cent higher than an individual system, limiting the amount of solar that is not used,” Ms Bowden said.
“The SolShare is the most efficient system to maximise the use of energy
generated at any given time. It achieves this by supplying energy to where it is needed most, instead of sending it back to the grid.”
The installed system is 73kW solar and 46kWh of battery storage, designed to produce 83MW per year or an average of 227kWh per day.
VICTORIAN MINISTER FOR ENERGY, THE HON. LILY D’AMBROSIO, INSPECTS THE COMMUNITY ENERGY HUB EQUIPMENT, WITH GIPPSLAND/RACV SOLAR SYSTEM DESIGNER, BRENDAN LAIDLAW, AND CHIEF EXECUTIVE OFFICER, ANDY MCCARTHY. THE SOLSHARE TECHNOLOGY, DESIGNED AND MANUFACTURED BY MELBOURNE-BASED ALLUME ENERGY, MONITORS ALL THE APARTMENTS’ ENERGY DEMANDS AND DISTRIBUTES THE ELECTRICAL ENERGY TO THE APARTMENTS OR THE BATTERIES TO STORE IT FOR USE LATER.
“The building, prior to the installation, had an average daytime energy demand of 599kWh per day, so the system will provide on average 39 per cent of the building’s energy needs. We are assessing the performance of the system currently and our results show a slightly higher amount of displaced grid energy, but our results are preliminary at this stage,” Ms Bowden said.
As the microgrid is a supplementary source of energy, all apartments remain connected to the electricity grid to ensure they have a constant electricity supply. They receive electricity from the electricity grid when there is a high demand on the on-site solar and battery storage system, or when the sun is not shining. Any excess energy is sent back to the grid and compensated for accordingly.
Residents pay a low fixed rate for the solar energy they use, which is about a third of the cost of their grid electricity rate. It’s expected that residents will save approximately $150 per year on electricity bills, or about 15 per cent.
“Our early results are positive and show the residents have higher savings than estimated, but the results are still preliminary,” Ms Bowden said.
There are no upfront costs for residents, who are free to opt in or out of the system as they choose.
According to Ms Bowden, the project’s challenges included technical and equipment challenges for relatively untested enabling technologies, design challenges with the limited space available for the microgrid equipment, a legal and regulatory landscape that had not anticipated such a solution, and the complexity of developing and testing a technical solution that satisfies the interests of multiple parties.
While challenges such as these could easily derail a project, Ms Bowden said that the various parties working on the project worked tirelessly to overcome problems and achieve a successful result.
“The technical and design challenges of the project were very well
managed by Gippsland Solar, who were successful in the competitive tendering process for installation because they presented an innovative, efficient and cost-effective design that resolved several site challenges,” Ms Bowden said.
Throughout the 12-week installation period, Ovida, Allume and Gippsland Solar, which was acquired by RACV in December 2019, collaborated extensively to ensure the installation went as smoothly as possible and the impact on the residents was minimised. However, there were still plenty of installation challenges that the Gippsland Solar/RACV team encountered, such as installing 1.5km of overhead cabling and working within the 3m by 4m solar equipment cage.
Another key challenge was engaging with the building’s residents to participate in the microgrid system.
“Residents can choose to participate in the program, so we needed to meet with all the tenants in person to explain the project to them and how it could help them reduce their energy bills. The more residents that participate in the system, the more energy savings they receive and the more effectively the system operates,” Ms Bowden said.
“We needed to explain the new technology in five different languages, including Auslan, and communicate creatively with BBQ group information events, one-on-one meetings, video, posters and letters. Thankfully Housing Choices Australia, who owns the building, and our partner Australian Energy Foundation, helped us work closely with the residents so they were supportive of the project and engaged in the process.”
Ms Bowden said that as a demonstration project, the key objective is to identify the barriers to developing a scalable commercial microgrid, so that it can be sustainably replicated across Australia.
“But as the first step, we are testing and optimising the technology, influencing, where possible, regulatory policy to support this type of new energy model, understanding the
property owner response to the product and participation rates, as well as assessing the demand response capabilities of the system to support peak demand periods in the network,” Ms Bowden said.
Information learnt from the project will be shared with government, key stakeholders and the industry broadly, to in turn support the journey of the energy industry to provide more choice and flexibility to customers in their energy options.
As the energy industry looks to the future, residential solar and battery systems are likely to play a more prominent role.
“The high take-up of residential solar looks set to continue with the bulk of solar being deployed currently in residential systems of 2-5kWh. This has been driven by the reducing cost of solar over the last five years, and it appears battery storage costs will follow that journey, with more efficient and cheaper batteries, potentially supported by government subsidies like the STC program that has been successful in supporting solar penetration in Australia,” Ms Bowden said.
The value of a battery in a residential context is that it maximises the benefit of solar generated by storing it during the day, and providing it the evening when the majority of energy is used in a home. As the cost of storage comes down, a rapid uptake of that technology is likely to be seen.
“We are starting to see the incorporation of solar and battery systems into new home builds, with developers looking to make their homes more efficient and more attractive to buyers. In addition, energy retailers are offering subsidies or discounted solar and battery storage packages to provide a cheaper system to the resident, with the resident being able to utilise the battery storage for their own use, as well as participate in market programs that drive additional revenue streams through a Virtual Power Plant program,” Ms Bowden said.
Your health and safety, along with that of our partners, employees and communities, are our highest priorities
We’re privileged to have earned the trust of the world’s leading infrastructure and utility companies. And we’re committed to help them navigate these uncertain times to function safely, efficiently and reliably.
We recognise, and remain fully committed to our role supporting our customer’s operations in today’s exceptional circumstances. And like you, we’re monitoring the situation closely and taking the necessary steps to maintain the continuity of products, services and support we provide.
So, among the many things we’re doing to ensure we’re best supporting our customers, we’re providing complimentary access to select offerings in the cloud until June 30, 2020 to keep your engineering and operations running safely during this time
For more information regarding access to our offerings please visit sw.aveva.com/about‐covid‐19
Or to discuss how we can help your teams function smoothly in these unprecedented times, please contact feedback@aveva.com
Critical infrastructure calls for critical equipment. Cybertec cellular modems are trusted by the Australian utilities sector for their reliability, rugged build and ease of use. The Cybertec 2255X is utilised and favoured by utility providers Australia-wide.
Cybertec cellular modems have been deployed and trusted in the Australian utility sector for well over a decade. There is good reason for their continued use across model upgrade lifecycles.
Customers trust the rugged construction coupled with the ability to withstand high temperature environments often associated with operating in the utility sector.
High availability and uptime are critical in these sectors, so having a modem that can adapt as the network environment changes around it by continually monitoring its connection status and quality is imperative.
Across the Australian power utilities sector, pole-mounted reclosers are utilised extensively to provide the ability for the power company to segment off areas of the power grid.
Reclosers are used to limit the disconnection impact to customers when a fault occurs, as well as to allow maintenance to be carried out with minimal customer impact.
Although the reclosers are a self-contained and intelligent device operating autonomously, the ability to monitor and interact with the reclosers remotely is required.
This is where Cybertec cellular modems excel. During normal use, the recloser is monitoring the voltages and currents travelling through the power grid. This consumption data allows the power company to monitor and control loads over the network.
In this condition, the Cybertec device is serving poll requests for data from the power distribution centre software, and converting these from Ethernet-based requests (TCP) to the serial protocol as used by the recloser.
Should a fault arise in the network surrounding the recloser, such as a tree branch has fallen across the lines, the recloser will shut down power to services downstream of
itself. This action will result in the status of the recloser being relayed back to the control centre to alert service crews.
The Cybertec device is critical to ensure the alert is successfully received by the control centre. Ensuring that the recloser is operating correctly and monitoring its health is as important to its operation as the job it performs. For this reason, having secondary access to the recloser via another serial port is necessary.
This additional channel to access the recloser allows engineers to download log files, perform calibration and firmware upgrades as and when required, without interrupting the operation of the recloser. The Cybertec 2255X model includes this additional serial port and provides this diagnostic access to the recloser over the cellular link.
The majority of remote control and monitoring of reclosers is performed using the industry standard DNP3 protocol. The Cybertec modems are aware and compliant to this protocol and even support a range of digital inputs and outputs which can be controlled and monitored from the control centre using the same DNP3 protocol.
This ensures a reduction in complexity of the system and the ability to support additional features like a tamper switch on the enclosure door and switching on and off ancillary equipment as required.
The ability to control the digital IO on the Cybertec 2255X and reboot the modem is all possible using SMS commands sent to the device. Security is provided in the form of a configurable whitelist to ensure security adherence.
It is for these reasons that Cybertec cellular modems are the perfect fit for the Australian power utilities sector, as well as many other industries where a highly reliable, rugged and Australian-designed and made modem is required. For more information, visit www.madison.tech/cybertec.
What you can do today with a poly tank is really only limited by your imagination. They are stronger, more versatile and easier to install on site than ever before...
• Great range of fittings and sizes
• Reduced civil requirements
• Compliant to DG standards
• Meets bunding regulations
• Purpose built
South Australia’s principal electricity Transmission Network Service Provider (TNSP), ElectraNet, recently won Energy Networks Australia’s 2019 Industry Innovation Award for its Dalrymple Battery Energy Storage System (BESS). The remarkable project is now in full commercial operation and is the first BESS in the National Electricity Market (NEM) to provide both regulated network reliability and security services alongside competitive market services.
As one of the most extensive regional transmission systems in Australia, ElectraNet’s network extends across some 200,000 square kilometres. The transmission network has more than 90 substation sites and 5,500 circuit kilometres of transmission lines operating at 275,000 and 132,000 volts.
The Australian Energy Market Operator’s (AEMO) Integrated System Plan (ISP), published in July 2018, highlighted that energy storage has a significant role to play in the future energy system with the continued growth of intermittent renewable energy sources.
The Dalrymple BESS showcases the widest range of services provided by a grid-connected BESS in the NEM, covering both energy and system security services.
ElectraNet designed, built and owns the Dalrymple BESS and leases commercial operation to AGL. The project received part-funding from the Australian Renewable Energy Agency (ARENA).
The objectives of the project were to demonstrate that utility-scale battery storage can effectively:
• Provide network reliability and security services alongside competitive market services in a network with a high penetration of renewable nonsynchronous generation
• Provide “seamless” islanded operation with 100 per cent renewable generation following transmission outages
• Demonstrate a commercial model for the provision of regulated services and competitive energy market services, and build delivery capability for such assets
The Dalrymple 30MW, 8MWh BESS is the first transmission grid-connected battery in the NEM providing both regulated and competitive market services.
The success of the project required significant innovation and leadership, including:
• A first-of-its-kind commercial model to support the provision of regulated reliability and security services by a Network Service Provider (ElectraNet) alongside competitive market services (provided by AGL), challenging perceived limitations to network ownership of battery energy storage technologies
• Navigating the market registration, licensing and connection processes for the first time, paving the way for others to follow
• Largest autonomous regional microgrid development to date co-optimised for both grid-connected and islanded operation, with 100 per cent renewables allowing seamless transition between the two operating modes (for both planned and unplanned islanding)
The Dalrymple BESS also provides pre-emptive emergency response as part of the South Australian System Integrity Protection Scheme (SIPS), providing fast power injection into the network following a significant loss of generation, which helps prevent a major loss of supply to customers.
Rainer Korte, Group Executive: Asset Management at ElectraNet, said that the Dalrymple BESS also includes several other innovative features relative to other generation and energy storage projects.
“Firstly, the inverters have grid-forming capability, as well as the ability to operate at very low short circuit ratios (<1.5), which is significantly beyond what existing grid-forming electronic converter-based generation can perform. The fast frequency response (synthetic inertia) also has unprecedented response speed (less than 100ms) and bandwidth (frequency droop down to 0.2 per cent),” Mr Korte said.
Additional features include:
• The non-synchronous fault level/system strength has a support capability which runs via short-term fault current overload (>1.0pu rating)
• Islanded grid master control, including wind farm generation MW dispatch/curtailment facilitating supply to the local island indefinitely under reasonable wind conditions
Dalrymple BESS: the groundbreaking energy storage initiative
• Black start capability for the local island with a peak demand of 8MW
• Largest-known indoor and climate-controlled BESS installation (30MW), with the advantages of quicker installation and lower cost compared to containerised battery solutions
• Topology-based Islanding Detection Scheme
• Control system that allows for an external set point, voltage and reactive power regulation or power factor regulation based on control mode priorities
“The BESS can be operating at full capacity and providing meaningful network support within 350ms of a network event being detected about 400km away in the south east of South Australia.”
The Dalrymple BESS demonstrates utility-scale energy storage as a key enabler of large-scale intermittent renewable energy on an interconnected power system.
“It also demonstrates the application of energy storage to providing essential system security services, such as fast frequency response (FFR), that enable a higher penetration of renewable energy by allowing more conventional synchronous generation to be displaced by renewable generation,” Mr Korte said.
Additionally, the Dalrymple BESS enables the operation of a local islanded system following the loss of transmission supply where demand is supplied by the local wind farm and small-scale solar generation supported by the BESS – with no conventional generation, and regulation services provided by the BESS.
“This will lead to learnings that are applicable at a broader level to a South Australian system with 100 per cent renewable generation, such as the amount of storage that is needed to manage varying levels of demand and intermittent generation,” Mr Korte said.
“More specifically, customers on the Lower Yorke Peninsula are already benefiting from improved reliability with the Dalrymple BESS keeping the lights on during planned and unplanned 132kV transmission line outages.”
ElectraNet conducted a competitive tender process to select Consolidated Power Projects (CPP) as its Engineering Procurement and Construction (EPC) contractor who engaged ABB as power system integration partner.
“With several novel applications, cooperation was required between ElectraNet, AGL, AEMO, CPP and ABB to implement BESS functionality,” Mr Korte said.
“Given that this had never been done before, a key challenge in the execution of the project was determining suitable BESS control parameters for grid-connected as well as islanded operation. The key to overcoming this challenge was the positive collaborative effort between ElectraNet, CPP and ABB, particularly when optimising these parameters proved more difficult than expected.
“The project had ambitious objectives that targeted a wide range of battery services, including the unprecedented islanding of an 8MW distribution area with the 90MW Wattle Point Wind Farm.
“The collaborative approach taken by all involved in the project was again key to overcoming this challenge, particularly in regards to the regulatory approvals, registration and technical delivery, and achieving seamless islanding with the Wattle Point Wind Farm, which was originally considered as a stretch goal, was hugely satisfying.”
Regulatory arrangements were not well developed to support the connection of the BESS to the NEM with its unique commercial arrangements, but by working with market and regulatory authorities, including AEMO and the Australian Energy Regulator (AER), ElectraNet was able to develop regulatory solutions to support the project.
In its first six months of operation, the Dalrymple BESS experienced several planned and unplanned transmission network outages, which required the BESS to supply the local 33kV distribution system to successfully maintain customer supply for up to seven hours.
In addition, the BESS successfully rode through network fault events with its measured voltage, active power and reactive power response in line with design and technical performance expectations.
The BESS responds almost instantly to the system voltage depression during a fault and injects a significant amount of active and reactive power into the network to support network voltage recovery.
Customers are benefiting from the Dalrymple BESS operation through improved reliability and security, and the provision of competitive market services.
The project is also helping support the transition to smart grids, with the Dalrymple BESS’ fast frequency response functionality now a standard requirement for new BESS grid connections. With the Dalrymple BESS being one of the first to be registered in the NEM, it has also assisted AEMO in developing registration procedures for utility-scale battery technology.
The project has incorporated a knowledge sharing portal, which provides a significant amount of information to assist the entire utility industry in observing first-hand how the Dalrymple BESS is performing. The knowledge sharing portal can be accessed via www.escri-sa.com.au.
The project is also being closely observed by AEMO to gain insights into how a BESS can effectively provide system security services. The experience gained from this will assist to determine when a BESS can be relied upon to provide such services, potentially leading to less reliance on synchronous generation to provide system security services in the NEM.
Accessing clean and reliable drinking water is an issue facing many remote and isolated communities across Australia. Utilising the power of community, smart meter technology, and First Peoples’ knowledge and connection to water and country, a recent project by Griffith University researchers has provided pragmatic and cost-effective options for alternative water management approaches that could secure consistent and long-term supply in these communities.
The first of its kind in Australia, the Remote and Isolated Community Essential Services (RICES) project, led by Dr Cara Beal, Associate Professor, School of Medicine and Cities Research Institute, Griffith University, aimed to explore community-driven frameworks that would enable long-term supply and efficiency of water and water-related energy in remote and isolated Aboriginal and/or Torres Strait Islander communities.
The implementation of smart meters, which played a pivotal role in the project, used in tandem with communitybased water demand strategies such as education, feedback, storytelling, information sharing and encouragement, were shown to be powerful tools in motivating behaviour change and encouraging water efficient practices.
Importantly, the project results found that if communities are given the right information and resources, they can, and will, use less water and energy.
In order to try and address the issue of water accessibility and reliability in these remote and isolated communities, the researchers first needed to understand the challenges they faced.
Unlike their urban counterparts, remote and isolated communities have unique geographical, environmental, political, economic and cultural contexts that must be considered in developing successful water management strategies.
The quality and functionality of household health hardware, such as taps, showers and toilets; a distrust of ‘town’ water due to the frequency of ‘boil alerts’; and significantly higher outdoor water use present additional challenges.
The changing climate produces less reliable and more
intense weather patterns, natural disasters, and threats to infrastructure and general health and wellbeing in remote communities. These factors exacerbate the challenges, making it essential to have community water management strategies that are resilient and sustainable –environmentally, socially and economically.
A response to the need to work with Indigenous communities to explore community-based water demand management strategies that would be suitable for their individual communities, the RICES project naturally involved the entire community – Indigenous representatives, project participants, council staff, water managers, State Government and industry partners.
Four remote and isolated communities across Australia participated in the project, with community engagement activities taking place throughout all stages of the trial. Activities included individual and group activities, combined and separate community and stakeholder events, and the use of a range of social media and face-to-face communications.
Smart meters, which captured baseline water and energy consumption through state-of-the-art, high-resolution digital meters and logging equipment, were installed at the participating households and proved pivotal to the project. The data from these meters was used to provide participants with individual feedback of water use, and benchmark their water use with others in the community.
Attempting to capture the breadth and depth of First Peoples’ knowledge and connection to water and
country provided researchers with valuable insights into the efficacy of the strategies and enabled them to offer pragmatic options for water management approaches.
A key finding of the project was the need to use a variety of conservation actions concurrently, within a broader water demand management program.
The project findings, as well as previous research in this area, suggest that long-term gains which focus on behaviour change, including community engagement and encouragement activities, are at least, if not more effective than more costly engineeringand technology-specific approaches.
Combining engineering and technology with community engagement, however, proved to be highly effective. The implementation of smart meters in participant households revealed that one quarter of homes had leaks from household hardware (toilets, showers and taps), showing a need for more adept leak and hardware management from essential service providers.
Perhaps more importantly, the water consumption data and benchmarking strategy proved to be a highly favoured demand management option for project participants, with water reductions of up to 40 per cent of pre-trial consumption achieved in participating communities. Water-related energy reductions of between 25 per cent and 65 per cent of pre-trial consumption were estimated.
The popularity of individualised water use feedback, including comparisons with the water use of other households in all four communities involved – from both the community and council/service provider perspective – shows that using data meaningfully, through smart meters and simple number crunching, can have a powerful impact on water management.
However, researchers are keen to note that long-term reductions will require sustained and positive efforts from councils and essential service providers. Participants were also generally in favour of such community-based water demand management strategies, such as council-led community workshops, water conservation education, and community announcements about water use and ways to save water.
The final report for the RICES project, Exploring community-based water management options for remote Australia, merges these insights into a suggested framework for community-based water demand management approaches in remote Aboriginal and Torres Strait Islander communities.
Any approach must be built around community involvement, with particular importance given to involving Indigenous representatives from the start. Education (e.g. water efficiency programs, community workshops and water stories) and encouragement measures (e.g. smart meters to benchmark household water use, mark individual water use and weekly usage community notices) are integral and should increase over time.
In order for the collaboration to be truly effective, local, state and federal governments must budget sufficient community engagement costs into any program development and tailor these programs to suit the individual limitations and opportunities within each community. Ongoing collaboration between councils and/or service providers and communities are essential.
Equal and ongoing collaboration must take place between the Aboriginal and Torres Strait Islander community and council and service providers in the transition toward an independent, resilient and sustainable water supply.
Edge Underground is a precision microtunnelling contractor that operates in Australia and the USA. With a focus on innovative technology and expertise, Edge Underground designs and enhances the performance of trenchless equipment. OUR SERVICES
• Microtunnelling
• Pipe Jacking
• Thrust Boring
•
Many of Sydney Water’s assets – including its network of 46,000km of pipes, treatment plants, pumping stations and reservoirs – are in remote locations, a demanding and complex maintenance task to manage over a large operating area.
Currently, trunk main assets are successfully monitored and controlled using SCADA technology. When it comes to distribution networks, however, this becomes a more challenging task, with customer feedback the main channel for sensing problems.
Sydney Water was looking for the capability to predict and proactively prevent faults from impacting customers. Telstra was able to provide a digital solution to facilitate monitoring its smaller assets using Internet of Things (IoT) technology.
Together, Sydney Water and Telstra developed a Proof of Concept (PoC) to enable Sydney Water to evaluate the business case in using IoT for water management.
The project comprised four key use cases: sewer blockage, environmental overflows, water pressure and digital metering. All were aimed at providing better customer outcomes.
The first two cases used over 250 devices and advanced algorithms to monitor sewer levels and flows. This allowed Sydney Water to preemptively stop pipe blockages and overflows which could impact both customers and the environment.
The third use case deployed sensors on the distribution network to provide data on water pressure to predict and help prevent leaks and other incidents, including water theft.
The fourth use case was to assess the value of digital water meters on customer properties. This showed digital metering can help to detect leaks in customers' properties or surrounding networks, helping to minimise water wastage and assist in providing customers with more accurate water bills.
The PoC approach has been a success for Sydney Water, with the project winning the Committee for Sydney’s 2018 Smart City Award for ‘Best NSW Government Initiative’. The success of the PoC project resulted in the Sydney Water Executive approving a further roll out of the technology to 10,000 additional locations.
To date, the program has helped to detect 37 wastewater blockages that could have resulted in customer or
environmental impacts, as well as a potential overflow that could have affected more than 4,000 properties. In addition, it has demonstrated that installing digital meters in customer properties can detect leaks at 8-10 per cent of all properties.
Together, Sydney Water and Telstra are striving to bring the benefits of IoT to the water industry. Telstra is working with device manufacturers to optimise LTE-M and NB-IoT devices on Telstra's IoT network, including improved battery life, better operation in challenging environments, improved digital water meter functionality and interoperability standards.
Telstra's IoT water solution brings together Telstra's IoT platform and comprehensive IoT network. This has given Sydney Water the opportunity to try multiple solutions and explore how IoT can help it care for the environment and its customers.
Visit Telstra.com/iotwater to find out more.
The rise and scalability of renewables is creating vast opportunities for utilities to embed sustainable sources of energy generation across their infrastructure and reduce their reliance on expensive grid electricity.
Expanding the concept from a residential setting, utilities are discovering the ability to harness the generating capacity of solar panels, and economic merit of energy storage devices and other innovative technology on a large scale, by unlocking value from their existing footprints and operational processes.
SA Water’s goal of a zero-cost energy future is leading the Australian water industry in its unique approach, which is set to neutralise one of the utility’s largest operating expenses and deliver sustainable environmental outcomes.
Through a range of complementary initiatives, underpinned by increasing its renewable energy generation and storage exponentially, SA Water is working towards zero-net electricity costs in the future.
As one of South Australia’s single largest electricity users, the utility’s energy-intensive drinking water and wastewater pumping and treatment operations across the state cost $83 million in 2018-19.
Stimulating innovative thinking, SA Water embraced the opportunity to electrify its own energy sources and is investing more than $300 million to install 242GWh of energy generation from new solar arrays and 34MWh of energy storage devices across its sites.
The power generated and stored on-site will reduce SA Water’s reliance on expensive grid electricity and create a revenue stream from carefully timed sales back to the market, to offset the cost of electricity that will need to be purchased at times of peak demand or low solar productivity.
SA Water Senior Manager Supply Chain and Zero Cost Energy Future, Nicola Murphy, said more than 500,000 solar photovoltaic panels will be deployed over the next 12 months as part of the program.
“We’re delivering initiatives to keep our operations as efficient as possible to help keep customers’ water prices as low and stable as possible,” Mrs Murphy said.
“Large operational circuit breakers like this are essential to achieving savings.
“Our water and wastewater treatment and pumping operations provide up to 1.7 million people across South Australia with safe, clean drinking water every day, but are very energy intensive and make us one of the largest electricity users in the state.
“In the same way that many South Australians have harnessed the benefits of solar panels at home, we’ll make some of our physical assets work harder for us, taking advantage of our large buildings, roof spaces and land holdings to generate a sustainable source of energy.
“Across our major treatment plants and pipeline pump stations, to some of our depots and workshops, the rate of return makes this an obvious investment to help neutralise a substantial operational expense, while demonstrating the way renewable generation can be integrated at large utility scale.”
In an average weather and water consumption year, SA Water projects its solar generation capacity will provide 70 per cent of its electricity consumption – enriched by energy efficiencies and complementary sources of renewable energy.
“Locating generation behind the meter will improve our resilience to grid interruptions, significantly reduce our network charges and isolate our business from electricity market price volatility, in both the short and long term,” Mrs Murphy said.
“We’ll always need to use and buy some electricity, but we can be smart in our approach to managing it as we work towards a zero-cost energy future.”
The Australian water industry is energy intensive, requiring approximately 3,000GWh of electricity annually, with SA Water consuming almost one fifth of the national total.
SA Water’s program to pursue a zero-cost energy future is not only driven by a desire to sustainably cut costs for the benefit of its customers, but is also in recognition of the organisation’s social responsibility to reduce its environmental footprint.
Mrs Murphy said it’s vitally important that water and wastewater utilities explore opportunities to reduce their carbon emissions.
“The most significant challenge facing the industry right now is climate change and its impact on water supply,” Mrs Murphy said.
“A warming climate, rainfall and carbon emissions are all intertwined, and we’re actively responding by harnessing innovation to deliver sustainable water services.
“Our high electricity bill in 2018-19 is attributed to more energy-intensive pumping and treatment required to support increased water demand and lower reservoir inflows during last year’s dry summer and winter, which ultimately impacted our ability to limit emissions.
“By enhancing our sources of clean energy, we’re pushing ahead on our path to tackling the effect of climate change.
“Our investment in 242GWh of energy from solar generation will deliver substantial positive environmental outcomes, helping reduce our emissions by more than 89,000 tonnes a year – the equivalent to planting seven million trees or removing more than 32,000 cars from the road per year, every year of operation.
“Solar generation is a proven form of renewable energy, and it’s availability, and scalability, enables the technology to be integrated swiftly within our existing energy management portfolio, achieving the greatest impact on our environmental performance.
“Importantly, our progressive leap forward will help the global transition to a low-carbon future.”
SA Water’s deep understanding of energy’s role and influence as part of its operations, and expertise in embedding innovative mechanisms that provide greater flexibility and control, demonstrates how it is evolving from ‘energy procurement’ to ‘energy management’.
The new solar arrays are only one piece of the energy puzzle – the utility’s integrated approach is the cumulative effect of seven initiatives that include demand scheduling, energy efficiency, energy storage and generation, and energy market levers.
Mrs Murphy said the diversity of initiatives were positioning the utility to effectively manage its energy portfolio for the long term.
“Our pursuit of a zero-cost energy future builds on a strong foundation of energy management, which has delivered savings of more than $3 million a year from our electricity bills since 2013, so we know it’s within reach,” Mrs Murphy said.
“Biogas and hydroelectric generation, and trading as a market participant, are a few of the initiatives contributing to our industryleading approach.
“Two of our wastewater treatment plants in metropolitan Adelaide are already 80-90 per cent energy self-sufficient, achieved by burning the natural biogas created through the sewage treatment process to extract the methane content and generate electricity, effectively turning waste into energy.
“Hydroelectric systems integrated within our water network harness the force of moving water and contribute around 7,000MWh per year, equating to 14 per cent of the total electricity we currently produce.
“Augmenting our energy portfolio with an abundance of solar generation and storage devices underpins our vision of zero-net electricity costs and elevates our ability to achieve it.
“We’ve set ourselves an ambitious goal, but this kind of innovative thinking can shake up traditional models and deliver sustainable savings – and we’re backing ourselves and our key partners to deliver it.”
The RAPTOR vehicle mount system is extremely fast at acquiring quality 3D subsurface data. A choice of 800 MHZ for detection of shallow services and road layers, or a 450 MHZ for deeper utility detection. High-speed acquisition up to 130 KM means less time detecting and more time for processing. Modern 3D processing software ensures fast processing data. Keys to a successful project.
· Available in two frequency options for precise mapping
· Up to 18-channels (450 MHz) / 28-channels (800 MHz)
· Talon Acquisition software included with the system
· Optional Software for fast data processing and visualization
· Convert into a cart-based system for smaller worksites
· SIMPLE, EASY, FAST
The last few months have shown how quickly situations can change, with the COVID-19 pandemic sending shockwaves through the global economy and affecting business operations in every industry. If contracts start to dwindle, hiring reduces the risk of equipment sitting idle and also allows companies to trial how it fits into operations without committing to a large initial investment.
Cost is a significant factor as poly welding equipment typically requires a medium to large initial outlay. Hiring has the advantage of removing ownership costs such as storage, maintenance and calibration, allowing for more working capital, and costs can be calculated week to week, which makes budgeting easier. This is particularly important when the full economic impact of external factors such as COVID-19 are still unknown.
For long-term projects, it makes sense to buy poly welding equipment as you’ll pay less in the long run. However, if the equipment is only for specific contracts or one-off jobs, hiring is probably the better option. A good rule of thumb is that if you use the equipment less than 60 per cent of the time, it may be better to hire – this figure may increase if the pandemic continues to disrupt supply chains and put entire industries on pause.
Buying comes with the additional costs associated with maintenance, support and servicing, whereas the supplier is responsible for these when hiring welding equipment. Hiring also provides access to the latest technological advances without the commitment of buying.
When faced with the decision to buy or hire welding equipment, civil contractors and utility companies should consider what the job involves, their budget and how much flexibility they need. There are pros and cons for both buying and hiring equipment, and in times of crisis, risk mitigation is key.
Whatever you choose to do, it’s essential to go through experienced suppliers such as Caldertech Australia – which has been supporting customers in choosing their PE pipe fusion or flow control equipment for more than 30 years. For more information, please visit caldertech.com.au
So, whether you are installing or repairing PE pipe for small or large civil projects, you can count on us to have the solutions and equipment for you.
Damaging existing utilities can be costly in terms of project downtime and potentially significant fines. The new Verifier G3 underground utility locator by McLaughlin delivers durable design, the most accurate push button Peak depths in the market, plus a new combined Peak/ Null operator friendly screen. Contact your local Vermeer dealer to see one in action.
Sydney Water’s Lower South Creek Treatment Program was awarded the highest design sustainability rating ever achieved for an Australian water infrastructure project by the Infrastructure Sustainability Council of Australia (ISCA). The high score was given to its $450 million program of upgrades to three treatment facilities in Riverstone, St Marys and Quakers Hill involving two Australian-first technology innovations and two NSW-first process innovations.
The upgrades aim to improve the quality and reliability of Sydney Water’s Riverstone, St Marys and Quakers Hill treatment facilities in order to cater for growth in the area. Sydney’s North West is predicted to grow by an additional third of a million people by 2040, which is equivalent to the population of Newcastle, NSW’s seventh largest city.
The program involves the adoption of several new technologies that will help make water treatment more sustainable, cost efficient and effective for Sydney Water. It’s these innovations
that are set to achieve a 42 per cent reduction in whole-of-life greenhouse gas emissions that earned the program the “excellent” design rating of 69.7 points from ISCA, the highest ever for a water project.
The program received a full ten out of ten score for innovation from ISCA, with two of the innovation points awarded for exceeding the benchmarks for energy and carbon reduction, and renewable energy supply.
So far, a major upgrade to the Riverstone Wastewater Treatment Plant has been completed which increased the capacity of the plant by more than three times, from 4ML per day to 14ML per day (megalitre = one million litres).
Upgrades to the Quakers Hill and St Marys Water Recycling Plants (WRP) are currently underway and are set to be completed in 2021. It’s these two upgrades, plus a repurposed 12.5km transfer pipeline between the two plants, that were the scope for the Infrastructure Sustainability (IS) Design Rating.
A spokesperson for Sydney Water said the repurposed 12.5km transfer pipeline will allow the utility to centralise biosolid treatment at St Marys WRP, which is in an industrial area.
“This will reduce the noise and traffic impacts at Quakers Hill WRP, which is located in a predominately residential area. We will also capture biogas through cogeneration to create renewable energy, this will reduce our electricity use and Sydney Water’s carbon footprint,” the spokesperson said.
When all three treatment facilities are fully operational by 2022, Sydney Water will have helped enhance the waterway health along South Creek and its tributaries, contributing to the sustainability and liveability of these fast-growing communities.
This program of works included the implementation of numerous sustainable innovations that will not only benefit these three treatment plants, but will also provide guidance for the rest of Sydney Water’s treatment facilities, as well as other water utilities.
There are two Australian-first technology/process innovations being implemented on the project:
Mechanical Primary Sedimentation (MPS) Screens and the transfer of biosolids sludge through a pipeline for consolidated biosolids processing at St Marys.
Mechanical Primary Sedimentation (MPS) Screens
This is an emerging technology that delivers reduced power consumption and greenhouse gas emissions due to reduced aeration requirements in the bioreactor. Pre-sedimentation takes place in a much smaller footprint, using few materials, odour control is more efficient, and the process is costeffective. Solids harvested in the MPS are anaerobically digested, producing biogas which can then be captured and converted into energy to offset operational energy demand.
The solid waste produced at the Quakers Hill WRP will be transported via an existing effluent pipeline to St Marys WRP, to provide the scale to beneficially recover the energy contained in the sludge. This delivers reduced power consumption and costs, and a significant reduction in greenhouse gas emissions due to reduced aeration requirements of the anaerobic digester, as well as biogas production enabling energy recovery. It is anticipated the energy recovery enabled by the anaerobic digester will allow for 70-90 per cent self-supply of electricity at St Marys, which is approximately 115,358GJ/year of biogas generating 13.3GWh of electricity.
There are also two process innovations being implemented on the project that are a first for New South Wales: Nereda Anaerobic Granulated Sludge (AGS) process and the Thermal Hydrolysis Process (THP).
The Nereda AGS process is fully automated, easy to operate with no moving parts, has low energy consumption and a small footprint. Clarifiers are not required for the AGS
process – treated effluent is decanted after a very short settling period. Therefore, substantially less concrete is used in construction, the footprint is much smaller, and the construction costs are substantially lower. The AGS process also uses about 25-30 per cent less energy and a conventional membrane type bioreactor, delivering significant greenhouse gas reduction for the project. The material savings compared to its base case will also result in about 25 per cent saving on concrete and steel. Quakers Hill WRP will have the largest installation of an AGS reactor in Australia, and the first in NSW.
This is a proven technology using steam or heat to break down biomass material prior to anaerobic digestion. The sustainability benefits include enhanced energy recovery (increased biogas production), reduced sludge quantities and a reduced digester volume. A drier cake and higher-grade biosolids would also be utilised closer to site, reducing transport costs. The reduced volumes of biosolids transported for disposal is a significant sustainability benefit of the THP. In addition, the THP results in a pathogenfree and stabilised biosolids product that can be applied directly to land with
potential for further drying to fertiliser or biofuel pellets. It also eliminates odour problems associated with the treatment of organic materials. With THP at St Marys, biosolids can potentially be reused within the Sydney basin, which would significantly reduce transportation.
The Sydney Water spokesperson said the four innovative wastewater process technologies described will deliver significant energy and carbon savings for Sydney Water, and help pave the way to a more sustainable water services industry.
Energy and carbon forecast modelling for the project estimates that the Lower South Creek Treatment Program will achieve a reduction of 870,000 tonnes or 42 per cent of total greenhouse gas emissions during construction and across its 50 years’ operation. This reduction includes embodied CO2 emissions from construction materials and treatment chemicals.
On-site renewable energy use is a core objective of the Lower South Creek Treatment Strategy, with the consolidated solids processing at St Marys implemented to allow for anaerobic digestion and energy
recovery through a cogeneration plant. With on-site thermal energy recovery and electricity generation, the project is able to self-supply more than 70 per cent of its electricity demand.
It was these outcomes that helped achieve the program’s IS rating, which is more impressive considering the IS rating was initially undertaken for this project only as a benchmarking exercise.
“The IS rating was an opportunity to benchmark Sydney Water’s sustainability performance with the wider industry. This demonstrated our planning and design processes are robust. We identified and considered options, challenged thinking and past practices, and have ultimately adopted innovative wastewater treatment technologies that are more sustainable,” the spokesperson said.
“We are continually striving to find better ways of working so our customers are guaranteed world-class water and wastewater services. Sydney Water will continue
to monitor the cumulative effect these improvements have on our environment and the added benefit to our customers.”
The Lower South Creek Program is Sydney Water’s first project to trial the Infrastructure Sustainability Council of Australia’s IS Rating tool and certification process. This process has provided independent third-party assurance of sustainability outcomes in the delivery of the project.
Ainsley Simpson, CEO of Infrastructure Sustainability Council of Australia, said, “This is the highest IS rating ever achieved for a water infrastructure project and includes numerous innovations and sustainable outcomes which other water utilities can follow and learn from. A tremendous achievement for Sydney Water.”
Sydney Water said it is focused on providing world-class water services
to the Greater Sydney region while striving to minimise its impact on the environment, a feat achieved by continually challenging current processes and exploring new ways of operating.
“In order to do so, it’s important we continue to adapt and evolve, benchmark our current processes against the wider infrastructure industry and identify areas for further improvement, so we can gain insight into how things can be done differently,” the spokesperson said.
“This project demonstrates the benefits that can be achieved for an operator, the community and the environment when standard approaches are challenged, and new technologies and ways of thinking are embraced. The project has proven how the investigation of opportunities in the feasibility and concept phase allows for thorough investigations to be undertaken to identify and implement the best solutions available on the market.”
of Future Fuels Collaborative Research Centre – the industry-focused Research, Development & Demonstration (RD&D) partnership enabling the decarbonisation of Australia’s energy networks
Australia is actively investigating affordable, reliable low-carbon energy for all of its total energy needs as well as for future clean-energy export potential. Achieving this requires solutions that go well beyond renewable electricity.
We need to consider the optimal energy solutions for homes, businesses, transport and industrial sectors which account for 40 per cent of our current energy market, currently serviced mainly by gaseous and liquid fuels.
Decarbonisation can present many opportunities and the gas sector is well placed to provide reliable and secure energy and cost-effective carbon reductions.
We have the opportunity to adapt existing gas infrastructure for the production, transport, storage and use of more sustainable future fuels, including hydrogen and biogas and their liquid derivatives such as liquid hydrogen, ammonia and methanol.
All of these fuels can meet a significant part of local demand and generate export opportunities. Importantly, they also have the potential to be fully scaled up to meet the needs of Australia’s energy markets.
Future Fuels CRC research provides knowledge for the public, industry and government to make informed decisions on our energy future. Our research is focused through three integrated research programs:
• Fuels Technologies, Systems and Markets focuses on understanding the technical, commercial and market barriers to, and opportunities for, the use of hydrogen, biogas and other future fuels
• Social Acceptance, Security of Supply and Public Safety studies the social and policy context, including public acceptance and safety, for technology and infrastructure associated with low-carbon fuels
• Network Lifecycle Management identifies and addresses gaps in relevant Australian industry codes and standards associated with design, construction and operation of existing and future gas networks
Existing gas energy network infrastructure can store the same amount of energy as six billion Powerwall batteries and currently services five million homes, 130,000 businesses and powers mining and manufacturing.
Successful adaptation of this existing gas network infrastructure, industrial equipment and household appliances to use future fuels provides an efficient transition pathway to low-carbon energy with lower implementation barriers, and this represents a major economic benefit for Australia.
Recent studies in Australia (Deloitte) and the UK (KPMG) concluded that conversion to future fuels could offer a considerably more cost-effective decarbonisation route than full electrification. Repurposing Australia’s existing infrastructure for future fuels will lower the overall cost of emission reduction and energy supply, and will significantly benefit the productivity of our national infrastructure.
The use of gas infrastructure to store excess renewable electricity for delivery at peak demand will also improve the integration of variable renewable generation, providing benefits in terms of both generation efficiency and energy grid security. Providing more options for end users for lowcarbon energy at competitive prices will broaden consumer choice and security of supply.
Supporting Australia’s Gas Vision 2050, Future Fuels CRC’s research is enabling the Australian gas industry to provide a competitive, low-carbon energy alternative for residential, commercial, industrial and transport sectors to complement and support renewable electricity generation. With targeted investment in research, development and demonstration, Australia can lead in this emerging field and benefit from the resulting technology and knowledge.
Future fuels are already technically feasible today with some large-scale deployment challenges that the Australian industry is now addressing:
• Research is still needed to ensure the reliable introduction of future fuels and to ensure the worldclass safety levels that the Australian market expects.
Australian industry must also keep abreast of fastmoving global developments to utilise these quickly and effectively
• Appropriate national policy, regulation and standards are being developed
• The potential social, economic and environmental impacts of future fuels and related infrastructure are being researched now and need to be quantified and communicated to address any public concerns during the transition to new fuel types
• Detailed confirmation is needed that all types of existing infrastructure can be repurposed to safely and reliably transport future fuels on a large scale. This includes understanding how to maximise the serviceability and life of new and existing infrastructure when it uses future fuels
New fuels, such as biogas and hydrogen, have the potential to become mainstream and complementary energy solutions that will use existing energy infrastructure. Biogas can make use of landfill or agricultural and forestry waste to produce a net-zero emissions fuel.
Hydrogen can be produced through electrolysis using renewables and then stored or moved to customers via the gas pipeline networks.
These integrated solutions help to address the intermittency of renewable energy sources and enable a secure transformation to a net-zero emissions energy system.
The storage of renewable energy in the form of hydrogen provides both short-term gas and longer-term storage of energy, capable of meeting daily energy variations as well as major interseasonal storage needs over much longer time periods.
Australia is already testing hydrogen blended into natural gas supplies in a series of demonstration projects led by Jemena, ATCO and Australian Gas Networks (AGN).
In February 2020, the Federal Government’s Australian Renewable Energy Agency announced it would support the Australian Hydrogen Centre (AHC) to scale up these projects.
The AHC is developing feasibility studies to inject up to ten per cent renewable hydrogen into the gas distribution network of selected regional towns in South Australia and Victoria.
Building on the feasibility studies for regional towns, the AHC will also develop feasibility studies to inject up to ten per cent renewable hydrogen into the gas distribution networks of South Australia and Victoria and develop a pathway to make the transition to 100 per cent hydrogen networks.
AGN’s flagship project, Hydrogen Park South Australia (HyP SA) will be operational by mid-2020. It will be Australia’s largest renewable hydrogen production facility, where
renewable hydrogen will be produced and blended into the gas distribution network in Mitchell Park, Adelaide.
Approximately 710 households in Mitchell Park will be receiving a blended five per cent renewable gas – a combination of natural gas and renewable hydrogen. By December 2021, AGN is also planning to bring online a hydrogen plant in Gladstone, Queensland, to deliver up to ten per cent blended hydrogen across the city’s total 770 residential, small commercial and industrial customer base.
In the long term, entire networks may be converted to pure hydrogen or mixtures of hydrogen and biogas. This will require some modifications to existing gas appliances, but a suitable transition program would minimise the cost and impacts on consumers.
Each of the feasibility projects already have their own engagement strategies for end users, local communities and first responders, and they are seeing early, positive responses.
COAG Energy Council commissioned a series of reviews, studies, research and analysis to inform Australia’s National Hydrogen Strategy including research on 'Developing Community Trust in Hydrogen' led by Professor Peta Ashworth of the University of Queensland who is a lead researcher in Future Fuels CRC.
The report documents current knowledge of the social issues surrounding hydrogen projects. It reviews leading practice stakeholder engagement and communication strategies, and findings from focus groups and research activities across Australia.
Future Fuels CRC’s collaborative research is outcomes focused and driven by our unique range of participants from industry, research and government.
We are fortunate to have the Energy Networks Association, Australian Pipeline and Gas Association, and Gas Appliance Manufacturers Association Australia as active participants, with over 60 Australian companies behind them.
Every research project has an industry adviser to provide support and guidance. This means the end user is always top mind in our research, ensuring we deliver their real-world needs including driving change in industry standards and software development.
Sewer maintenance chambers that are damaged and leaking not only put a strain on the environment, but also on local authorities and their communities. Billions of euros are spent every year across Europe on the renovation of wastewater infrastructure, with the costs of repairing a concrete manhole ranging between 3,000 and 5,000 euros*, approximately AUD$5,400-$9,000.
Concrete chambers can suffer from multiple types of damage including dynamic stress, corrosion, water leakage and limited life spans.
REHAU’s AWASHAFT maintenance holes offer a new, innovative approach to mitigate these common problems.
Every AWASHAFT is made out of pure, high-quality polypropylene, without any of the recycled materials or fillers you can find in other synthetic chambers. The benefit of using a pure material is a perfect balance between high levels of stiffness and impact strength. That means that cracks do not occur at all, making it immediately watertight.
* IKT comparative test manhole renovation,2016.
The AWASHAFT ladder steps are made of glass-reinforced plastic, a corrosion-resistant material. This means that 22 per cent of the damage that has plagued sewer chambers until now will not even develop**
The polypropylene used in AWASHAFT is also resistant to aggressive substances with pH values of 1 to 13, including biogenic sulphuric acid corrosion, making it suitable for the drainage of aggressive industrial waste and able to quickly absorb temperatures of up to 90°C.
Every AWASHAFT also comes with a 100-year life span and a ten-year warranty for peace of mind.
The AWASHAFT is incredibly lightweight – up to 95 per cent lighter than a concrete chamber. That means installers won’t need heavy duty machines to help with installation – two people is plenty! This also speeds up the process, reducing installation time by 25 per cent.
Unlike concrete, there is no need for a make-up ring when adjusting the height of the AWASHAFT. The height adjustment can be simply achieved by shortening the plastic cone and the bearing ring is inlaid into the road’s base course. If the road settles, the bearing ring will settle with it, meaning the cover will not start to jut out.
There are generally heavy costs associated with concrete manholes, driving the progressive increase in demand for a cost-effective alternative.
Modern injection moulding technology reduces the costs of a synthetic chamber, and installation of a REHAU chamber made of pure polypropylene is 37 per cent*** more affordable than its traditional counterpart.
With the background knowledge that the material component only makes up ten per cent of the total cost of the construction, the additional costs of acquisition become negligible. For more information, visit awashaft.myrehau.com
** DWA (German Association for Water, Wastewater and Waste) study about the state of sewage systems in Germany 2015.
*** Technical article in the magazine 'Strassen und Tiefbau, June 2013
Lifting access covers is a strenuous, high-frequency task that utility field workers need to undertake, and is a significant contributor to serious injury and lost time. With over 40,000 access covers in its service area, Icon Water went searching for a solution to help protect the safety and musculoskeletal health of its workers.
However, after trialling several existing products and not finding one that met all of its needs, Icon Water undertook its own research and development, and has designed the Cracker Jack, an innovative solution to the sector-wide problem.
Access covers come in a range of styles and connections, and will typically weigh between 25-125kg. When they become stuck – a problem that frequently occurs – they often require loads greater than 200kg to crack, which can result in significant dynamic loads being placed on workers, and leading to long-term musculoskeletal damage.
While there are a range of methods available to crack and lift access covers, field workers will commonly do so manually using a T bar or other similar means, to help them lift the lid and drag it off of the maintenance hole. However, this is hard work, and with some of Icon Water’s field workers lifting 20 access covers a day, they can be lifting over a ton and a half every day.
While this is a lot of weight, field workers are used to lifting heavy loads, so in the short term it may not cause a problem. However, the issue is with the frequency associated with lifting this amount of weight, as in the long term it will lead to musculoskeletal issues and lost time.
Eric Nielsen, Senior Mechanical Engineer at Icon Water, said Icon Water searched for a solution to protect the safety and health of its field workers, trialling a number of existing mechanical solutions, but found them to be cumbersome or slow to set up, and heavy or ineffective across the many types of terrain that workers typically encountered.
“Access covers are in people’s
backyards, in garden beds, on the side of hills, they’re everywhere. So while most solutions available are really good for flat, concrete surfaces such as in a water treatment plant or a flat road where there are no gradients, as soon as they are on grass or in a muddy environment, we found that they just didn’t suit our needs.
“This is because the ones we trialled took a significant amount of time to set up, weighed 20+ kilograms and struggled to function in the different types of terrain and scenarios our field workers often encounter.”
With no suitable alternative available on the market, and the industry as a whole struggling with the problem, Icon Water decided to invest resources into the development of a bespoke lifting device that could overcome common pain points, including being able to work on a variety of surfaces, gradients and loads, as well as being lightweight and easy to use.
Icon Water’s Engineering Services team took a research and development style approach to solving this problem. This involved rapidly developing and testing concepts, through the use of Autodesk Inventor to trial different kinematic scenarios, as well as through building component/sub-assembly level prototypes as quickly as possible.
This design methodology was a departure from how design is usually delivered at the utility, which is typically completed by external resources for water assets rather than products. This meant significant upskilling of staff was required, as well as a high level of engagement with end users right from the beginning of the project.
“Using an R&D style process, we were able to design, build, test and iterate, before going back to the start to see what worked, what didn’t and then modify the design to try it again. This process allowed us to arrive at a solution pretty rapidly, as opposed to spending a lot of time designing and not knowing if what we were doing would work. We did a lot of designing, building and testing to prove concepts rapidly and then implement them or modify them as necessary,” Mr Nielsen said.
A key step in the design process was analysing the different situations and reasons behind field workers needing to lift access covers.
“We realised that around 60 to 70 per cent of the time, a lot of the field workers are lifting access covers just to inspect the inside. So they're not actually removing the access cover to gain access and get into the maintenance hole,” Mr Nielsen said.
Mr Nielsen said the team decoupled the two functions of lifting and removing the cover to come up with a solution that can significantly reduce loads on the user. In the event that the user wants to simply inspect inside the cover, they crack the access cover using the Cracker Jack and use an IP camera like a GoPro connected to a selfie stick and iPad to look inside the maintenance hole. This takes less than a minute and requires no load from the user. When the user needs to remove the access cover for entry, they crack the cover, drop it onto a bespoke roller and then simply roll it off, which also requires little effort and minimal time from the user.
Weighing only 10kg, the CJ is a novel, lightweight, portable system for lifting access covers. With a working load limit of 500kg, it significantly reduces loads on the user compared to manual lifting methods.
The CJ consists of a jack driven by a battery-operated power drill, a specialised roller and wifi camera system. The jack and wifi camera allow users to quickly crack and inspect inside access covers without any load from the cover being placed on them.
When the access cover needs to be removed, the jack and specialised roller
can be used to crack and remove the lid with minimal effort.
The system has been tested and proven to work with all types of access cover, terrain and gradients that field workers often encounter.
Mr Nielsen said the main benefits of the CJ are that it’s easy on the musculoskeletal system, it doesn’t require a lot of force and is quick to use.
“Workers can use it to crack an access cover, and take a look into the maintenance hole in about a minute, and if the lid needs to be cracked, it can crack and roll it off within two minutes,” Mr Nielsen said.
“In that instance, you can see the major benefit between something that weighs 23kg, takes five minutes to use and takes a significant amount of effort and work on the operator’s behalf to actually employ versus the CJ, which you can set up in a minute and crack the manhole with no effort.
“In one test, the CJ was used on a steep, slippery driveway to crack and remove an 80kg circular cover in approximately one minute, which placed a peak momentary 15kg load on the user. If this had been done manually, it would have taken less time, however there would have been significantly more load placed on the user (peak momentary load of 80kg).”
Mr Nielsen said Icon Water is continuing to trial the CJ in its operations and plans to release the design via its website, allowing other water utilities across Australia to use its innovative solution, and help improve the design and methodology for safely lifting access covers.
“We're at the point now where we're releasing a final prototype to the field workers to use. So we're getting multiple Cracker Jacks made, and our field workers will continue to use it and give us feedback,” Mr Nielsen said.
“We're also going to release the design documentation to the market and other utilities without any licensing associated with it, so other utilities can pick it up, with the aim of benefiting the backs of many.”
Piping Speciality Supply Service (PSSS) is a dedicated supplier of specialised machinery, tooling and consumables to the pipeline, energy, water and infrastructure sectors, across both steel and HDPE pipe.
PSSS offers a full selection of tools and equipment for HDPE pipeline construction projects, including butt fusion machines. PSSS supplies machines from two of the world's leading manufacturers, McElroy and WeldMaster, offering customers both rental and purchase options for their projects.
The McElroy range of Tracstar rental machines are the T500, T630 and T900, covering pipe sizes ranging from six inches to 36 inches (150m-900m).
The T500 made its debut in 1997 and was instrumental in the development of the entire Tracstar line of fusion equipment. These machines are self-contained, with an on-board generator powering the heater, self-propelled and suitable for all types of terrain. Their serrated jaws and inserts keep pipes from slipping during the fusion process.
The Tracstar models have a powerful hydraulic face which helps weld even the toughest pipes with ease. The heater and facer can easily be converted to top loading for work in confined spaces. The wireless remote control ensures a safe, efficient working environment and precise machine placement.
The WeldMaster butt fusion machines are an alternative to McElroy’s smaller range.
The fully automatic WeldMaster range of BFM 180, BFM 250, BFM 315 and BFM 400 cover pipe sizes from 2.5 inches to 16 inches (63m-400m). Hy-Ram has designed and manufactured the high-quality WeldMaster butt fusion equipment for the global market since the early 1980s.
The WeldMaster range takes the fully automatic machine to the next level in terms of control, quality, connectivity, usability and smart technology features.
All four of these machines have seven inch touch screens with integrated RFID readers for monitoring training status and operator ID, menu-driven data entry, on-board diagnostics software and early warning error messages.
Additional features include Bluetooth and USB connectivity, an embedded GPS for precise weld location and internal memory for an excess of one million joint records.
PSSS can provide very competitive prices for the purchase of these machines, however if rental fits better into your budget, the majority of models are available from its current rental fleet. All rental machines are fully mine compliant and with Australia-wide shipping, PSSS is your genuine partner in all things piping.
For further information, please contact 1300 794 096 or sales@psssa.com.au to get in touch with the PSSS team – “we are here to help”.
Did you know that manhole rehabilitation has been a challenge for councils and water authorities for over 2,500 years?
One of the directors of Alternative Lining Technologies recently visited the ancient city of Jerash in Jordan. Known for its magnificent Roman city, Jerash is so well preserved you can almost feel the people walking to the forum!
While taking in the wonder of this world heritage site, imagine his surprise to find a manhole in the main street, complete with a brass ring to allow for access.
The Romans invented subterranean sewer systems and, even then, understood the importance of wastewater management. They were truly a civilisation ahead of its time, and there is good reason that the Roman Empire ruled for as long as it did.
Now, 2,500 years later, underground sewer systems are still built in a very similar way to how they were back then. All components of the sewer system are critical to the safe and efficient transfer of waste to a place where it can be safely managed.
Manholes are just as important now as they were back then and so is preserving them.
With so much focus on the pipe in network rehabilitation, the range of products available to adequately rehabilitate manholes has previously been limited.
However, Alternative Lining Technologies’ Cured in Place Manhole (CIPM) systems can be customised to suit virtually any shape manhole, pump well or other underground structure.
Alternative Lining Technologies’ CIPM has been used in the US for over 20 years. Unlike coatings, it provides a structural solution that features:
• Zero reliance on the sewer maintenance structure substrate condition
• Acid-resistant PVC surface
• Fast installation process
• 50-year plus lifetime solution backed by 20year warranty
CIPM liners add years of serviceability to aging sewer structures while also saving tens of thousands of dollars through rehabilitation rather than reconstruction.
Alternative Lining Technologies has completed installations of CIPM within the Melbourne Water, Yarra Valley Water and South East Water catchment areas in Victoria.
Alternative Lining Technologies and delivery partner, Abergeldie Complex Infrastructure, are now installing CIPM across Australia and New Zealand.
Find out more at www.altliner.com.au.
Trees can pose a significant threat to the safety and reliability of electricity networks. Now the impact of a changing climate on vegetation, including an increase in bushfires, looks set to become the greatest risk to the management of network assets. A new collaborative project by Endeavour Energy and NM Group is using spatial analysis and sophisticated model building to map current vegetation, see how fast it is growing towards powerlines and identify potential hazards posed by specific trees, creating a sophisticated risk-based vegetation management program to combat these challenges.
The need for holistic vegetation management programs has increased for Australian utilities as they start to face even more threats to their networks. On average, 84 homes are lost to bushfires each year and CSIRO research suggests climate change will lead to increases in ‘very high’ and ‘extreme’ fire danger rating days, and earlier starts to the fire season, which we’ve already experienced in late 2019.
Looking at New South Wales specifically, studies have projected that the probability of extreme fire risk will increase by around 25 per cent by 2050.
These predictions are especially worrying for energy utilities that have network infrastructure in high bushfire risk areas, including Endeavour Energy, who has around 12,000km of overhead powerlines running through Greater Western Sydney, the Blue Mountains, the Southern Highlands and the Illawarra region of New South Wales. In order to be on the front foot of these risks and ensure the safety of customers and continuity of supply, Endeavour created a project to better understand the dynamics of vegetation on its large, dispersed electricity distribution network.
The aim of the project was to create a holistic multi-year picture of vegetation threats to its electrical network, so it can not only identify current hazards, but see how these will change in the future, and put steps in place to proactively manage them.
Working with electrical network technology service company, NM Group, the project used spatial analysis and model building to combine multi-temporal LiDAR data with data from other sources including historical meteorology and vegetation work patterns, as well as actual observations of tree fall.
They used cloud processing to process these massive datasets and create localised models which described where vegetation was situated, how fast it was growing towards powerlines and the potential hazards posed by individual trees based on a predictive index.
The findings are being used to inform the works undertaken by Endeavour’s maintenance team so they can target specific areas for ongoing inspection trimming and tree removal works. Making maintenance operations more targeted allows the utility to better manage network risks while minimising costs and increasing asset management efficiencies.
In effect, these efficiencies help keep downward pressure on its network charges while still maintaining a safe and reliable power supply to customers.
Phase One of the project occurred in 2018 and involved a significant amount of research and collation of numerous datasets from multiple sources. This was in addition to field work where measurements and observations from over 400 trees across 43 sites were collected.
Both in the field and using a desk-based inspection of the LiDAR data, the location of tens of thousands of fallen trees was also pinpointed. Using the principle that by analysing and understanding patterns of past tree fall we can begin to identify areas at higher risk of tree fall in the future, this provided one half of the dataset that was used during a machine learning process to identify vegetation, soil, terrain and weather scenarios most likely to contain tree fall hazards.
The aim of this phase was to investigate if LiDAR could identify trees that had the potential to fall onto the electricity network, with a view to developing a risk-based approach in the management of hazard trees.
In doing this, the project was able to:
• Unlock the value in LiDAR data
• Develop vegetation inventory (canopies)
• Understand tree clearance per bay and establish program/contract compliance
• Understand growth analysis to estimate the rate of vegetation growth towards the wires and how long until non-compliance
• Identify hazard trees/fall-in risk – which trees were likely to fail and their locations
• Identify risk vs investment opportunities
This process produced a rich GIS database for the utility, as well as detailed reports on vegetation growth and fall risk. These included breakdowns on historical patterns of growth rate span and predictions for the next five years, as well as guidance on individual trees in terms of the relationship of that tree to the nearby span – including its ability to fall onto a powerline and the size of the overstrike in the ranked likelihood of the tree to fall.
The project findings noted a pattern match between previously fallen trees and trees identified in the model from the LiDAR data of up to 80 per cent accuracy.
This was an impressive result, especially considering the many diverse factors affecting tree fall which may not have been incorporated into the modelling. The findings were also verified and field tested by a specialist independent group and validated by Endeavour Energy specialist arborists.
Phase Two of the project began in 2019 and is currently ongoing. It is looking at environmental parameters to determine how quickly trees responded to a shift in climate. The large computing power generated from NM Group will input a variety of open source datasets, Endeavour Energy LiDAR, contractor cutting records and specialist Visual Tree Assessments (VTA) from the utility’s tree management officers.
In this phase, Endeavour Energy is currently reviewing:
• All results to align with standardised risk matrices of likelihood and consequence
• Whole-of-network LiDAR outputs as opposed to only the bushfire analysis
• Provision of ‘strings’ which are the 3D representations of the powerline catenaries
The aim of this is to have a sound grasp of environmental parameters to predict how vegetation is likely to respond to these changes in climate.
The plan is to also introduce key metrics to evaluate post-cut clearances and use machine learning (AI) to optimise program delivery ahead of bushfire season. The results of this model will be finalised by June 2020.
The utility is also reviewing the scope for implementation of model testing, which will form Phase Three.
Using spatial analysis technology has shown that datasets, from LiDAR through to tree trimming records, can be used to design a risk-based vegetation management program. This data can then help utilities reduce operating costs.
Endeavour Energy is now able to target specific trees that require specialist resources and inspections, and can identify potential hazards that might otherwise have been missed.
Preventive maintenance schedules can also be created around predicted vegetation growth rates, so specific areas aren’t being over or under serviced.
The Endeavour Energy and NM Group project team plans to continue to refine and extend their technical capabilities and improve the way that the data can be collected, integrated and shared. The plan is to then roll out this technology to other parts of the network that might not be in a bushfire risk area.
After this summer’s record-breaking bushfire season, businesses, community groups and the Royal Commission have started to discuss the next steps to ensure we are not unprepared for next year. From that, one key consideration that utility providers need to take into account is excess vegetation close to powerlines and the role it potentially plays in sparking and exasperating these fires. It’s clear that drastic clearing efforts should be undertaken now to ensure our 2020-21 summer is safer for all Australians.
The Black Summer of 2020 was one of the worst bushfire seasons Australia has endured, especially for New South Wales in terms of the intensity, area burned and the number of properties lost, and had a devastating effect on many communities around Australia.
As of March 2020, the fires burned an estimated 18 million hectares, destroyed over 5,900 buildings and killed at least 33 people. An estimated one billion animals have been killed and some endangered species may be driven to extinction.
At its peak, air quality dropped to hazardous levels, while the cost of dealing with the bushfires is expected to exceed $5 billion dollars.
As temperatures drop, and efforts move from fighting fires to rolling out funding and support for those who have been impacted by the fires, we also need to look more closely at the steps we can take to mitigate future bushfire risks in Australia.
One issue that has been raised during the Black Summer fires has been the role vegetation management has to play in mitigating bushfire risks.
In February 2020, the Federal Government announced that a national Royal Commission into Australia’s 2019-2020 Black Summer bushfires would be established, with it to report
its findings by the end of August.
One of the issues the Royal Commission has been tasked with investigating is the question of whether Australia could harmonise aspects of land and vegetation management, like hazard reduction burns.
Vegetation around powerlines is a cause of bushfire sparking in Australia, and it’s critically important that utilities stay on top of this.
According to Dr Simon Dunstall, Research Director of the Decision Sciences Program at Data61, “Powerline-initiated bushfires do happen, and they’re more likely to be large and fatal. Over 80 per cent of bushfire fatalities in Australia since 1950 have been due to fires initiated on high-voltage (HV) distribution powerlines.”
One of the most basic mitigations utilities can take against the threat of powerline-initiated bushfires is to manage the vegetation around their powerlines – and after the Black Summer fires we’ve just experienced, it’s more important than ever that utilities get on the front foot.
We only need to look at the case of Californian electricity and gas network service provider Pacific Gas & Electric Co, which filed for bankruptcy in January 2019. The company saw two-thirds of its value stripped from it, with blame largely attributed to poor vegetation management practices and unsuitable asset design, following the
impacts of the 2018 bushfire season in California.
According to Greg Parkinson, Vermeer’s QLD Product Specialist for Environmental Equipment, we can expect to see increased requirements when it comes to managing vegetation in bushfire-prone areas and around powerlines.
“Most definitely, we will see governments looking at building firebreaks and clearing corridors that are considered a fire risk,” Mr Parkinson said.
Vegetation management is an enormous job in Australia, especially when areas of coverage can be in the millions of square kilometres.
“Vegetation management around power assets typically requires the removal and processing of vegetation both large and small,” Mr Parkinson said.
“The key is finding a contractor with highly productive and versatile equipment that will enable them to get more done, quicker, while maintaining a high quality of work.”
Global equipment manufacturer Vermeer has an extensive range of wood chippers and whole tree chippers – the crucial link in the processing of cleared vegetation – which have been developed to deliver efficiency and
ease of operation, with operator safety paramount.
“Our wood chippers range from 8 inch x 6 inch capacity all the way up to 38 inch x 27 inch capacity. We have the most diverse range of machines that can handle basic pruning and trimming all the way up to tree removal,” Mr Parkinson said.
“We pride ourselves on the productivity, safety and ease of operation of our machines.
“The end product from our wood chippers is also a consistent, saleable product, which is perfectly suitable for use as an organic mulch in gardening, landscaping or restoration ecology.
“As we move out of one horrific
bushfire season, and into the planning phase for our next one, contractors will be well equipped to get ahead of the curve. When thinking about the vegetation management works you need to undertake to create a safer environment, think about the role a high-quality wood chipping machine can play in these efforts.”
Trenchless technologies enable the installation and rehabilitation of underground utility infrastructure with little to no excavation, minimising the impact on the environment and reducing community disruption. Water Corporation, the principal supplier of water, wastewater and drainage services to over two million people throughout Western Australia, is utilising trenchless technology to deliver improved water and wastewater services to its customers.
Water Corporation continues its ongoing program of work to refurbish wastewater pipes across Western Australia to extend the life of this important infrastructure by at least 50 years.
The latest areas to be refurbished through the program include 12.5km of wastewater mains in Northam, 750m in Wagin and 950m in Gnowangerup.
Where practicable, Water Corporation uses trenchless technology to reline wastewater pipes, minimising the disturbance to the community and the environment.
Unlike traditional pipe replacement, relining involves accessing the wastewater mains via access chambers instead of open trenches. The technology works by inserting a plastic strip liner inside an existing wastewater pipe via access chambers that is then wound down the length of the pipe route. The wound plastic liner is then expanded to fit tightly within the walls of the existing pipe to provide a smooth finish.
Work began in Northam in December 2019, progressing to Wagin then Gnowangerup, with the project expected to be finished by late 2020.
Relining wastewater pipes is important as it not only helps prevent corrosion and reduce blockages, but it also helps protect the local wastewater systems and the health of the community and environment.
Since 2015, Water Corporation has refurbished around 65km of wastewater mains through the program, to ensure a reliable wastewater service into the future.
Wastewater is 99.97 per cent water, as it comes mostly from showers, baths and washing machines.
Water Corporation manages more than 17,000km of wastewater mains across Western Australia and collected 165 billion litres of wastewater in 2018-19. A total of 1,178 pump stations transport wastewater to 122 treatment plants across the state, where wastewater is treated and safely returned to the environment.
Water Corporation also operates 75 recycled water schemes across Western Australia, which not only reduce reliance on precious drinking water for irrigation, but also provide an environmentally-friendly way of disposing of the community’s wastewater.
Sections of Perth’s water main network are over 100 years old and, like anything of that age, they’re starting to show some wear and tear.
Through Pipes for Perth, Water Corporation is renewing these aging water mains to reduce the likelihood of future breaks and leaks, and the disruption this may cause to commuters, residents and businesses.
Water Corporation undertook a comprehensive study of its water main network to see which streets needed to be renewed.
As the older pipes tend to have the highest priority for renewal, most of the work over the past few years has taken place in Perth’s oldest and most established suburbs, but it has also included other areas where pipes have been assessed as needing replacement.
While the original water mains in the late 1800s and early 1900s would have been laid by digging trenches by hand, and transporting sections of main using a horse and cart, it is a little different today.
The pipes are made of PVC (polyvinyl chloride) or PE (polyethylene) materials used worldwide for water mains for their strength, flexibility, durability and ease of installation.
PE water pipes in particular are often installed using trenchless construction techniques such as ‘microtunnelling’ and ‘horizontal directional drilling’, due to their capacity to be joined together in long ‘pipe strings’ for insertion under railway lines, major roads, rivers, and other locations where trenching is not appropriate.
An innovative relining technology can sometimes be used to renew the water mains. Pits are excavated every few hundred metres and a new PE pipe is then ‘pulled’ into the existing main from one pit to the next, breaking apart the old pipe and forming a new water main in the same location as the old.
Pit locations for trenchless and relining techniques are selected to minimise disruption to road users, businesses and residents, with traffic maintained in both directions where possible.
Since July 2016, Water Corporation has renewed over 120km of water mains across the Perth metropolitan area.
When it comes to microtunnelling projects, there are a number of factors that determine whether a pipeline installation is successfully installed the first time, including the experience of the contractor, pre-planning and having the right equipment.
But what we see most commonly in projects that run into trouble part way – or have trouble finding a contractor to take it on – is that there is a lack of accurate information to identify and confirm ground conditions at the site.
Understanding the prevailing ground conditions at the site is extremely important on a microtunnelling project as it will help determine what drill head will be used. However, while geotechnical information should be provided at the start, it is not uncommon for it to be incorrect. This is through no fault of anyone – core samples and geotechnical inspections are like looking for a needle in a haystack. This is because you are just looking at a small sample, and what you see may not reflect the conditions even a short distance away. When you install a pipeline though, you pass every metre of ground from one point to another, so if there are any changes in the ground along that route, you’re going to find them.
The problem with this is that the drill head needs to be selected to best match the ground conditions, otherwise there’s a high chance that you will need to stop the drill part way through to change out the head if there is a significant change in ground conditions. However, most microtunnelling machines don’t have the ability to retract, so a hole will need to be dug from above the drill head to swap it out, adding time and cost to the project – and that’s as long as no other problems occur.
If the area is known to have, or the geotechnical information shows, difficult ground conditions, project managers may also find it difficult to find a contractor willing to take on the job due to the high risk of problems occurring.
Having state-of-the-art equipment is one way to mitigate
the risks of changing or difficult ground conditions. While most machines are designed to only move in a forward direction, the AXIS is designed to retract. This allows the contractor to perform a pilot line, inspect the ground conditions and select the best drill head before committing to the final jacking.
This feature also means that if something does change part way through the drill, the head can be retracted and the contractor can reassess the next steps.
We have found this feature invaluable, allowing us to take on jobs that no one else can or wants to, and complete jobs successfully and with minimal risks.
In one instance, the geotechnical survey indicated the ground was sandy clay, but when drilling started, we found that it was actually wet sand with clay bits. The original contractor had been unable to complete the installation because of this as they were using a vacuum style machine which isn’t suitable for wet ground as the drill head will drop. This led to project delays. We were called in to help and after completing a pilot line, we were able to select the correct drill head, advise on the best pipe materials and complete the project successfully.
In another example, they were having trouble finding a microtunnelling contractor willing to do the job due to the ground conditions being known to be difficult and high risk. Our pilot line showed us that there was more rock with seams of clay through it, as well as partial fracturing, then the geotechnical survey suggested. These conditions are particularly difficult due to the potential for wedging to occur. But armed with all the information and knowing how the AXIS reacts to these ground conditions, we were confident we could install the pipeline successfully – and we did.
By making sure you have all the right information from the start and having equipment that can retract to change out the drill head if required, you’re mitigating a lot of the risks that will prevent you from having a successful installation the first time.
ABOUT STUART HARRISONGlobal microtunnelling pioneer Stuart Harrison is the Managing Director of Edge Underground, where he specialises in on-grade microtunnelling installations with millimetre accuracy.
Stuart is also the inventor of the Vermeer AXIS Guided Boring system, and he is constantly working to improve the effectiveness of this and other trenchless systems used in the installation of gravity sewers.
To discuss your next microtunnelling installation, contact Stuart on 1300 JACKED or at stuart@edgeunderground.co
I f the re ’ s one t hin g you don’ t want to take a chance on, it’s the ability of yo u r DC power system to protect your critical a sse t s. O ur D C power sy stem s are designed to meet Australian standards and to delive r maxi mu m longevity. By custom designing every s y stem, w e provide en gi ne ered sol u t ions t hat me et t h e unique tech nical re quirements of yo u r si te. T h is in n ovat ive ap proach combined with our maintenance support m eans we le ave no t h ing to c h anc e when it comes to protecting you r cri ti ca l a sse t s.
To le arn more about our DC power systems and ma intenance ser v ices, v is it o u r website.
F or enquiries call 1300 364 877 www.intelepower.com.au
November 18 -20, 2020
Platinum Sponsor:
Join colleagues from across the Oceania region for the 2020 Oceania Damage Prevention Conference. This event educates stakeholders on damage prevention and safe excavation while showcasing best practices and international learnings on damage prevention efforts for underground assets and essential infrastructure.
“It is the first conference that’s brought together a large international contingent to learn about damage prevention and help develop our industry in both Australia and New Zealand.”
- Innes Fisher, Utility Location Services Ltd
“The knowledge sharing… is what it’s all about.”
– Neil Weatherly, APA Group
Share your industry knowledge and be recognized as an expert in your field by telling an exceptional story, addressing a concern specific to one or more stakeholder group, providing distinctive training or education, and/or promoting the damage prevention message in a unique way.